Zinc oxide: the hidden champion of nylon material upgrade
Abstract Zinc oxide has become one of the key technologies for high-performance nylon through nano-modification and synergistic effects. This paper systematically analyzes the mechanism of zinc oxide in enhancing the mechanical properties, flame retardancy, thermal stability and dimensional accuracy of nylon, and combines patented technology and industrial cases to reveal how it promotes the transformation of “plastic replacing steel” in the fields of automobiles and electronics.
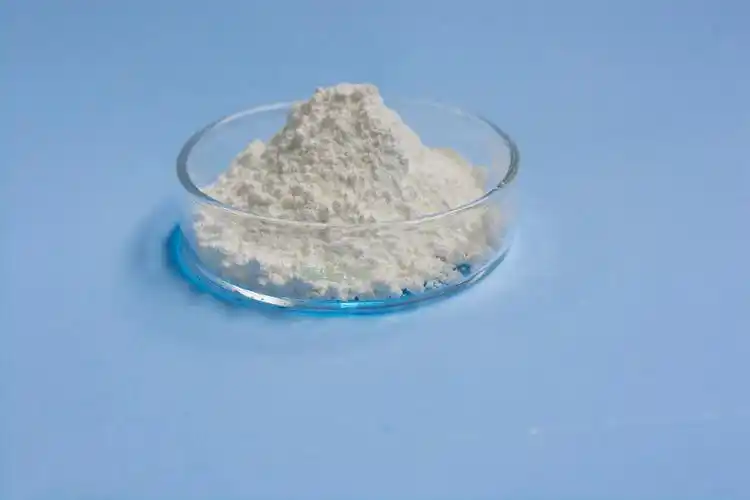
1. Mechanical property enhancement: from molecular bonding to network construction
The core of zinc oxide to enhance the strength of nylon lies in the physical-chemical dual action mechanism. At the physical level, the four-needle zinc oxide whiskers (surface modified with silane coupling agent) form a three-dimensional network skeleton in the nylon matrix, effectively transmitting stress and limiting molecular chain slippage. At the chemical level, its surface hydroxyl groups form hydrogen bonds with nylon amide groups to enhance the interface bonding force.
- Patent Evidence: Shanghai Kingfa Technology’s nylon composite material patent shows that adding 15-25 parts of modified zinc oxide whiskers (with a mass ratio of 1:1.2~1.9 to glass fiber) can increase the tensile strength by 78.84% and the impact strength by 14.49% compared with pure nylon.
- Process Key: Accurately control the extrusion temperature (240-260℃) through melt blending to avoid high temperature yellowing and ensure the integrity of the network structure.
2. Flame retardant performance breakthrough: “Repairer” of carbon layer structure
Nano zinc oxide plays a unique synergistic role in the intumescent flame retardant system (IFR) to solve the carbon layer cracking defect of traditional flame retardant nylon.
- Mechanism Revealed: Zinc oxide catalyzes the graphitization of the carbon layer during combustion to form a dense and continuous barrier. Experiments show that a 2.0% addition increases the limiting oxygen index (LOI) of nylon 66 by 11.19%, reaching UL94 V-0 level; excessive addition destroys the carbon layer structure.
- Microscopic evidence: SEM observations show that cracks in the modified carbon layer are reduced by 80%, the heat insulation and oxygen isolation efficiency are significantly improved, and the molten droplets are effectively suppressed.
3. The guardian of thermal stability and dimensional accuracy
Automobiles and electronic components require nylon to maintain dimensional stability at high temperatures, and zinc oxide achieves a breakthrough by inhibiting the thermal motion of molecular chains.
- Increase in thermal deformation temperature: 2% nano zinc oxide cooperates with glass fiber to reduce the thermal expansion coefficient of nylon 66 to 3.2×10⁻⁵/℃, and the warpage deformation is reduced by more than 50%, meeting the needs of engine peripheral parts to withstand a 130℃ environment for a long time.
- Crystallization regulation: Zinc oxide acts as a nucleating agent to accelerate nylon crystallization and improve the dimensional accuracy of the product. A certain car pedal accessory uses zinc oxide modified PPA (polyphthalamide), and the tolerance of injection molded parts is controlled at ±0.05mm. After replacing aluminum alloy, the cost is reduced by 17%.
4. Dispersion technology: the key to performance optimization
The agglomeration problem of nano zinc oxide is the key to performance. The industry has achieved breakthroughs through surface modification and process innovation:
- Compound coupling agent technology: Jiangsu Borui Optoelectronics uses dopamine hydrochloride to modify nano powders, combined with trishydroxymethylaminomethane solution dispersion, and the agglomeration rate is reduced to less than 5%.
- In-situ polymerization process: Hangzhou patent CN116355280B develops ethylene glycol system dispersion liquid, which is directly added in polyester synthesis, and the dispersion uniformity is improved by 30%, ensuring the stability of the mechanical properties of the material.
5. Application scenario expansion: “Plastic instead of steel” practitioners
Zinc oxide modified nylon has replaced metal materials in the field of high-end manufacturing:
- Automobile electric pedal: Through the reaction of zinc oxide modified PPA and carboxylated attapulgite to construct a mesh structure, the impact resistance is 31% higher than that of unmodified nylon, and the service life reaches 150,000 kilometers.
- Electronic connector: The volume resistivity of nylon 66 with the addition of nano zinc oxide is increased by 2 orders of magnitude, while maintaining dielectric strength (>20 kV/mm), which is suitable for the heat dissipation requirements of 5G equipment.
6. Sustainability: A new fulcrum for circular economy
The combination of zinc oxide-modified nylon and recycling technology promotes the green manufacturing process:
- Recycling compatibility: INVISTA’s ammonia solution process can decompose nylon 66 waste containing zinc oxide into monomers, with a recycling rate of 92%, and a 12% reduction in the carbon footprint of recycled materials.
- Economic benefits: Toray’s supercritical hydrolysis technology combined with modified nylon closed-loop recycling can obtain a carbon tax subsidy of 300 euros per ton of recycled materials, and the cost is 20% lower than that of virgin materials.
Summary: The “invisible revolution” of zinc oxide and future challenges
Zinc oxide promotes the upgrade of nylon from general plastics to engineering materials through mechanical enhancement, flame retardant synergy, and thermal stability improvement. The current technical focus is on:
- Dispersion process optimization: Supercritical fluid technology solves the problem of nano-agglomeration;
- Green recycling closed loop: Chemical depolymerization technology is compatible with zinc oxide fillers to achieve high performance of recycled nylon;
- Intelligent production: Online monitoring of melt flow rate (fluctuation ≤±0.5g/10min) to ensure batch stability.
In the future, with the surge in demand for new energy vehicle corona-resistant materials, 3D printing precision consumables, etc., the innovative application of zinc oxide in nylon will continue to rewrite the material rules of high-end manufacturing.
Odkazy
- Shanghai Kingfa Technology Nylon Composite Material Patent (CN118290932B)
- Research on Mechanical Enhancement of Nylon 66/OMMT/SiO₂ Nanocomposites
- Toray VS INVISTA: Nylon 66 Recycling Technology Competition (Environmental Microworld)
- Flame Retardant Synergistic Mechanism of Nano Zinc Oxide (Insulation Materials)
- Borui Optoelectronics Highly Dispersed Aluminum Nitride Powder Patent (CN119899036A)
- Nylon Composite Material Patent for Automobile Pedals (CN119242027A)