Introduction
Driven by the dual forces of lightweight automobiles and Industry 4.0, PA6 (polyamide 6) is becoming the fastest growing engineering plastic in the world with an average annual growth rate of 5.3%. This semi-crystalline thermoplastic material has become the first choice in key areas such as gears, bearings, and automotive parts due to its high strength, wear resistance, and chemical corrosion resistance. This article will deeply analyze the five core technologies and reveal how to release the ultimate performance of PA6 through precise process control.
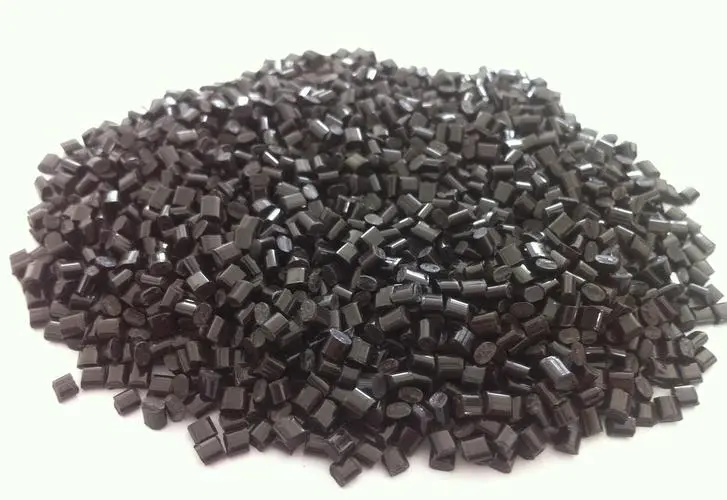
1. Material pretreatment: moisture control determines success or failure
The hygroscopicity of PA6 is a “double-edged sword” in its processing – undried materials will cause defects such as bubbles and silver streaks in the finished product. Experiments show that when the moisture content exceeds 0.2%, the tensile strength will decrease by 18%. Key process parameters:
- Drying temperature: 80-100℃ closed-loop system (30% better than traditional hot air drying)
- Drying time: 16-24 hours (dynamically adjusted according to ambient humidity)
- Dew point control: <-40℃ (to prevent secondary moisture absorption) Industry leaders such as Arburg have developed intelligent drying systems that monitor moisture content in real time through the Internet of Things, reducing the scrap rate to below 0.5%.
2. Precision injection molding: the art of temperature field
Injection molding accounts for 67% of the PA6 processing market, and its core technology lies in temperature gradient control:
- Melt temperature: 230-280℃ layered control (front section 230℃/middle section 250℃/nozzle 280℃)
- Mold temperature: 80-90℃ constant temperature system (temperature difference within ±2℃ to ensure crystallinity consistency)
- Pressure curve: 750-1250bar multi-stage injection technology The servo electric injection molding machine of KraussMaffei in Germany uses real-time adjustment through the in-mold pressure sensor to make the tooth profile accuracy of PA6 gears reach DIN 5 standard.
3. Reinforcement and modification: the key to performance breakthrough
PA6-GF30 reinforced with 30% glass fiber has a bending modulus of up to 9500MPa, which is 400% higher than pure PA6 (data source: DuPont technical report). The latest technology trends include:
- Nanoclay reinforcement: Adding 3% nano-montmorillonite increases the heat deformation temperature by 25°C
- Carbon fiber hybrid: 15% chopped carbon fiber + 15% glass fiber to achieve isotropy
- Self-lubricating modification: Adding MoS₂ or graphene, the friction coefficient is reduced to 0.08 PA6+carbon fiber composite materials developed by Victrex have been successfully used in aerospace hydraulic components, increasing their service life by 3 times.
4. Mold innovation: the battle of micron-level precision
Optimized mold design can shorten the molding cycle by 20% while improving dimensional stability:
- Hot runner system: reduce melt retention and avoid thermal degradation
- Conformal cooling water channel: 3D printing mold achieves ±0.5℃ temperature uniformity
- Exhaust structure: 0.03mm stepped exhaust groove design Case: Japan [Fanuc] (https://www.fanuc.com) uses in-mold induction heating technology to make the surface roughness of PA6 automotive connectors reach Ra0.8μm.
5. Post-processing process: the second leap in performance
- Annealing treatment: 120℃×4h annealing, eliminating internal stress, and improving dimensional stability by 30%
- Humidity conditioning: 48h equilibration in 65%RH environment, and 50% increase in impact strength
- Surface modification: Plasma treatment makes the coating adhesion reach 5B grade Protolabs‘s automated post-processing line can realize unmanned operation of the entire process of PA6 parts from molding to packaging.
Conclusion
From drying pre-processing to intelligent post-processing, PA6 processing technology is evolving towards digitalization and high precision. By mastering these five core technologies, companies can maximize the potential of PA6 – while maintaining cost competitiveness, the tensile strength exceeds 85MPa and the heat deformation temperature reaches 180℃. As an industry benchmark, Fuchen New Material‘s PA6/PA66 blend has passed IATF 16949 certification. Its innovative low warpage formula is redefining the performance boundaries of automotive parts.
Contact Fuchen’s technical team now to get customized PA6 processing solutions and start your new era of high-performance manufacturing!