PA66GF’s Role in Aerospace Engineering
Polyamide 66 glass fiber reinforced plastic, known as PA66GF, has gained prominence in the aerospace sector for its exceptional mechanical properties, superior temperature resistance, and lightweight nature. Aerospace engineers rely on these attributes to design components that adhere to the industry’s rigorous standards. One of the critical aspects is PA66GF’s high strength-to-weight ratio, enabling the creation of robust yet lightweight parts suitable for the demanding conditions of flight.
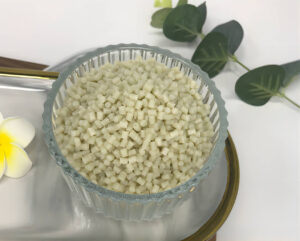
Optimizing Material Orientation and Layup
To maximize the benefits of PA66GF, engineers must meticulously choose the material’s orientation and layup pattern. The glass fibers within PA66GF can be aligned in specific directions to enhance various mechanical properties like tensile and flexural strength, and impact resistance. For instance, a unidirectional layup boosts tensile strength significantly, whereas a bidirectional layup enhances flexural strength. Selecting the appropriate layup pattern allows designers to customize the material properties to fulfill specific aerospace design needs.
Addressing Thermal Stability in High-Temperature Environments
Its high glass transition temperature makes it suitable for high-temperature aerospace applications. However, moisture can influence its thermal expansion coefficient, potentially causing dimensional changes and decreased performance. To counteract this, it’s crucial for designers to ensure components are adequately sealed and shielded from moisture, maintaining stability and performance under varying thermal conditions.
Ensuring Electrical Insulation and Moisture Resistance
Given PA66GF’s excellent electrical insulating properties, it is an ideal choice for applications requiring electrical isolation. Nevertheless, exposure to moisture can compromise these electrical properties, increasing conductivity. Designers must implement effective sealing solutions to prevent moisture infiltration, thus preserving the material’s insulating capabilities and ensuring consistent electrical performance.
Enhancing Reliability and Durability Through Surface Finish
The aerospace industry demands high reliability and durability from its components. For PA66GF parts, selecting the appropriate surface finish and texture is vital. A smooth surface finish can minimize wear, while a textured surface can enhance grip and reduce slippage. Thoughtful selection of these characteristics ensures that the components can withstand the operational stresses and meet the stringent reliability and durability standards of aerospace applications.
Navigating Processing and Manufacturing Techniques
It can be shaped using various methods such as injection molding, compression molding, and 3D printing, each with its own advantages and constraints. Designers must evaluate and select the most appropriate processing technique to align with the required component specifications. Moreover, rigorous inspection and testing are necessary to verify that the finished components comply with quality and performance standards set by the aerospace industry.
Comprehensive Design Strategy for PA66GF Components
In summary, designing aerospace components with PA66GF requires a holistic approach, considering factors like mechanical properties, thermal stability, electrical insulation, surface finish, and manufacturing techniques. By thoroughly evaluating and optimizing these aspects, engineers can develop components that meet the demanding requirements of aerospace applications, ensuring reliability, performance, and longevity.
FAQ: PA66GF in Aerospace Applications
- What is PA66GF?
PA66GF, or Polyamide 66 Glass Fiber Reinforced, is a composite material made by combining polyamide 66 (a type of nylon) with glass fibers. This blend results in a material that offers enhanced mechanical strength, high temperature resistance, and reduced weight, making it ideal for demanding applications such as those in the aerospace industry.
- Why is PA66GF commonly used in aerospace applications?
It is favored in aerospace due to its high strength-to-weight ratio, which allows for the construction of lightweight yet robust components. Additionally, its resistance to high temperatures and excellent mechanical properties make it suitable for the extreme conditions encountered in aerospace environments.
- How does the orientation and layup pattern of PA66GF affect its properties?
The orientation and layup pattern of the glass fibers within it significantly impact its mechanical properties. A unidirectional layup enhances tensile strength, while a bidirectional layup improves flexural strength. By choosing the appropriate fiber orientation, designers can tailor the material’s properties to meet specific performance requirements.
- What are the thermal properties of PA66GF and how do they influence its use?
It has a high glass transition temperature, which means it can maintain its structural integrity at elevated temperatures. However, its thermal expansion can be influenced by moisture, potentially leading to dimensional instability. Proper sealing and moisture protection are necessary to maintain its performance in high-temperature applications.
- How does PA66GF perform as an electrical insulator?
It is a good electrical insulator, making it suitable for aerospace applications where electrical isolation is required. Nevertheless, moisture can degrade its insulating properties, so it’s crucial to ensure components are well-sealed to prevent moisture ingress and maintain electrical performance.
- What considerations are there regarding the surface finish and texture of PA66GF components?
The surface finish and texture of its components are important for their durability and functionality. A smooth surface can reduce wear and tear, while a textured surface can improve grip and prevent slippage. Selecting the right surface characteristics ensures that components meet the aerospace industry’s stringent reliability and durability standards.
- What are the common processing and manufacturing techniques for PA66GF?
It can be processed using methods like injection molding, compression molding, and 3D printing. Each technique has unique advantages and challenges. For example, injection molding allows for high-volume production with consistent quality, while 3D printing offers flexibility in design and rapid prototyping. Selecting the right processing method depends on the specific requirements of the component.
- How do designers ensure the quality and performance of PA66GF components?
Designers ensure quality and performance through rigorous inspection and testing. Components made from it must meet the aerospace industry’s high standards for strength, thermal stability, and electrical insulation. This often involves detailed quality checks during and after the manufacturing process to confirm that components adhere to the necessary specifications.
- What challenges are associated with using PA66GF in aerospace applications?
Challenges with it include managing its moisture sensitivity, which can affect its thermal and electrical properties, and ensuring the proper orientation and processing to achieve desired mechanical characteristics. Additionally, selecting the right surface finish and processing technique can be complex, requiring careful consideration of the specific application needs.
- Can PA66GF be used in applications outside of aerospace?
Yes, it is also utilized in automotive, industrial, and consumer goods sectors due to its versatile properties. Its strength, lightweight nature, and resistance to high temperatures make it suitable for a wide range of applications beyond aerospace.