Abstract
As a core material in the field of engineering plastics, modified nylon has become a pillar material in the automotive, electronics, medical and other industries with its excellent mechanical properties, heat resistance and designability. This article discusses the current situation and future of the modified nylon industry from the perspectives of industry technology development, application scenario expansion, environmental protection trends and post-maintenance, combined with market data and technical cases. By analyzing eight core issues, it reveals its technological innovation path and sustainable development potential, providing reference for industry practitioners and investors.
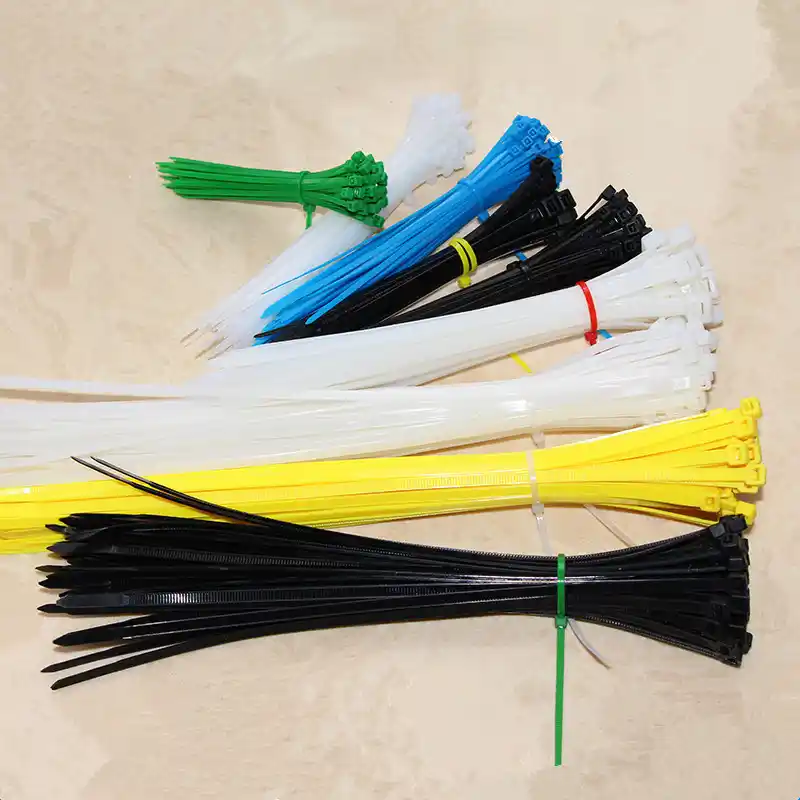
1. Technological innovation of modified nylon: from basic performance to functional breakthroughs
The core of modified nylon is to optimize its performance through physical or chemical means. For example, adding 30% glass fiber (GF) can reduce the molding shrinkage of PA66 from 1.5-2% to 0.3%, significantly improving dimensional stability. In recent years, the application of high-reinforcement materials (such as 50% GF-filled PA66) in the fields of automobile brake pedals has successfully replaced metal parts, achieving the dual advantages of lightweight and corrosion resistance. In addition, the development of halogen-free flame retardant technology (such as phosphorus nitrogen flame retardants) not only meets the V-0 fire protection standard, but also reduces smoke density, which is suitable for high-speed rail, aviation and other closed environments.
Technical case: The “silicon dioxide toughened modified nylon 6 composite fiber” recently developed by Wuhan Qishenming Technology has significantly improved the tensile strength through the synergistic effect of nano-silicon dioxide and polyvinyl alcohol, providing a new material option for aerospace parts.
2. Diversified expansion of application fields
- Automotive industry: Modified nylon is widely used in engine intake pipes, chassis fenders and other parts. PA66+30% GF material has become the first choice for turbocharger systems due to its temperature resistance of 140℃ and high toughness. Modified nylon accounts for more than 10% in Tesla Model Y, confirming its core position in the lightweight trend.
- Electronic appliances: Halogen-free flame-retardant PA66+35% GF is used for connectors, which has high fluidity and dimensional stability, meeting the needs of 5G equipment for precision parts.
- Medical field: PA66+15% GF is used for foot drop correctors and medical care beds due to its skin-friendliness and high load-bearing capacity.
III. Material transformation under the trend of environmental protection
The research and development of bio-based and degradable nylon has become the focus of the industry. In 2025, the global consumption of biodegradable modified nylon is expected to exceed 500,000 tons, of which the Asia-Pacific region accounts for 30%. For example, BASF’s Ultramid series can be used for a long time at 220°C through surface carbonization layer technology, reducing the problem of thermal oxidation aging. In addition, the use of recycled materials (such as PA6 waste silk particles) is strictly controlled within 25% to balance performance and environmental protection needs.
4. Fine control of production and processing technology
- Injection molding parameter optimization: The barrel temperature of PA6 and PA66 needs to be controlled above 220℃ and 250℃ respectively to avoid melt degradation.
- Mold design: Products with wall thickness > 3mm need to use 20-40℃ low-temperature molds, while glass fiber reinforced materials need mold temperature > 80℃ to reduce warping.
- 3D printing technology: The market size of 3D printing modified nylon is expected to reach US$1 billion in 2025. Boeing has produced more than 100,000 aviation parts, highlighting its customization advantages.
5. Post-maintenance and product processing technology
- Heat treatment: Use mineral oil or glycerin, treat at 10-20℃ above the use temperature for 10-30 minutes to eliminate internal stress and improve dimensional stability.
- Humidity adjustment: Potassium acetate solution (boiling point 121℃) can accelerate moisture balance. Products with a wall thickness of 6mm need to be treated for 16-18 hours to avoid performance degradation caused by environmental humidity.
VI. Market competition pattern and leading enterprise strategy
DuPont and BASF occupy 30% of the global market share, and their Zytel and Ultramid series dominate the high-end market. Domestic companies such as Shenma Co., Ltd. have won 15% of the domestic market share in the automotive field through the integration of the entire industrial chain. In terms of corporate strategy, mergers and acquisitions and R&D are equally important, such as BASF and Clariant’s merger to strengthen flame retardant technology, and Sinopec’s expansion of European and American markets through acquisitions.
VII. Industry challenges and response strategies
- Raw material fluctuations: Oil price fluctuations directly affect the cost of PA66. Enterprises need to buffer risks through long-term agreements and recycled material substitution.
- Environmental regulations: EU REACH regulations require strict control of flame retardants and plasticizers, and promote enterprises to turn to halogen-free and bio-based materials.
- Technical barriers: High glass fiber filling (>50%) requires bimetallic screw equipment, and domestic enterprises are under significant pressure to upgrade their equipment.
8. Future Outlook: Intelligence and Sustainable Development
- Nanotechnology: The addition of graphene and carbon nanotubes can further improve wear resistance and conductivity, and is suitable for smart wearable devices.
- Circular Economy: Chemical recycling technology of waste nylon (such as depolymerization and regeneration) will reduce carbon footprint, which is in line with the EU’s “Plastic Strategy” goals.
Summary
The modified nylon industry is undergoing a transformation from “performance optimization” to “functional innovation”, and its application boundaries are constantly expanding with technological progress. Despite the pressure of environmental protection and cost, the industry is expected to achieve breakthroughs in the fields of lightweight automobiles, precision electronics, and biomedicine through technological innovation, industrial chain integration, and green transformation. In the future, companies need to take sustainable development as the core, embrace intelligence and circular economy, and only then can they take the lead in this material revolution.
References