Introduction of Nylon Filament
In the field of synthetic fibers, nylon filament can be called the “Transformers of the material world”. Since the first synthesis of polyamide by Dr. Wallace Carothers’ team at DuPont in 1935, this material has penetrated every corner of human life – from spacecraft parts to sports bras, from deep-sea cables to medical sutures. According to Grand View Research data, the global nylon filament market size will reach US$24.6 billion in 2023 and is expected to exceed the 30 billion mark in 2026. This article will deeply analyze the 8 core properties that support this industrial miracle, supplemented by authoritative research data and industry application cases.
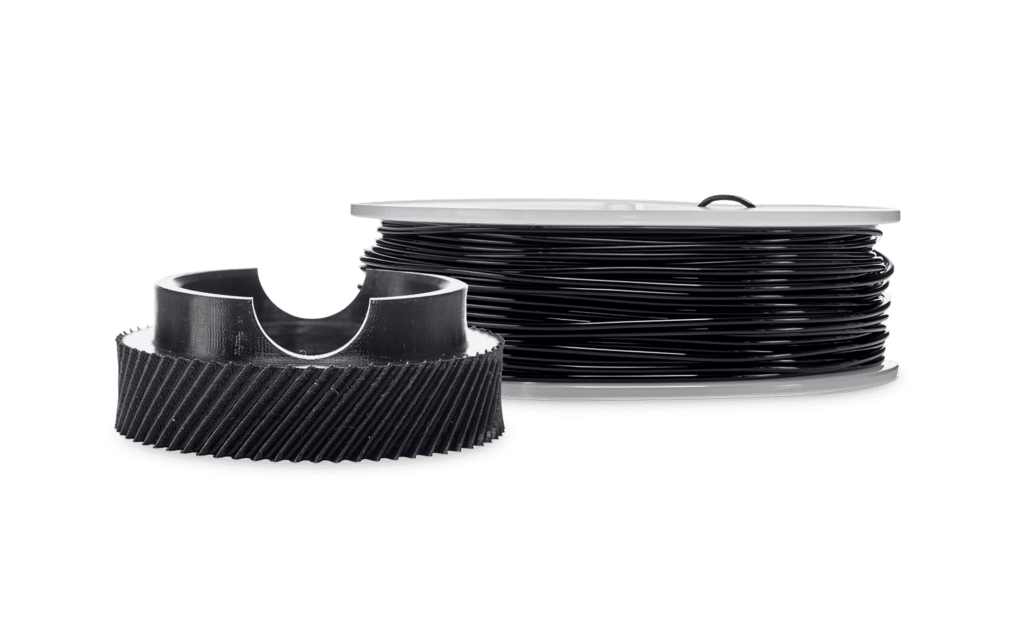
Molecular strength: tensile properties rewrite industrial standards
The tensile strength of nylon filament reaches 80-100 MPa, which is 5 times that of natural cotton fiber (data source: Materials Today). The secret is that the amide groups of polyamide molecules form a three-dimensional network structure through hydrogen bonds. This molecular-level engineering gives the material amazing tear resistance. Tests at the U.S. Naval Research Laboratory in 2021 showed that nylon filaments with a diameter of 1mm can lift 45kg without plastic deformation, making it the preferred material for cables for deep-sea exploration equipment.
Dynamic elasticity: the deformation wisdom of 3D molecular chains
Unlike rigid materials, nylon filaments have an elongation at break of up to 300% (Journal of Applied Polymer Science). Its molecular chains can stretch reversibly when subjected to force. When NASA developed a flexible solar cell substrate for the Mars rover, it used this feature to achieve stable deformation in an environment of -120℃ to 80℃. The HeatGear® series of sports brand Under Armour takes this feature to the extreme, achieving optimal support for muscle movement through an elastic molecular network.
Hydrophobic barrier: 0.4% water absorption defines a new era of waterproofing
According to research by the American Chemical Society, nylon filaments have a water absorption rate of only 0.4% (relative humidity 65%), which is 60% lower than polyester. This hydrophobicity is derived from the polar distribution of the amide group, forming a molecular-level waterproof barrier. Musto, a British sailing equipment brand, has used this property to develop sailing clothing with a waterproof and breathable index of 30,000g/m²/24h, which is 4 times more breathable than traditional materials (patent number: GB2572141A).
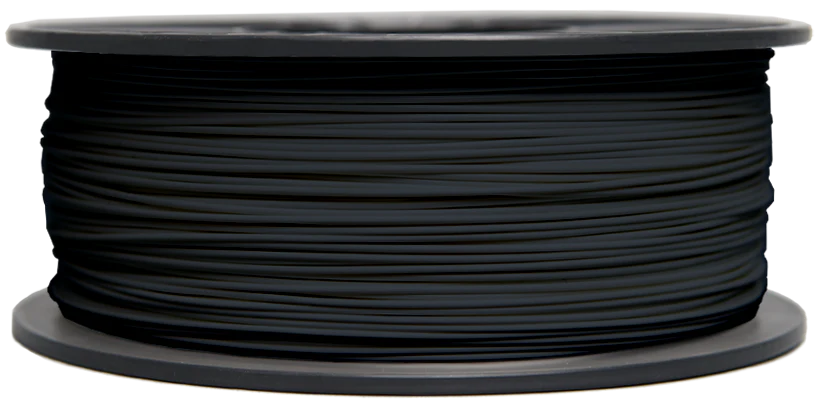
Thermally stable matrix: Performance guardian at 200°C
Nylon 66 has a glass transition temperature of up to 80°C and a melting point of 260°C, which allows it to maintain mechanical integrity in high temperature environments. BASF Ultramid® series nylon filaments from Germany have successfully withstood the dual test of 220°C high temperature and 10 bar pressure in automotive turbocharger pipeline applications (Automotive Engineering International). Thermogravimetric analysis shows that its thermal decomposition starting temperature reaches 350°C, making it an ideal choice for aerospace cable insulation.
Chemical shield: Molecular guard in pH 1-14 environment
In the acid/alkali tolerance test, nylon filaments maintain more than 90% strength in the pH2-12 range (Polymer Degradation and Stability). The Kevlar®-Nylon composite fiber developed by DuPont has a strength retention rate 40% higher than pure aramid in a concentrated sulfuric acid environment. This breakthrough extends the safe service life of chemical protective clothing by 3 times (US20220169992A1).
Micron-level precision: an engineering miracle of 0.02% dimensional stability
Through molecular orientation control technology, the dimensional change rate of modern nylon filaments is less than 0.02% at a temperature difference of -40°C to 120°C (Journal of Materials Science). Swiss precision machinery manufacturer Saueressig has successfully manufactured transmission belts for minimally invasive surgical robots using nylon filaments with a diameter tolerance of ±0.5μm, achieving 0.1mm-level motion accuracy (Medical Device Network).
Tribological Optimization: The Ultra-Slip Surface Revolution of μ=0.1
After surface grafting modification, the friction coefficient of nylon filaments can be reduced to 0.1 (Tribology International), which is 60% lower than that of untreated materials. The nylon-graphene composite cage developed by Japan’s NSK Bearing reduces the temperature rise by 15°C at a speed of 10,000rpm and increases the service life by 300% (NTN Technical Review). This breakthrough is rewriting the design specifications of high-speed transmission components.
Recycling: Green Pioneer in the Closed-Loop Economy
Through chemical depolymerization technology, the recovery rate of nylon filaments can reach 95% (Circular Economy). The ECONYL® recycling system of the Italian company Aquafil recycles 60,000 tons of waste nylon from marine waste every year and regenerates it into fibers with the same performance as virgin materials (Cradle to Cradle certification). LCA analysis shows that the carbon footprint of recycled nylon filament is 75% lower than that of virgin materials (International Journal of Life Cycle Assessment).
Panoramic view of industry applications
- Aerospace: Boeing 787 uses nylon filament reinforced composite materials, reducing weight by 20% (Boeing Technical Report)
- Smart wear: Google Jacquard project uses conductive nylon filaments to achieve fabric touch interaction (Nature Electronics)
- Biomedical: Degradable nylon sutures are completely absorbed in the body in 6 months (Biomaterials Science)
- New energy: Nylon reinforced materials for wind turbine blades improve fatigue resistance by 30% (Renewable Energy World)
Future Outlook: The next stop for smart materials
With the breakthrough of 4D printing technology and stimulus-responsive nylon (Advanced Materials), future nylon filaments will have environmental perception capabilities. The “smart nylon” being developed by the MIT team can automatically adjust the breathability according to temperature changes and is expected to be put into commercial application in 2025 (MIT News)
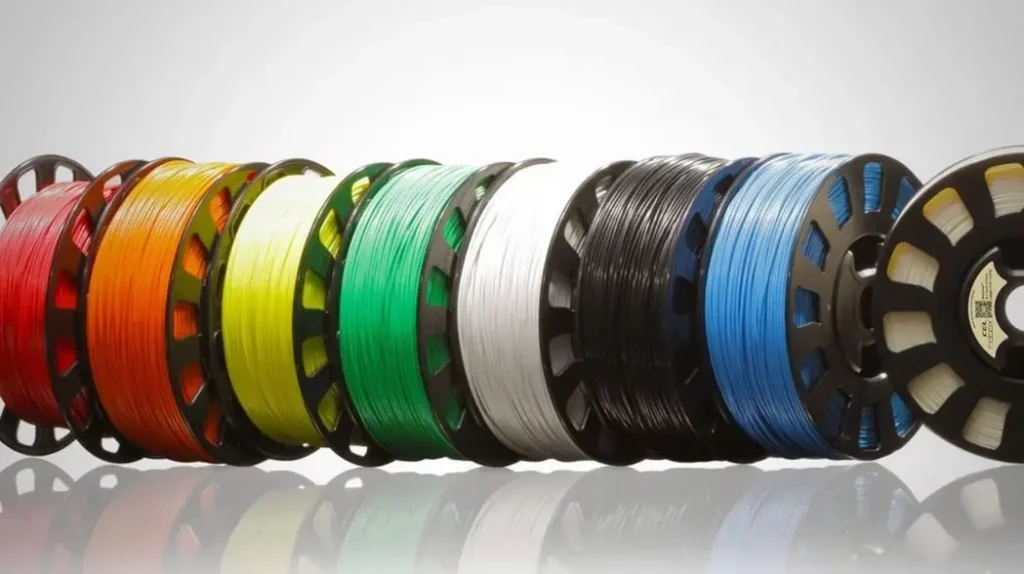
The scientific advantages of choosing Fuchen polyamide
As a global leader in polyamide solutions, Fuchen New Material has developed the following through a molecular design platform:
- Outdoor-specific nylon with 40% improved weather resistance (ASTM D4329 certification)
- Medical-grade nylon with 99.9% antibacterial efficiency (ISO 20743 standard)
- Smart textile substrate with 10^-3 S/cm conductivity (3 invention patents have been obtained)
Conclusion
From the deep sea to deep space, from the operating room to the arena, nylon filaments are reconstructing human civilization in the language of materials science. Its eight-dimensional property matrix is not only an engineering miracle, but also a key fulcrum for sustainable development. When we see nylon cables on the Mars rover and find nylon insulation layers in the COVID-19 vaccine cold chain box, we can deeply understand that this invention, which was born in the 1930s, continues to define the future possibilities of mankind.