Introduction of Nylon 6 vs Nylon 66
Nylon is a popular synthetic polymer, valued for its strength, durability, and versatility. Among the most common types are Nylon 6 and Nylon 66, both widely used across various industries. Although they share many similar traits, the two nylons differ significantly in their chemical structure, leading to variations in their physical properties. One of the most crucial distinctions between them lies in their melting points, which affects their suitability for different applications. In this article, we will explore the differences between Nylon 6 and Nylon 66, focusing on how their melting points impact their use in various industries.
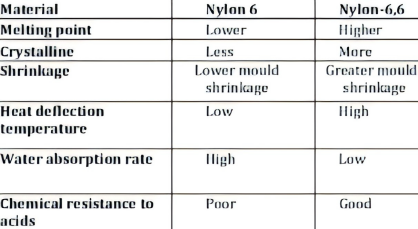
Chemical Structure: Nylon 6 vs Nylon 66
The key to understanding the differences between Nylon 6 and Nylon 66 lies in their chemical structures. Nylon 6 is a homopolymer, meaning it is created from a single type of monomer—caprolactam. Through a process called ring-opening polymerization, caprolactam forms a polymer chain with repeating units of six carbon atoms. This relatively straightforward structure is the foundation of Nylon 6’s unique properties.
In contrast, Nylon 66 is a copolymer, synthesized from two different monomers: adipic acid and hexamethylenediamine. The resulting polymer chain consists of alternating units from each monomer, with both contributing six carbon atoms to the chain. This alternating structure gives Nylon 66 a more complex and rigid framework, which in turn affects its melting point and overall performance in various applications.
Melting Point of Nylon 6: Lower Temperature for Flexibility
One of the main differences between Nylon 6 and Nylon 66 is their melting points. Nylon 6 typically melts at a lower temperature, with a range of 215 to 230 degrees Celsius. This lower melting point is due to its simpler polymer structure, which has weaker intermolecular forces. The result is a material that is easier to melt, making Nylon 6 ideal for applications where flexibility and ease of processing are important.
For example, Nylon 6 is commonly used in the textile industry for fabrics, where its lower melting point allows for efficient processing and manufacturing. Additionally, the material is used in injection molding for producing plastic parts, as it can be melted and reshaped with less energy compared to Nylon 66.
Melting Point of Nylon 66: Higher Temperature for Strength
In contrast, Nylon 66 has a significantly higher melting point, typically falling between 260 and 270 degrees Celsius. The more complex chemical structure of Nylon 66, with its alternating monomers of adipic acid and hexamethylenediamine, leads to stronger intermolecular forces. This tighter, more rigid structure requires more heat to break down, resulting in a higher melting point.
This high melting point makes Nylon 66 ideal for applications requiring greater heat resistance and dimensional stability. For instance, Nylon 66 is commonly used in the automotive and engineering industries, where components must withstand high temperatures and mechanical stress. It is often found in engine parts, electrical connectors, and other high-performance applications where strength and heat resistance are critical.
Application-Based Selection: Flexibility vs Heat Resistance
When choosing between Nylon 6 and Nylon 66, the melting point is a crucial factor to consider, especially when the material will be exposed to heat during its application. Nylon 6, with its lower melting point, is well-suited for applications that prioritize flexibility and ease of processing. Industries such as textiles, consumer goods, and packaging benefit from the material’s adaptability.
On the other hand, Nylon 66 is the preferred choice for more demanding applications where heat resistance and durability are key. The automotive, aerospace, and electrical industries often rely on Nylon 66 for parts that must perform reliably in high-temperature environments. Its higher melting point ensures that these components maintain their structural integrity even under intense conditions.
Pros and Cons of Nylon 6
Nylon 6 offers several advantages, particularly its lower melting point, which makes it easier to process and mold. This characteristic allows for quicker production cycles, which can be beneficial for manufacturers looking to increase efficiency. Additionally, Nylon 6’s lower melting temperature means it requires less energy to melt, resulting in potential cost savings during production.
However, the lower melting point also limits Nylon 6’s use in high-temperature environments. In applications where heat resistance is essential, Nylon 6 may not perform as well as Nylon 66, which can maintain its structural integrity at higher temperatures.
Pros and Cons of Nylon 66
Nylon 66’s higher melting point is one of its standout features, making it ideal for applications requiring high heat resistance. It is also stronger and more rigid than Nylon 6, making it better suited for mechanical components exposed to stress. Its durability and strength give it a longer lifespan in harsh environments, making it the go-to material for demanding industries.
On the downside, Nylon 66 is more difficult to process due to its higher melting point. This often results in longer production times and increased energy costs. Additionally, the rigidity of Nylon 66 can make it less suitable for applications requiring flexibility.
Conclusion of Nylon 6 vs Nylon 66
Understanding the melting point differences between Nylon 6 and Nylon 66 is essential for selecting the right material for specific applications. Nylon 6, with its lower melting point, offers greater flexibility and ease of processing, making it ideal for textiles, injection molding, and consumer goods. Meanwhile, Nylon 66’s higher melting point provides superior heat resistance and strength, making it the better choice for demanding applications in the automotive, aerospace, and engineering industries. By considering the specific needs of an application, manufacturers can make informed decisions about which type of nylon to use, ensuring optimal performance and durability.
Nylon 6 vs Nylon 66: FAQ Summary
1. What is the main difference between Nylon 6 and Nylon 66?
The primary difference is in their chemical structures. Nylon 6 is a homopolymer made from a single monomer (caprolactam), while Nylon 66 is a copolymer formed from two monomers (adipic acid and hexamethylenediamine).
2.How do their melting points differ?
Nylon 6 has a lower melting point, typically between 215-230°C. Nylon 66 has a higher melting point, ranging from 260-270°C.
3.Why does Nylon 6 have a lower melting point?
Nylon 6’s simpler polymer structure leads to weaker intermolecular forces, making it easier to melt at lower temperatures.
Why is Nylon 66’s melting point higher?
Nylon 66’s alternating polymer structure creates stronger intermolecular forces, requiring more heat to break down, hence the higher melting point.
In what applications is Nylon 6 preferred?
Nylon 6 is preferred for applications requiring flexibility and ease of processing, such as textiles, injection molding, and consumer goods manufacturing.
When is Nylon 66 the better choice?
Nylon 66 is better suited for high-temperature and high-strength applications, like automotive parts, engineering components, and electrical connectors.
What are the advantages of Nylon 6?
Nylon 6 is easier to process, has a faster production cycle, and requires less energy to melt, making it cost-effective for certain industries.
What are the advantages of Nylon 66?
Nylon 66 offers superior heat resistance, rigidity, and durability, making it ideal for demanding environments.
What are the disadvantages of Nylon 6?
Nylon 6’s lower melting point limits its use in high-heat applications where it may lose structural integrity.
What are the disadvantages of Nylon 66?
Nylon 66’s higher melting point makes it more challenging and costly to process, and its rigidity may make it less suitable for flexible applications.
How does the melting point impact material selection?
The melting point affects a material’s suitability for different applications. Nylon 6 is chosen for flexible, low-heat uses, while Nylon 66 is selected for high-heat, high-strength environments.