Introduction
In today’s industrial landscape, choosing the right material can make all the difference in product performance, durability, and cost-effectiveness. ABS (Acrylonitrile Butadiene Styrene) and PA (Polyamide, commonly known as Nylon) are two popular thermoplastics widely used across various industries, from automotive to consumer electronics. Understanding the differences between ABS and PA is crucial for manufacturers, engineers, and product designers who seek to balance functionality with economic viability. ABS vs PA, this article explores the key distinctions, properties, and applications of ABS and PA to help you make informed material choices.
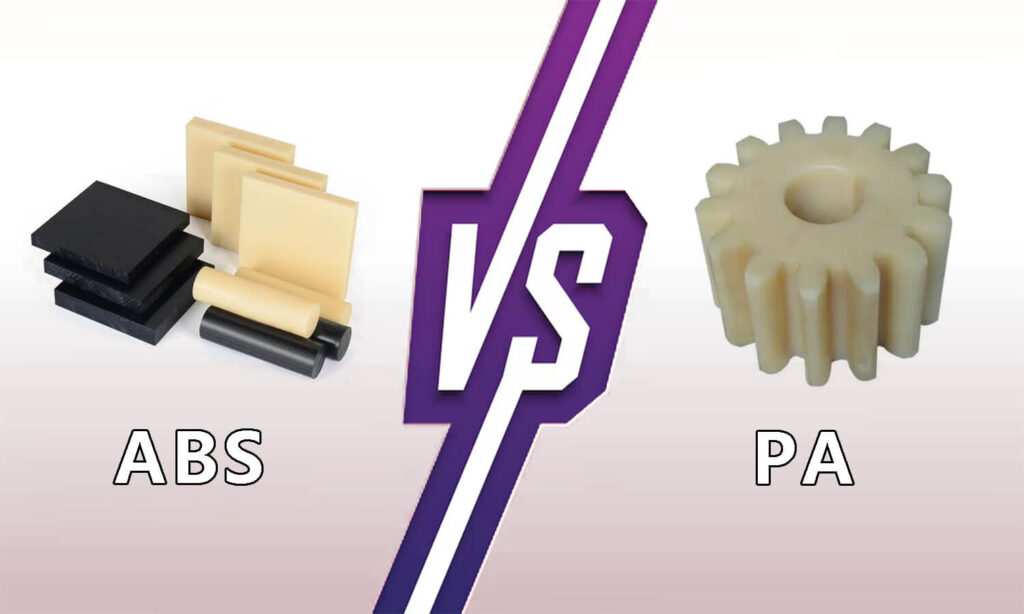
ABS – Features and Applications
Definition and Composition of ABS
ABS is a copolymer made by combining acrylonitrile, butadiene, and styrene, resulting in a durable plastic known for its robustness, impact resistance, and cost-effectiveness. This composition allows ABS to be molded easily, making it ideal for complex designs and detailed shapes.
Key Properties of ABS
ABS is prized for its mechanical strength, toughness, and resistance to scratches and dents. It also has good dimensional stability and can withstand moderate heat and environmental factors, though it is not suitable for high-heat applications.
Common Applications of ABS
Automotive Industry: ABS is used extensively in car interiors, dashboards, and trim components, where durability and ease of manufacture are priorities.
Consumer Electronics: The casing for many electronic devices, such as laptops, phones, and remote controls, is made from ABS due to its lightweight and impact-resistant nature.
Household Appliances: From vacuum cleaners to refrigerator shelves, ABS is a popular choice for components that require rigidity and durability under frequent use.
PA – Features and Applications
Definition and Composition of PA (Nylon)
Polyamide, commonly referred to as Nylon, is a type of synthetic polymer derived from petroleum. It is known for its strong fiber structure, which gives it high tensile strength, flexibility, and resistance to abrasion.
Key Properties of PA
PA’s strength and resilience, along with its excellent chemical and wear resistance, make it highly suitable for demanding applications. It can withstand high temperatures and is often used in environments requiring mechanical strength under stress.
Common Applications of PA
Engineering and Industrial Applications: Due to its high durability and resistance to wear, PA is frequently used in gears, bearings, and machine parts.
Textile Industry: Nylon is a staple in the textile industry, found in clothing, upholstery, and sportswear for its flexibility and toughness.
Consumer Goods: Everyday items like toothbrush bristles, fishing lines, and packaging materials benefit from PA’s resilience and versatility.
Detailed Comparison between ABS and PA
Mechanical Properties
Strength and Stiffness: PA generally has higher tensile strength and flexibility than ABS, which can make it more suitable for parts exposed to high stress and movement.
Impact Resistance: ABS is known for its superior impact resistance, making it a better option for applications requiring shock absorption.
Chemical Resistance
PA shows greater resistance to chemicals and solvents, especially against oils and greases, whereas ABS is more prone to degradation under chemical exposure.
Thermal Properties
ABS can withstand moderate temperatures, making it suitable for general-purpose applications, while PA’s higher thermal stability allows it to perform well in high-heat environments.
Cost Comparison
ABS is generally more cost-effective than PA, making it the material of choice for applications where budget constraints are significant and high-performance properties are not required.
Selecting the Right Material
Factors to Consider
Specific Application Requirements: The intended use plays a significant role. For high-stress applications, PA’s strength may be more suitable, while ABS offers greater affordability for low-impact uses.
Environmental Considerations: Consider the environment the product will be exposed to. PA is preferred in chemical-heavy settings, while ABS is ideal for low-exposure applications.
Decision-Making Process
Evaluating the application requirements, budget constraints, and environmental factors can guide material selection. Prototyping with both materials might also be beneficial to assess real-world performance.
Frequently Asked Questions (FAQs)
A. What are the main differences between ABS and PA?
ABS is known for its impact resistance and affordability, whereas PA is valued for its tensile strength, thermal resistance, and durability under stress. Each material has distinct advantages suited to different applications.
B. Which material is better for automotive applications?
ABS is often used in interior automotive parts for its moldability and cost-effectiveness, but for high-stress parts like gears and bushings, PA may be the preferred choice due to its strength.
C. Are ABS and PA recyclable?
Yes, both ABS and PA are recyclable. ABS can be melted and reshaped, while PA requires specific recycling processes due to its high melting point and toughness.
Conclusion of ABS vs PA
ABS and PA are both versatile thermoplastics with distinct properties that make them valuable in various applications. While ABS offers impact resistance and affordability, PA stands out for its strength, chemical resistance, and temperature tolerance. Choosing the right material depends on specific requirements, including mechanical needs, environmental factors, and budget constraints. By carefully considering these factors, businesses and manufacturers can optimize product performance, longevity, and cost efficiency. Selecting the appropriate material can lead to better product satisfaction, improved durability, and ultimately, a smarter investment.