Introduction of Polyamide 11
Polyamide 11, commonly referred to as PA11, is a distinctive polymer that has found favor in a variety of industries, including automotive, aerospace, and medical sectors. Its unique combination of properties, such as high tensile strength, elongation, impact resistance, and excellent chemical resistance, makes it an invaluable material for numerous applications. However, to fully leverage the benefits of PA11, one must understand how to properly handle, process, and troubleshoot issues associated with this material. This guide aims to provide essential insights into working with PA11 to ensure optimal performance and efficiency.
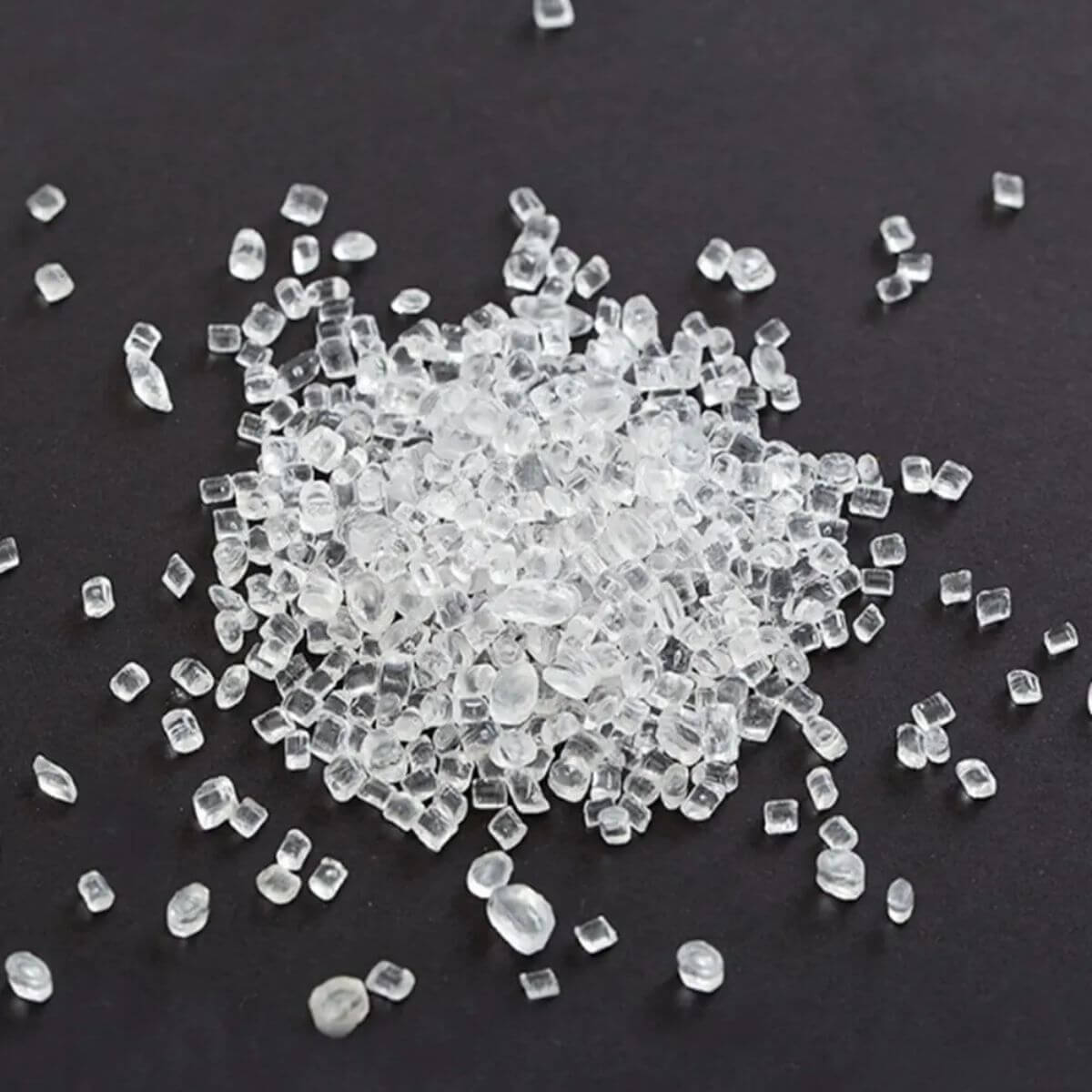
Understanding the Properties of PA11
Semi-Crystalline Nature and Mechanical Excellence
Polyamide 11 is a semi-crystalline polymer, meaning it consists of both amorphous and crystalline regions. This dual structure endows PA11 with remarkable mechanical properties, including high tensile strength and elongation, which contribute to its robustness and durability. Its impact resistance further enhances its appeal for applications where mechanical stress is a concern.
Chemical Resistance and Versatile Applications
Another standout feature of PA11 is its exceptional chemical resistance. This property makes it suitable for use in environments where exposure to chemicals is a concern, such as in the automotive, aerospace, and medical industries. PA11’s ability to withstand harsh chemicals without degrading ensures its longevity and reliability in demanding applications.
Proper Storage and Handling of Polyamide 11
Maintaining Optimal Storage Conditions
To preserve the integrity of PA11, it is crucial to store it in a cool, dry environment. Exposure to direct sunlight and moisture can degrade the polymer, leading to potential issues during processing and in the final product. Ensuring that PA11 is kept in a controlled environment helps maintain its quality and performance.
Handling with Care to Prevent Damage
When handling PA11, careful attention must be paid to avoid scratches and contamination. Any physical damage or foreign particles can adversely affect the quality of the final product. Implementing gentle handling practices and using clean equipment can mitigate these risks, ensuring that the polymer remains in optimal condition for processing.
Techniques for Processing Polyamide 11
Injection Molding: Precision in Complex Shapes
Injection molding is the preferred technique for producing complex and precise parts from PA11. To achieve the best results, it is essential to utilize a well-designed mold and maintain precise control over processing parameters such as temperature, pressure, and injection speed. These factors directly influence the quality and accuracy of the molded parts.
Extrusion: Crafting Profiles, Sheets, and Tubes
Extrusion is another popular method for processing PA11, particularly for manufacturing continuous profiles, sheets, and tubes. This process involves forcing the polymer through a die under high pressure, which shapes the material into the desired form. Proper temperature and pressure control, along with an accurately designed die, are key to a smooth and successful extrusion process.
Blow Molding: Creating Hollow Parts
For producing hollow parts like bottles and containers, blow molding is an ideal technique. In this process, a heated preform is placed in a mold, and air is blown into it to expand and shape the material. Achieving the desired part quality and shape requires meticulous control over temperature, air pressure, and mold design.
Troubleshooting Common Issues of Polyamide 11
Addressing Surface Finish Problems
Poor surface finish is a common issue encountered when working with PA11. This problem can often be traced back to suboptimal processing parameters or mold design. Adjusting the temperature, pressure, or injection speed, and ensuring the mold is clean and properly maintained, can help improve the surface finish of the final product.
Mitigating Warping and Discoloration
Warping and discoloration are other challenges that may arise during PA11 processing. Warping typically results from uneven cooling or residual stresses within the material. To prevent warping, it is important to maintain uniform cooling and optimize the processing conditions. Discoloration can be caused by excessive heat or contamination and can be addressed by controlling the processing temperature and ensuring clean handling practices.
Conclusion of Polyamide 11
Working with Polyamide 11 (PA11) demands a deep understanding of its unique properties and the adoption of precise handling and processing techniques. By maintaining proper storage conditions, carefully managing the material during processing, and addressing potential issues through effective troubleshooting, you can harness the full potential of this versatile polymer. Whether in the automotive, aerospace, or medical industries, mastering the art of working with PA11 can lead to the creation of high-quality, reliable products that meet stringent performance requirements.
FAQ: Working with Polyamide 11 (PA11)
1.What is Polyamide 11 (PA11)?
Polyamide 11, or PA11, is a semi-crystalline polymer known for its excellent mechanical properties, high tensile strength, elongation, impact resistance, and exceptional chemical resistance. It is widely used in industries like automotive, aerospace, and medical due to these attributes.
2.Why is Polyamide 11 considered versatile in industrial applications?
PA11’s versatility stems from its unique properties:
- High Mechanical Strength:It can withstand significant stress and strain.
- Chemical Resistance:It remains stable in environments with exposure to harsh chemicals.
- Processing Flexibility:It can be molded and shaped into complex forms and structures through various techniques.
3.How should Polyamide 11 be stored to maintain its quality?
PA11 should be stored in a cool, dry environment away from direct sunlight and moisture. Proper storage prevents degradation and preserves the material’s properties, ensuring it remains suitable for processing.
4.What precautions should be taken when handling PA11?
When handling PA11, avoid physical damage and contamination by:
- Using clean, non-abrasive tools.
- Wearing gloves to prevent scratches and contamination.
- Ensuring the handling area is free from dust and foreign particles.
5.What are the common techniques for processing PA11?
- Injection Molding: Used for creating precise, complex parts. It requires careful control of temperature, pressure, and injection speed, along with a well-designed mold.
- Extrusion: Ideal for producing continuous profiles, sheets, and tubes. It involves forcing the polymer through a die at high pressure, where maintaining optimal temperature and pressure settings is crucial.
- Blow Molding: Best for making hollow parts like bottles. This process involves expanding a heated preform using air pressure in a mold, requiring precise control over temperature and pressure.
6.What are common troubleshooting issues when working with PA11?
- Poor Surface Finish: Often caused by improper processing parameters or mold conditions. It can be improved by adjusting temperature, pressure, and ensuring the mold is clean.
- Warping: Results from uneven cooling or internal stresses. Preventing warping involves uniform cooling and optimizing processing conditions.
- Discoloration: Can occur due to excessive heat or contamination. Address this by controlling the processing temperature and ensuring clean handling practices.
7.How can I improve the quality of PA11 parts?
To enhance the quality of parts made from PA11:
- Store the material under proper conditions to prevent degradation.
- Handle it carefully to avoid contamination and physical damage.
- Maintain precise control over processing parameters during molding or extrusion.
- Regularly inspect and maintain molds and dies to ensure they are clean and well-designed.
8. What applications are ideal for PA11?
Given its robust mechanical and chemical properties, PA11 is suitable for:
- Automotive Components:Such as fuel lines and connectors.
- Aerospace Parts:Including lightweight and durable components.
- Medical Devices:Where chemical resistance and mechanical strength are crucial.
9. How does PA11’s chemical resistance benefit its applications?
PA11’s chemical resistance allows it to perform well in environments where it may be exposed to oils, fuels, and other chemicals. This makes it ideal for automotive and aerospace applications where such exposure is common.
10. What is the key to successful processing of PA11?
The key to successfully processing PA11 lies in:
- Understanding its properties.
- Storing and handling it properly.
- Choosing the right processing technique.
- Maintaining and controlling the processing parameters effectively.
By following these guidelines, you can ensure high-quality outcomes when working with PA11 in various industrial applications.