Introductie van Nylon vs PP
Als het gaat om productie en productontwerp, kan het kiezen van het juiste materiaal een aanzienlijk verschil maken in prestaties, kosten en duurzaamheid. Twee van de meest gebruikte materialen in verschillende industrieën zijn nylon en PP. Beide zijn veelzijdig, duurzaam en worden op grote schaal toegepast, maar toch hebben ze verschillende eigenschappen die ze elk meer geschikt maken voor specifieke toepassingen. Inzicht in deze verschillen is essentieel om weloverwogen beslissingen te kunnen nemen op het gebied van engineering, textiel, verpakking en nog veel meer. Deze gids biedt een diepgaande vergelijking van nylon en PP, met aandacht voor hun belangrijkste eigenschappen, toepassingen en de factoren waarmee rekening moet worden gehouden bij het maken van een keuze.
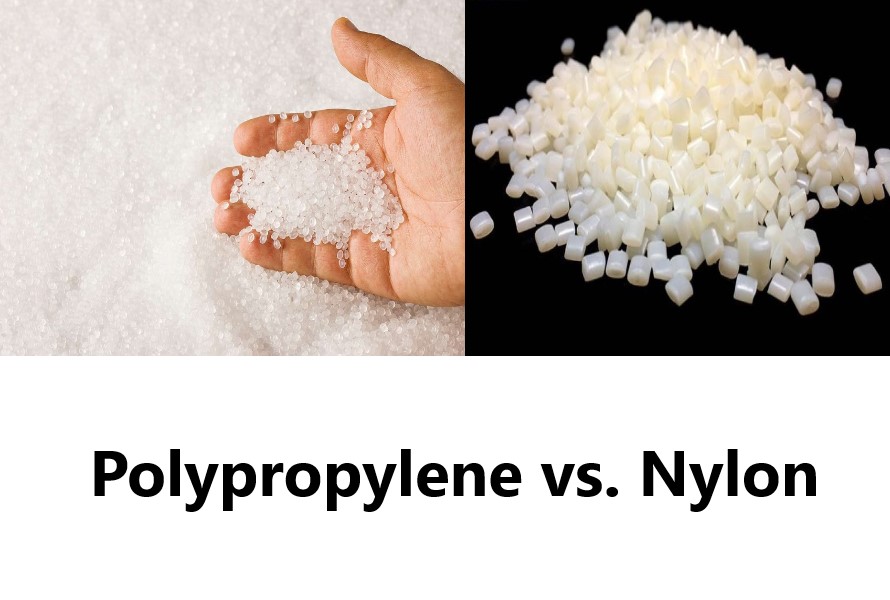
Wat is nylon?
Nylon, voor het eerst ontwikkeld in de jaren 1930, is een synthetisch polymeer dat behoort tot de polyamidefamilie. Het werd op grote schaal gebruikt vanwege de uitstekende balans tussen sterkte, flexibiliteit en slijtvastheid. Er zijn verschillende soorten nylon, met Nylon 6 en Nylon 66 de meest prominente. Nylon 66 heeft bijvoorbeeld een iets hoger smeltpunt en een betere sterkte bij verhoogde temperaturen in vergelijking met Nylon 6, waardoor het geschikter is voor veeleisende toepassingen.
Kenmerken en eigenschappen van nylon:
- Duurzaamheid: Nylon staat bekend om zijn sterkte en slijtvastheid, waardoor het een ideaal materiaal is voor zware toepassingen zoals industriële onderdelen en textiel.
- Flexibiliteit: Ondanks zijn taaiheid behoudt nylon een goede elasticiteit, waardoor het geschikt is voor producten die een zekere mate van flexibiliteit vereisen, zoals kleding of vislijnen.
- Vochtbestendigheid: Nylon absorbeert vocht uit de lucht, wat na verloop van tijd zijn mechanische eigenschappen kan aantasten. Vooruitgang in nylon formuleringen heeft echter de vochtbestendigheid voor verschillende toepassingen verbeterd.
Veelvoorkomend gebruik van nylon in de industrie:
Nylon wordt veel gebruikt in auto-onderdelen, textiel, consumptiegoederen en meer. Zijn combinatie van sterkte en flexibiliteit maakt tot het een aangewezen materiaal in de industrieën die duurzaamheid en prestaties, zoals de productie van toestellen, lagers, kabels, en zelfs medische hulpmiddelen vereisen.
Wat is polypropyleen (PP)?
Polypropyleen, of PP, werd voor het eerst gesynthetiseerd in de jaren 1950 en is sindsdien uitgegroeid tot een van de meest geproduceerde kunststoffen ter wereld. PP is een thermoplastisch polymeer dat bekend staat om zijn lichte gewicht en chemische bestendigheid, waardoor het een populaire keuze is in sectoren variërend van verpakking tot auto-onderdelen.
Eigenschappen en kenmerken van PP:
- Licht gewicht: Een van de belangrijkste voordelen van PP is de lage dichtheid, waardoor het een lichter alternatief is voor andere materialen zoals nylon. Deze eigenschap is vooral gunstig in toepassingen waar gewichtsbesparing van cruciaal belang is, zoals verpakkingen en auto-onderdelen.
- Chemische weerstand: PP is uitstekend bestand tegen een groot aantal chemicaliën, waaronder zuren, basen en oplosmiddelen. Dit maakt het een ideaal materiaal voor gebruik in verpakkingen voor huishoudelijke schoonmaakmiddelen, geneesmiddelen en industriële containers.
- Lage vochtopname: In tegenstelling tot nylon absorbeert PP minimaal vocht, waardoor de mechanische eigenschappen stabiel blijven in vochtige omgevingen.
Toepassingen van PP in verschillende sectoren:
PP wordt vaak gebruikt in de verpakkingsindustrie, vooral voor voedselcontainers, flessen en doppen, vanwege het niet-giftige en lichte gewicht. Het wordt ook vaak gebruikt in huishoudelijke artikelen, auto-onderdelen en textiel zoals tapijten en bekleding.
Nylon vs PP: een directe vergelijking
Bij het vergelijken van nylon en PP is het belangrijk om te kijken naar hun structurele verschillen en hoe die de prestaties in verschillende toepassingen beïnvloeden.
- Structurele verschillen: Nylon is een polyamide, wat betekent dat het amidebindingen bevat, terwijl PP een polyolefine is, bestaande uit koolstof- en waterstofatomen. Dit fundamentele verschil zorgt ervoor dat nylon sterker en flexibeler is dan PP, terwijl PP lichter en chemisch inert is.
- Prestatiefactoren:
- Sterkte: Nylon is sterker dan PP, vooral als het gaat om het weerstaan van trekspanning, waardoor het een betere keuze is voor zware toepassingen zoals mechanische onderdelen.
- Elasticiteit: Nylon heeft ook een grotere elasticiteit, waardoor het kan terugkeren naar zijn oorspronkelijke vorm nadat het is uitgerekt of vervormd. Daarom wordt het gebruikt in textiel en andere toepassingen die flexibiliteit vereisen.
- Veerkracht: PP is weliswaar niet zo sterk als nylon, maar is beter bestand tegen vermoeidheid en behoudt zijn vorm beter bij langdurige belasting, waardoor het ideaal is voor voorwerpen zoals scharnieren of verpakkingen.
- Kostenoverwegingen: Over het algemeen is PP budgetvriendelijker dan nylon, wat het aantrekkelijker kan maken voor grootschalige toepassingen waarbij kostenefficiëntie een prioriteit is.
- Milieu-impact: Noch nylon noch PP is biologisch afbreekbaar, maar beide materialen kunnen worden gerecycled. PP heeft een licht voordeel wat betreft het gemak van recycling vanwege de eenvoudigere chemische structuur, maar beide materialen hebben voortdurende milieu-uitdagingen op het gebied van afvalbeheer.
Eigendom | Polypropyleen | Nylon |
Treksterkte | 25-40 MPa | 50-90 MPa |
Oppervlaktehardheid | 92 HRR (Rockwell R) | 100 - 120 (Rockwell R) |
Bedrijfstemperatuur | <180 °F | -70 tot 250 °F |
Smelttemperatuur | 327 °F | 374 - 460 °F |
Schokbestendigheid | Hoge schokbestendigheid | Hoge slagvastheid (10 keer meer dan ABS) |
Chemische weerstand | Grote chemische weerstand - verdraagt verdunde basen en zuren | Goede chemische weerstand - inclusief weerstand tegen oliën, benzine, brandstoffen, minerale spiritus en sommige alcoholen. |
Waterabsorptie | Bijna waterbestendig. Het absorbeert slechts 0,01% van zijn gewicht in water na een onderdompeling van 24 uur. | 0,30 - 7,0% in gewicht |
Recycleerbaarheid | Ja. Het duurt 20-30 jaar voordat PP biologisch afgebroken is. | Ja. Nylon is niet biologisch afbreekbaar. |
Kiezen tussen nylon en PP
De keuze tussen nylon en PP hangt af van verschillende factoren, waaronder de specifieke vereisten van de toepassing, kostenbeperkingen en milieuoverwegingen.
- Factoren om te overwegen:
- Toepassingseisen: Voor toepassingen die een hoge sterkte en flexibiliteit vereisen, is nylon vaak de beste keuze. Aan de andere kant, voor toepassingen waar lichtgewicht en chemische weerstand van cruciaal belang zijn, is PP de betere optie.
- Kosten vs. prestaties: Als het budget beperkt is, kan PP aantrekkelijker zijn vanwege de lagere kosten. Voor toepassingen die hogere prestaties vereisen, kunnen de extra kosten van nylon echter gerechtvaardigd zijn.
- Casestudies:
- Nylon in industriële onderdelen: In de auto-industrie wordt nylon vaak gebruikt voor onderdelen zoals tandwielen en lagers, waar sterkte en slijtvastheid van cruciaal belang zijn.
- PP in verpakking: PP is een veelgebruikt materiaal voor verpakkingen, vooral in de voedingsmiddelen- en farmaceutische industrie, waar het lichte gewicht en de chemische weerstand van groot belang zijn.
- Aanbevelingen van experts: Experts raden vaak nylon aan voor mechanische toepassingen en PP voor verpakking of chemische opslag vanwege hun respectieve sterke punten.
FAQs over Nylon vs PP
- Is nylon sterker dan PP?
Ja, nylon heeft over het algemeen een hogere treksterkte dan PP, waardoor het beter geschikt is voor zware toepassingen. - Welk materiaal is beter voor buiten?
PP is beter bestand tegen UV-degradatie en vocht, waardoor het een betere optie is voor buitentoepassingen. - Is PP recyclebaar?
Ja, PP wordt op grote schaal gerecycled en wordt meer geaccepteerd in recyclingprogramma's dan nylon. - Kan nylon worden gebruikt in voedselverpakkingen?
Hoewel nylon soms wordt gebruikt voor het verpakken van voedingsmiddelen, met name in vacuüm-gesealde zakken, wordt PP vaker gebruikt vanwege het lichtere gewicht en de lagere kosten.
Conclusie van nylon vs PP
Samengevat zijn nylon en PP twee veelgebruikte materialen die verschillende doelen dienen in verschillende industrieën. Nylon onderscheidt zich door zijn sterkte, flexibiliteit en duurzaamheid, waardoor het ideaal is voor industriële en mechanische toepassingen. Aan de andere kant maken het lichtgewicht, de chemische weerstand en de kosteneffectiviteit van polypropyleen het materiaal bij uitstek voor verpakking en consumptiegoederen. Door de unieke eigenschappen van elk materiaal te begrijpen, kunnen fabrikanten, ingenieurs en ontwerpers weloverwogen beslissingen nemen op basis van de eisen van hun projecten. Uiteindelijk zal de keuze tussen nylon en PP afhangen van factoren zoals toepassingsvereisten, budget en milieuoverwegingen, maar beide materialen zullen een cruciale rol blijven spelen in moderne productie en ontwerp.