Въведение of PA11 and PA12 Plastic
In the world of engineering plastics, polyamides stand out for their versatility and robust performance across various industries. Among the most notable types are PA11 and PA12 plastic, two materials renowned for their unique properties and extensive applications. Both of these polyamides share common characteristics but also exhibit significant differences that influence their suitability for specific uses. This article delves into the nuances that distinguish PA11 from PA12, providing a detailed understanding of their compositions, properties, and potential applications.
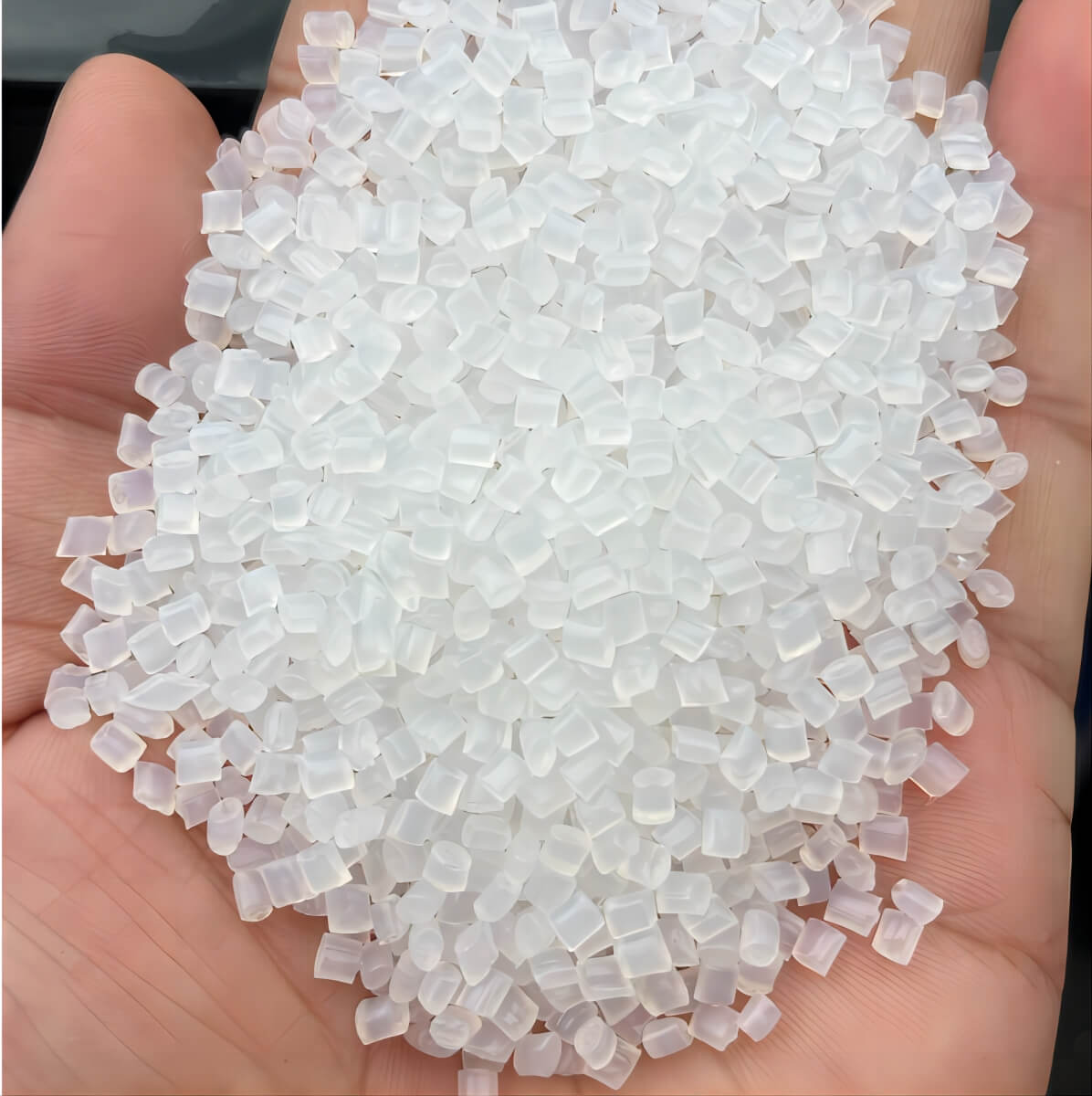
Chemical Composition: The Backbone of Differences in PA11 and PA12 Plastic
PA11 и Пластмаса PA12 are both members of the polyamide family, a group of thermoplastics known for their strength and durability. However, their chemical compositions set them apart significantly. PA11 is synthesized from 11-aminoundecanoic acid, while PA12 originates from 12-aminododecanoic acid. This seemingly minor difference—a single carbon atom in their molecular structure—leads to distinct variations in their physical and mechanical properties.
Mechanical Properties: Flexibility vs. Rigidity of PA11 and PA12 Plastic
The mechanical properties of PA11 and PA12 plastic are influenced by their molecular structures. PA11 is generally more flexible, with a lower glass transition temperature (Tg), making it easier to process and mold into different shapes. This flexibility is advantageous in applications where impact resistance and adaptability are critical. Conversely, PA12 exhibits a higher Tg, offering superior heat resistance and stiffness. This makes PA12 ideal for high-strength applications such as gears and bearings, where dimensional stability is paramount.
Compatibility with Additives: Blending Capabilities in PA11 and PA12 Plastic
Another crucial aspect that differentiates PA11 from PA12 is their compatibility with additives and fillers. PA11 can be readily blended with various materials, including glass fibers, to enhance its mechanical properties and performance. This blending versatility makes PA11 a popular choice for a wide range of applications, from automotive components to sports equipment. On the other hand, PA12’s unique chemical structure poses challenges in blending with other materials. Nonetheless, PA12 can still be combined with other engineering plastics to create tailored solutions for specific needs.
Applications: Tailoring Material Choice to Functional Requirements
Given their distinct properties, PA11 and PA12 plastic find uses in diverse applications. PA11’s flexibility and impact resistance make it suitable for dynamic environments, such as in automotive and medical applications. Its ability to blend with other materials also extends its utility across various industries. PA12, with its superior stiffness and heat resistance, excels in environments requiring high strength and stability. Applications in aerospace, electronics, and precision mechanical components often favor PA12 for these reasons.
Заключение на PA11 and PA12 Plastic
While PA11 and PA12 are both high-performance polyamides, their differences in chemical composition, mechanical properties, and blending capabilities render them suitable for distinct applications. Understanding these differences enables engineers and designers to select the most appropriate material for their specific requirements, ensuring optimized performance and efficiency. Whether the need is for flexibility and impact resistance or stiffness and heat resistance, the choice between PA11 and PA12 can significantly impact the success of a project.
FAQ: Understanding the Differences Between PA11 and PA12 Plastics
1.What are PA11 and PA12 Plastic?
PA11 (Полиамид 11) и PA12 (Полиамид 12) are types of engineering plastics known as polyamides. They are thermoplastics appreciated for their high strength, durability, and resistance to environmental factors, making them suitable for various industrial applications.
2.How do PA11 and PA12 plastic differ in their chemical composition?
PA11 is derived from 11-aminoundecanoic acid, while PA12 is synthesized from 12-aminododecanoic acid. This difference in their molecular structure—specifically, the number of carbon atoms—results in distinct physical and mechanical properties.
3.What are the key mechanical properties of PA11 compared to PA12 plastic?
- PA11: Known for its flexibility, PA11 has a lower glass transition temperature (Tg). This makes it easier to mold and process into various shapes, and it excels in applications requiring high impact resistance.
- PA12: Exhibits greater stiffness and a higher Tg, providing better heat resistance and dimensional stability. It is ideal for applications needing high strength and precision.
4. How do PA11 and PA12 plastic handle blending with additives and fillers?
- PA11: Easily blends with materials like glass fibers, enhancing its mechanical properties. This versatility makes it a popular choice for diverse applications, including automotive and sports equipment.
- PA12: More challenging to blend due to its chemical structure. However, it can be combined with other engineering plastics to develop custom materials for specific applications.
5. In what applications are PA11 and PA12 plastic commonly used?
- PA11: Utilized where flexibility and impact resistance are crucial, such as in automotive components, medical devices, and dynamic environments.
- PA12: Preferred for applications requiring high strength and stability, including aerospace components, electronic parts, and precision mechanical gears.
6. What factors should be considered when choosing between PA11 and PA12 plastic?
When selecting between PA11 and PA12, consider the specific requirements of your application:
- Flexibility vs. Stiffness: PA11 is better for applications needing flexibility and impact resistance, while PA12 is suited for scenarios requiring rigidity and heat resistance.
- Blending Capabilities: PA11’s compatibility with additives makes it versatile for various uses. PA12 is more specialized but can be tailored for specific high-strength applications.
- Environmental Resistance: Both materials offer resistance to environmental factors, but their suitability may vary based on specific conditions and performance needs.