Application of Nylon Introduction
Nylon has become a critical material in the aerospace industry due to its unique properties and versatile applications. Its adoption has led to improved performance, cost efficiency, and technological advancements in aircraft and spacecraft manufacturing. This article explores the various ways nylon is transforming the aerospace sector.
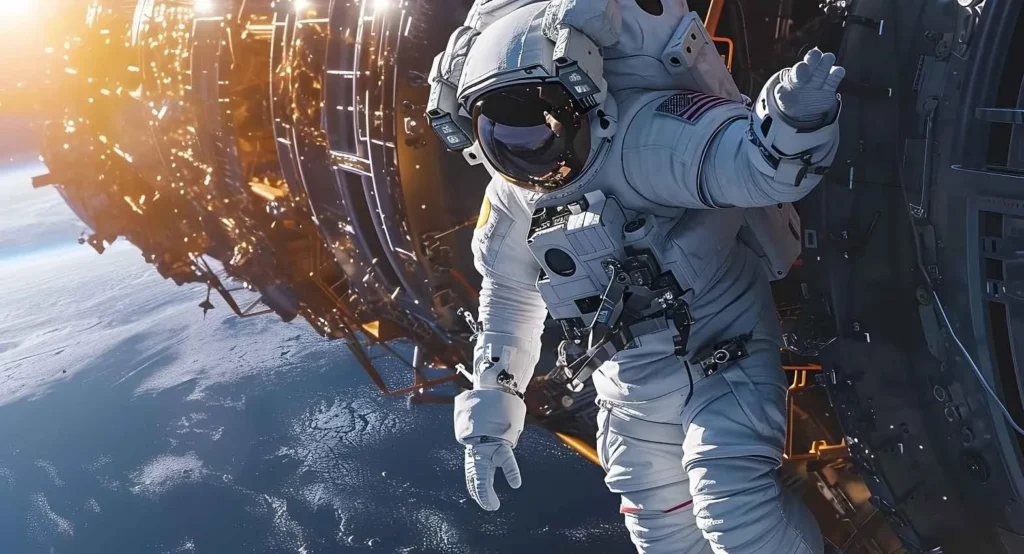
Strength-to-Weight Ratio: Key to Lightweighting
One of the primary reasons nylon is used in aerospace is its exceptional strength-to-weight ratio. This characteristic is crucial in aircraft and spacecraft design, where reducing weight enhances fuel efficiency and increases payload capacity. Nylon’s lightweight yet strong nature makes it ideal for various applications.
High Strength and Fatigue Resistance in Structural Components
Nylon’s resistance to fatigue and its ability to endure extreme conditions make it a top choice for structural components like fasteners, brackets, and engine mounts. These parts require durability in harsh environments, including exposure to high temperatures and vibration, areas where nylon excels.
Nylon-Based Composites: Strengthening Aerospace Design
The integration of nylon with materials like carbon fiber or glass fiber has resulted in high-performance composite materials. These nylon-based composites offer enhanced strength, stiffness, and impact resistance, which are essential for aerospace components such as fuselage panels, wing skins, and control surfaces. This has led to lighter, more fuel-efficient aircraft.
Seals and Gaskets: Ensuring System Integrity
Nylon’s high resistance to chemicals and extreme temperatures makes it perfect for seals and gaskets used in critical aerospace systems like fuel, hydraulic, and environmental control systems. These components help prevent fluid and gas leaks, ensuring the proper function of essential aircraft systems.
Enhancing Aircraft Interiors and Safety Equipment
Nylon is also extensively used in aircraft interiors, contributing to the development of seat belts, harnesses, and safety equipment. Its strength and abrasion resistance ensure that safety features are durable, while its comfort properties enhance passenger experience with durable seating and well-constructed compartments.
Nylon and Manufacturing Innovations: Pioneering 3D Printing
The application of nylon has driven advancements in manufacturing, including the development of 3D printing technologies. Nylon-based composites allow for the rapid and precise production of complex aerospace components. This innovation has streamlined manufacturing processes, significantly reducing production time and costs.
Application of Nylon Conclusion
The application of nylon in aerospace has revolutionized both design and manufacturing processes. With its excellent strength-to-weight ratio, high resistance to fatigue and corrosion, and capability to endure extreme temperatures, nylon has improved the efficiency, safety, and comfort of modern aircraft. As the industry progresses, nylon’s role is expected to expand further, contributing to the development of even more advanced and efficient aerospace technologies.
FAQ: Application of Nylon in the Aerospace Industry
1.Why is nylon used in the aerospace industry?
Nylon is widely used in aerospace due to its exceptional strength-to-weight ratio, resistance to fatigue, and ability to withstand extreme temperatures and corrosive environments. These properties make it ideal for reducing weight while maintaining structural integrity in aircraft and spacecraft.
2.What are the main applications of nylon in aerospace?
Nylon is used in various aerospace components, including fasteners, brackets, engine mounts, composite materials, seals, gaskets, seat belts, harnesses, and interior components like seating and luggage compartments.
3.How does nylon improve fuel efficiency in aircraft?
By reducing the weight of structural components through its lightweight nature, nylon contributes to improved fuel efficiency. Nylon-based composites further enhance this benefit by making aircraft lighter while maintaining strength and durability.
4.What role does nylon play in aerospace composites?
Nylon is often combined with carbon fiber or glass fiber to create high-performance composite materials. These composites are used in components like fuselage panels, wing skins, and control surfaces, providing improved strength, stiffness, and impact resistance.
5.How is nylon used in sealing systems?
Nylon’s high resistance to chemicals and extreme temperatures makes it an ideal material for seals and gaskets in fuel systems, hydraulic systems, and environmental control systems. These seals prevent leakage of fluids and gases in critical aerospace systems.
6.How does nylon contribute to passenger safety and comfort?
Nylon is used to produce safety equipment such as seat belts and harnesses due to its strength and abrasion resistance. It also enhances passenger comfort by being a durable material for seats and interior amenities like luggage compartments.
7.Has nylon influenced aerospace manufacturing technologies?
Yes, nylon-based composites have driven advancements in 3D printing technologies, allowing for the rapid and precise production of complex aerospace components. This has reduced manufacturing time and costs.
8.What is the future of nylon in aerospace?
As the aerospace industry evolves, the use of nylon is expected to grow. Its unique properties and role in advanced manufacturing techniques will likely lead to more efficient, safe, and comfortable aircraft.