Introduction of Nylon vs PP
In the world of synthetic polymers, nylon vs PP (polypropylene) stand out due to their widespread use and adaptability. These thermoplastic polymers share some similarities but also possess distinct characteristics that make them suitable for different applications. This article provides a detailed comparison between nylon vs PP, examining their properties, differences, and common uses.
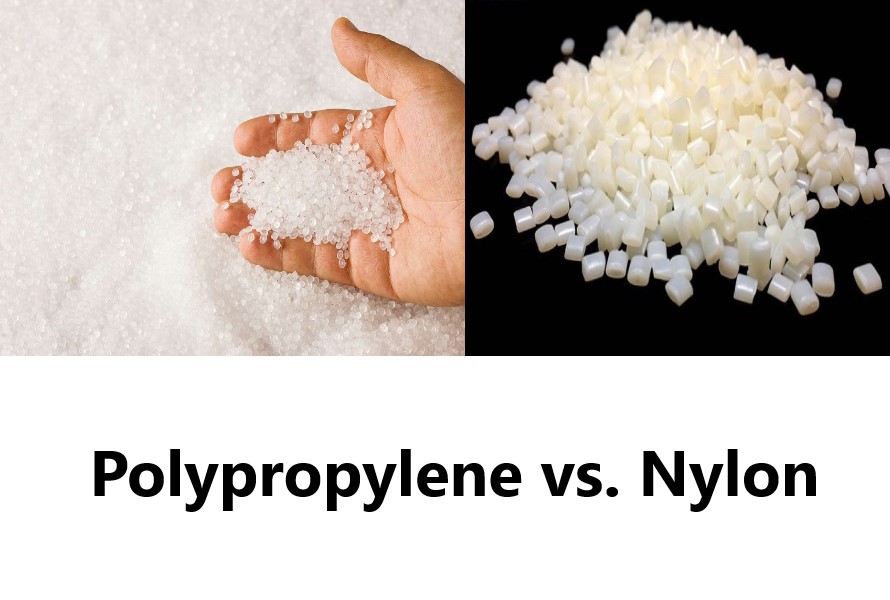
Overview of Nylon vs PP (Polypropylene)
Two Versatile Thermoplastic Polymers
Nylon and polypropylene are both thermoplastics, meaning they can be melted and reshaped multiple times without undergoing chemical changes. Despite this shared feature, each material exhibits unique properties that lend themselves to specific uses.
Characteristics of Nylon
High Tensile Strength and Abrasion Resistance
Nylon, a polyamide first synthesized in 1935, is recognized for its exceptional tensile strength, resistance to abrasion, and flexibility, even at low temperatures. Its self-lubricating property, due to amide groups, makes it an excellent choice for applications that demand low friction and wear resistance, such as gears and bearings. Additionally, nylon’s ability to absorb moisture makes it suitable for environments where moisture resistance is less critical.
Characteristics of Polypropylene
Chemical Resistance and Low Moisture Absorption
Developed in 1954, polypropylene is a thermoplastic polymer known for its high melting point, excellent chemical resistance, and minimal moisture absorption. Its low density, strong impact resistance, and superior electrical insulation properties make it ideal for applications in packaging, automotive components, and textiles.
Processing Differences Between Nylon and Polypropylene
Impact on Production Costs
One of the significant distinctions between nylon and PP lies in their processing requirements. Nylon, with its higher melting point and crystallization tendency, demands higher processing temperatures and extended cooling periods. In contrast, PP, with its lower melting point and crystallization tendency, is easier and faster to process, often resulting in lower production costs.
Chemical Resistance of Nylon vs PP
Suitability for Chemical Exposure
Nylon, while resistant to many organic solvents, is vulnerable to degradation by strong acids and bases. Conversely, PP exhibits excellent resistance to a broad range of chemicals, including acids, bases, and organic solvents, making it a preferred material for applications that involve chemical exposure.
Common Applications of Nylon vs PP
Matching Material to Application Needs
Nylon’s high tensile strength, flexibility, and self-lubricating properties make it ideal for products such as textiles, ropes, and fishing nets. Its abrasion resistance also makes it suitable for items like brushes and conveyor belts. On the other hand, PP’s low density, impact strength, and chemical resistance make it a prime candidate for packaging, automotive components, and textiles.
Conclusion of Nylon vs PP
In summary, both nylon and polypropylene are valuable thermoplastic polymers with distinct characteristics that make them suitable for specific applications. Nylon’s high tensile strength and abrasion resistance make it ideal for uses that require low friction and durability. In contrast, polypropylene’s low density, impact strength, and chemical resistance make it a better choice for applications involving chemical exposure and lightweight components. Understanding these materials’ properties is essential for making informed decisions when selecting the right polymer for a given application.
FAQ: Nylon vs PP(Polypropylene)
1.What are Nylon and PP?
Nylon and PP are both thermoplastic polymers that can be melted and reshaped multiple times without undergoing chemical changes. They are widely used in various applications due to their distinct properties.
2.What are the key properties of Nylon?
Nylon is known for its high tensile strength, excellent abrasion resistance, and flexibility, even at low temperatures. It has a self-lubricating property, making it suitable for applications requiring low friction and wear resistance.
3.What are the key properties of Polypropylene?
Polypropylene has a high melting point, excellent chemical resistance, and low moisture absorption. It is lightweight, has good impact strength, and provides excellent electrical insulation.
4.How do Nylon and PP differ in processing?
Nylon requires higher processing temperatures and longer cooling times due to its high melting point and crystallization tendency. Polypropylene, on the other hand, has a lower melting point and is easier and faster to process, making it more cost-effective.
5.Which material is more resistant to chemicals?
Polypropylene exhibits better chemical resistance compared to nylon. While nylon is resistant to many organic solvents, it is susceptible to degradation by strong acids and bases. Polypropylene resists a wider range of chemicals, including acids, bases, and organic solvents.
6.What are common applications of Nylon?
Nylon is commonly used in textiles, ropes, fishing nets, gears, bearings, brushes, and conveyor belts due to its strength, flexibility, and abrasion resistance.
7.What are common applications of Polypropylene?
Polypropylene is used in packaging, automotive components, and textiles due to its low density, impact strength, and chemical resistance.
8.Which material should I choose for my application?
The choice between nylon and PP depends on the specific needs of your application. Nylon is better suited for applications requiring low friction and wear resistance, while polypropylene is ideal for those involving chemical exposure and the need for lightweight components.