Introduction of Nylon Density
Nylon, a synthetic polymer, is one of the most versatile materials used across various industries. Its durability, strength, and flexibility make it a go-to choice for numerous applications. However, one aspect that significantly impacts nylon’s performance is its density. Nylon density plays a crucial role in determining how well the material can meet the demands of different projects. In this article, we’ll explore the importance of nylon density, its role in project success, and how to select the right density for your needs.
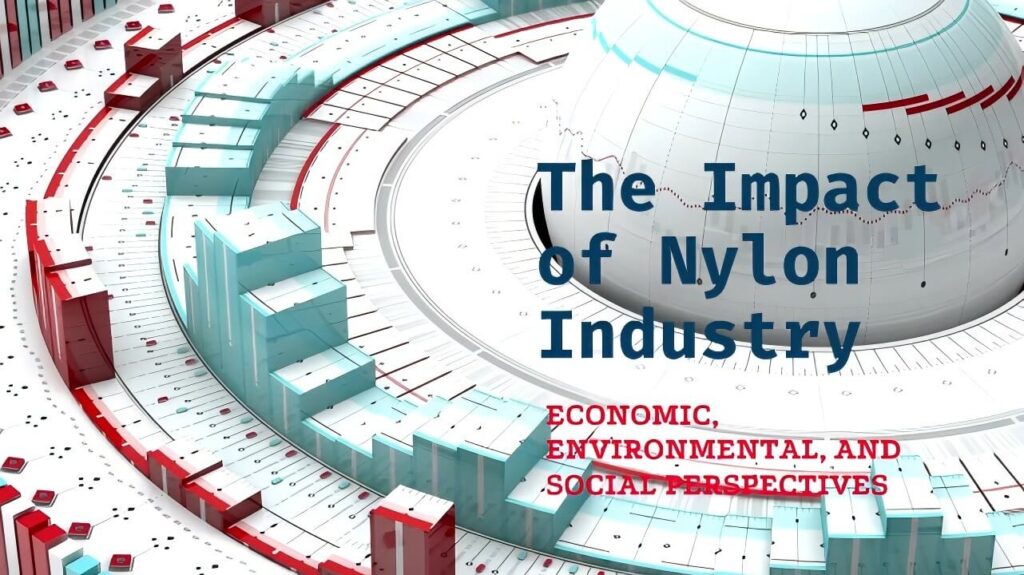
What is Nylon Density?
Definition and Explanation of Nylon Density
Nylon density refers to the mass per unit volume of the material. It is typically measured in grams per cubic centimeter (g/cm³). The density of nylon affects its physical properties, including strength, flexibility, and durability. Higher density means more tightly packed molecules, resulting in a stronger material, while lower density offers more flexibility and lighter weight.
Factors Influencing Nylon Density
Several factors can affect the density of nylon. The type of nylon, the manufacturing process, and any additives or fillers included in the material can all influence its density. For example, the presence of glass fibers in nylon can increase its density, making it more rigid and durable.
Different Types of Nylon and Their Densities
Nylon comes in various forms, each with its own density. The most common types are Nylon 6 and Nylon 6,6. Nylon 6 has a density of approximately 1.13 g/cm³, while Nylon 6,6 is slightly denser, at around 1.14 g/cm³. Other specialty nylons may have different densities, tailored for specific uses.
The Role of Nylon Density in Project Success
How Density Affects Durability
Nylon density directly impacts its durability. High-density nylon is stronger and more resistant to wear and tear, making it ideal for heavy-duty applications like automotive parts or industrial machinery. In contrast, low-density nylon offers greater flexibility but may not withstand the same level of stress over time.
Density’s Impact on Flexibility and Stretch
While high-density nylon is strong, it may lack the flexibility needed for certain projects. Low-density nylon is more stretchable, which can be beneficial for applications like clothing or flexible components in machinery. However, sacrificing density for flexibility can reduce the material’s overall strength.
The Influence of Density on Cost
Another important consideration is cost. High-density nylon typically requires more raw material, making it more expensive than its low-density counterpart. However, the increased durability and strength may justify the higher cost, depending on the project requirements. On the other hand, low-density nylon is more affordable but may need to be replaced more frequently, adding long-term costs.
Selecting the Right Nylon Density for Your Project
Evaluating Project Needs: When to Choose High vs. Low Density
Choosing the right nylon density depends on the specific needs of your project. For applications requiring strength and rigidity, such as automotive or aerospace components, high-density nylon is often the best choice. However, for projects that prioritize flexibility and light weight, like clothing or consumer accessories, low-density nylon may be more suitable.
Case Studies: Successful Applications of Varying Nylon Densities
One example of successful use of high-density nylon is in the automotive industry, where it is used to create durable, long-lasting engine parts. In contrast, low-density nylon has been used effectively in the fashion industry to create lightweight yet sturdy bags and clothing items.
Common Mistakes to Avoid When Choosing Nylon Density
One common mistake is selecting nylon with a density that doesn’t align with the project’s needs. For example, using low-density nylon in a high-stress application may lead to premature wear and tear. Conversely, choosing high-density nylon for a project that requires flexibility can result in a product that is too rigid and uncomfortable to use.
Real-World Applications of Nylon Density
Industrial Uses: Automotive and Aerospace
In the automotive and aerospace industries, nylon density is critical. High-density nylon is used in parts that require durability and resistance to high temperatures, such as engine components or fuel lines. The strength of high-density nylon ensures that these parts can withstand the harsh conditions often encountered in these fields.
Consumer Products: Clothing and Accessories
For consumer products, especially in clothing and accessories, nylon density plays a role in balancing durability and comfort. Low-density nylon is often used in outdoor gear like jackets and backpacks, where lightweight materials are essential but still need to offer protection and longevity.
Specialty Applications: Medical and Safety Gear
In the medical field, nylon density impacts the design of safety equipment, such as gloves and protective clothing. High-density nylon is favored for its strength and ability to provide a barrier against contaminants, while low-density options might be used for disposable or single-use items where flexibility and comfort are more important.
Future Trends in Nylon Density
Advances in Nylon Production Technology
Technological advancements are making it possible to produce nylon with tailored densities for specific applications. New manufacturing processes allow for more precise control over the material’s properties, leading to innovations in both high- and low-density nylons.
Sustainable Practices in Nylon Manufacturing
Sustainability is becoming increasingly important in nylon production. Companies are working on developing nylon with lower environmental impact, including recycling and using renewable resources. These practices are likely to influence the availability of different nylon densities in the future.
Predictions for Nylon Density Innovations
Looking ahead, we can expect to see even more specialized nylon densities designed for niche applications. Innovations in manufacturing techniques and materials science will likely lead to nylons with enhanced properties, such as improved strength-to-weight ratios or greater resistance to extreme conditions.
Conclusion of Nylon Density
Nylon density is a critical factor in determining the success of your project. Whether you need high-density nylon for strength and durability or low-density nylon for flexibility and cost-effectiveness, understanding the role of density will help you make informed decisions. As advancements in technology continue, the future of nylon density looks promising, with more options and sustainable practices on the horizon. Don’t be afraid to experiment with different densities to find the perfect balance for your specific project needs.
Frequently Asked Questions
1.What is the standard density of nylon?
The standard density of nylon varies depending on the type but typically ranges from 1.13 to 1.14 g/cm³ for Nylon 6 and Nylon 6,6.
2.How does nylon density correlate with weight?
Higher-density nylon is heavier due to the tightly packed molecules, while lower-density nylon is lighter and more flexible.
3.Can I combine different nylon densities in one project?
Yes, combining different nylon densities can provide a balance of strength and flexibility, depending on the requirements of the project.
4.What are the advantages of high-density nylon?
High-density nylon offers increased durability, strength, and resistance to wear and tear, making it ideal for heavy-duty applications.
5.How does temperature affect nylon density?
Temperature changes can cause nylon to expand or contract, potentially affecting its density and performance. High temperatures may cause low-density nylon to become more flexible, while cold temperatures may increase its rigidity.