Einführung von PA12GF30
In der sich ständig weiterentwickelnden Welt der Luft- und Raumfahrttechnik spielt die Materialauswahl eine entscheidende Rolle bei der Gewährleistung der Leistung, Sicherheit und Effizienz von Luft- und Raumfahrzeugkomponenten. Ein solches Material, das die Aufmerksamkeit von Ingenieuren und Designern auf sich gezogen hat, ist PA12GF30, ein Hochleistungswerkstoff. Polyamid 12 (PA12), verstärkt mit 30%-Glasfasern. PA12-GF30 ist für seine außergewöhnlichen mechanischen Eigenschaften, seine thermische Stabilität und seine Chemikalien- und Abriebbeständigkeit bekannt und wird zunehmend in der Luft- und Raumfahrtindustrie eingesetzt. Um dieses Material effektiv nutzen zu können, ist jedoch ein tiefes Verständnis seiner einzigartigen Eigenschaften und potenziellen Einschränkungen erforderlich.
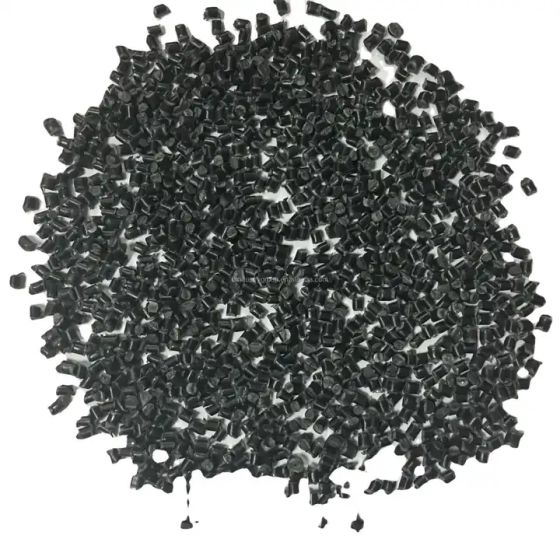
Steifigkeit/Gewicht-Verhältnis von PA12GF30
Eine der wichtigsten Eigenschaften von PA12GF30, die es für die Luft- und Raumfahrttechnik interessant macht, ist sein hohes Verhältnis von Steifigkeit zu Gewicht. Diese Eigenschaft macht es ideal für Anwendungen, bei denen eine Gewichtsreduzierung von größter Bedeutung ist, wie z. B. bei Flugzeugkomponenten und Satellitenteilen. Die beeindruckende Steifigkeit des Materials ermöglicht leichte Konstruktionen, die die strukturelle Integrität nicht beeinträchtigen. Dieser Vorteil ist jedoch mit einer Einschränkung verbunden: PA12-GF30 ist anfällig für Risse und sprödes Versagen, wenn es nicht sorgfältig konstruiert und hergestellt wird. Die hohe Steifigkeit ist zwar vorteilhaft für die Gewichtsreduzierung, kann aber zu Spannungskonzentrationen führen, so dass die Konstrukteure der Geometrie der Teile große Aufmerksamkeit schenken müssen. Durch sorgfältige Konstruktionsverfahren und eine gleichmäßige Verteilung der Spannungen auf die Komponenten können Ingenieure das Risiko von Rissen verringern und die Haltbarkeit von PA12-GF30-Bauteilen erhöhen.
PA12GF30 meistert hohe Temperaturen und Temperaturschocks
Die Hochtemperaturbeständigkeit von PA12-GF30 ist eine weitere Eigenschaft, die seine Eignung für Anwendungen in der Luft- und Raumfahrt unterstreicht, insbesondere in Umgebungen, in denen hohe Temperaturen ein Problem darstellen. Diese thermische Stabilität ermöglicht es dem Material, seine strukturellen Eigenschaften unter Hitzebelastung beizubehalten, was es für Bauteile, die hohen thermischen Belastungen ausgesetzt sind, wertvoll macht. Diese Widerstandsfähigkeit bedeutet jedoch auch, dass PA12-GF30 anfällig für Temperaturschocks ist, d. h. für schnelle Temperaturschwankungen, die im Laufe der Zeit zu einer Verschlechterung des Materials führen können. Um diese Herausforderung zu meistern, müssen die Konstrukteure den Wärmeausdehnungskoeffizienten des Materials berücksichtigen und sicherstellen, dass die Konstruktion und der Herstellungsprozess des Bauteils potenzielle Wärmeschwankungen berücksichtigen. Auf diese Weise können sie das Risiko von Temperaturschocks verringern und die Lebensdauer von PA12-GF30-Komponenten in Hochtemperaturumgebungen verlängern.
Chemische Beständigkeit von PA12GF30
Die ausgezeichnete chemische Beständigkeit von PA12GF30 ist einer seiner wichtigsten Vorteile in der Luft- und Raumfahrttechnik, wo der Kontakt mit aggressiven Chemikalien oft unvermeidlich ist. Diese Eigenschaft macht es zu einer idealen Wahl für Bauteile, die korrosiven Umgebungen oder dem Kontakt mit aggressiven Flüssigkeiten standhalten müssen. Trotz seiner Robustheit ist PA12-GF30 jedoch nicht völlig immun gegen chemischen Abbau. Bestimmte Chemikalien können zu einer Verschlechterung führen, die die Leistung des Materials im Laufe der Zeit beeinträchtigen kann. Konstrukteure müssen die chemischen Bedingungen, denen die Komponenten ausgesetzt sind, genau kennen und PA12-GF30 entsprechend auswählen. Durch die Einbeziehung von Schutzmaßnahmen und die Berücksichtigung der chemischen Kompatibilität während der Konstruktionsphase können Ingenieure die Integrität von PA12-GF30-Bauteilen vor potenziellen chemischen Bedrohungen schützen.
Festigkeit/Gewicht-Verhältnis von PA12GF30
Das hohe Festigkeits-Gewichts-Verhältnis von PA12GF30 macht es besonders attraktiv für Anwendungen in der Luft- und Raumfahrt, bei denen die strukturelle Festigkeit eine wichtige Rolle spielt. Diese Eigenschaft ist besonders vorteilhaft für Bauteile wie Flugzeugfahrwerke und andere Strukturelemente, die hohen mechanischen Belastungen standhalten müssen, ohne übermäßig viel Gewicht zu haben. Die beeindruckende Festigkeit des Materials geht jedoch mit einer Anfälligkeit für Ermüdungsversagen einher, wenn es nicht richtig behandelt wird. Ermüdungsversagen kann durch wiederholte zyklische Belastung auftreten, was im Laufe der Zeit zu einer allmählichen Schwächung des Materials führt. Um dieses Risiko zu minimieren, müssen Konstrukteure die Ermüdungseigenschaften des Materials bereits in der Konstruktions- und Fertigungsphase berücksichtigen. Durch die Umsetzung von Konstruktionsstrategien, die Spannungskonzentrationen minimieren und Lasten gleichmäßig verteilen, können Ingenieure die Ermüdungsbeständigkeit von PA12-GF30-Komponenten verbessern und ihre langfristige Zuverlässigkeit sicherstellen.
Abrieb- und Verschleißfestigkeit: Garantiert Langlebigkeit
PA12GF30 zeichnet sich durch seine hohe Abrieb- und Verschleißfestigkeit aus und ist daher eine ausgezeichnete Wahl für Anwendungen, bei denen Abnutzung und Verschleiß ein Thema sind. Diese Eigenschaft ist besonders wertvoll für Komponenten, die Reibung oder Stößen ausgesetzt sind, wie z. B. bei Flugzeug- und Satellitenteilen. Die Fähigkeit des Materials, mechanischem Verschleiß zu widerstehen, trägt zur Langlebigkeit und Leistungsstabilität von Bauteilen in der Luft- und Raumfahrt bei. Es ist jedoch zu beachten, dass PA12-GF30 im Laufe der Zeit eine Oberflächenverschlechterung erleiden kann, die seine Leistung beeinträchtigen kann. Konstrukteure müssen sich darauf konzentrieren, die Oberflächenbeschaffenheit zu optimieren und potenzielle Verschleißstellen zu beseitigen, um die Integrität des Materials zu erhalten. Durch die Berücksichtigung dieser Faktoren in der Konstruktions- und Produktionsphase können Ingenieure die Lebensdauer von PA12-GF30-Bauteilen verlängern und sicherstellen, dass sie den strengen Anforderungen von Luft- und Raumfahrtanwendungen gerecht werden.
Schlussfolgerung: Nutzung des Potenzials von PA12GF30
Zusammenfassend lässt sich sagen, dass PA12GF30 ein Hochleistungswerkstoff ist, der eine einzigartige Kombination mechanischer, thermischer und chemischer Eigenschaften bietet, die ihn zu einer attraktiven Wahl für verschiedene Anwendungen in der Luft- und Raumfahrt machen. Seine hohe Steifigkeit im Verhältnis zum Gewicht, seine thermische Stabilität, seine chemische Beständigkeit, seine Festigkeit im Verhältnis zum Gewicht und seine Beständigkeit gegen Abrieb und Verschleiß machen es zu einem vielseitigen Material mit großem Potenzial. Um diese Vorteile in vollem Umfang nutzen zu können, müssen die Konstrukteure jedoch die Herausforderungen meistern, die mit seinen einzigartigen Eigenschaften verbunden sind. Durch die Anwendung sorgfältiger Konstruktionsverfahren und die Berücksichtigung potenzieller Einschränkungen können Ingenieure PA12-GF30 nutzen, um Bauteile für die Luft- und Raumfahrt zu entwickeln, die nicht nur die Industriestandards erfüllen, sondern auch die Leistungserwartungen übertreffen. Bei sorgfältiger Beachtung von Details und einem Engagement für Innovation kann PA12-GF30 eine entscheidende Rolle bei der Weiterentwicklung der Luft- und Raumfahrttechnik spielen und die Grenzen des Möglichen in der Luft und darüber hinaus erweitern.
FAQ: Konstruktionsüberlegungen für PA12GF30 in der Luft- und Raumfahrttechnik
1. was ist PA12GF30?
PA12-GF30 ist ein Hochleistungsmaterial aus Polyamid 12 (PA12), das mit 30%-Glasfasern verstärkt ist. Es ist bekannt für seine außergewöhnlichen mechanischen Eigenschaften, seine thermische Stabilität und seine Beständigkeit gegen Chemikalien und Abrieb, was es zu einer beliebten Wahl für Anwendungen in der Luft- und Raumfahrt macht, z. B. für Flugzeugteile, Satellitenteile und Raumfahrzeugkomponenten.
2. warum wird PA12GF30 in der Luft- und Raumfahrttechnik verwendet?
PA12-GF30 wird aufgrund seiner Eigenschaften in der Luft- und Raumfahrttechnik verwendet:
- Hohes Verhältnis von Steifigkeit zu Gewicht:Ermöglicht leichte Konstruktionen ohne Beeinträchtigung der Festigkeit, ideal für Anwendungen, bei denen eine Gewichtsreduzierung entscheidend ist.
- Hohe Temperaturbeständigkeit:Geeignet für Umgebungen mit hohen Temperaturen, wobei die Stabilität unter thermischer Belastung erhalten bleibt.
- Ausgezeichnete chemische Beständigkeit:Schützt vor aggressiven Chemikalien und korrosiven Umgebungen.
- Hohes Verhältnis von Festigkeit zu Gewicht:Bietet eine hohe strukturelle Integrität bei geringem Gewicht.
- Abrieb- und Verschleißfestigkeit:Gewährleistet die Haltbarkeit von Komponenten, die Reibung und Stößen ausgesetzt sind.
Was ist bei der Verwendung von PA12GF30 zu beachten?
Bei der Konstruktion mit PA12-GF30 müssen mehrere wichtige Aspekte berücksichtigt werden:
Verhältnis von Steifigkeit zu Gewicht:
- Vorteile:Ermöglicht leichte und stabile Komponenten.
- Die Risiken:Anfällig für Rissbildung und sprödes Versagen aufgrund von Spannungskonzentrationen.
- Lösungen:Sorgfältige Konstruktion, um die Belastung gleichmäßig zu verteilen und das Risiko von Rissen zu minimieren.
Thermische Stabilität:
- Vorteile:Kann hohen Temperaturen standhalten und ist daher ideal für heiße Umgebungen.
- Die Risiken:Anfällig für Wärmeschocks, was im Laufe der Zeit zu einer Verschlechterung führt.
- Lösungen:Berücksichtigen Sie den Wärmeausdehnungskoeffizienten und planen Sie für thermische Schwankungen.
Chemische Beständigkeit:
- Vorteile:Beständig gegen viele aggressive Chemikalien, ideal für korrosive Umgebungen.
- Die Risiken:Empfindlich gegenüber bestimmten Chemikalien, die zu einer Verschlechterung führen können.
- Lösungen:Stellen Sie die chemische Verträglichkeit sicher und beziehen Sie Schutzmaßnahmen in die Konstruktion ein.
Verhältnis Stärke/Gewicht:
- Vorteile:Aufgrund seiner hohen Festigkeit eignet es sich für Strukturbauteile wie Fahrwerke.
- Die Risiken:Anfällig für Ermüdungsbruch durch zyklische Belastung.
- Lösungen:Konstruktion zur Minimierung von Spannungskonzentrationen und zur gleichmäßigen Verteilung der Lasten.
Abrieb- und Abnutzungsbeständigkeit:
- Vorteile:Die hohe Verschleißfestigkeit verlängert die Lebensdauer der Komponenten.
- Die Risiken:Mögliche Verschlechterung der Oberfläche im Laufe der Zeit.
- Lösungen:Optimieren Sie die Oberflächenbeschaffenheit und berücksichtigen Sie potenzielle Verschleißstellen bei der Konstruktion.
4 Wie kann das Risiko der Rissbildung in PA12GF30-Bauteilen minimiert werden?
Um das Risiko der Rissbildung in PA12-GF30-Bauteilen zu minimieren, sollten die Konstrukteure darauf achten:
- Sicherstellung, dass die Geometrie der Teile die Spannung gleichmäßig über das Bauteil verteilt.
- Vermeidung von scharfen Ecken oder plötzlichen Dickenänderungen, die zu Spannungskonzentrationen führen könnten.
- Sorgfältige Auswahl von Herstellungsverfahren, die die Wahrscheinlichkeit der Entstehung von Fehlern verringern.
5. Was ist bei den thermischen Eigenschaften von PA12GF30 zu beachten?
Die Konstrukteure müssen die folgenden thermischen Eigenschaften berücksichtigen:
- Die hohe Temperaturbeständigkeit von PA12-GF30 macht es geeignet für Umgebungen mit thermischer Belastung.
- Das Material reagiert empfindlich auf Temperaturschocks, so dass die Konstruktion mögliche schnelle Temperaturschwankungen berücksichtigen muss.
- Die Kenntnis und Planung des thermischen Ausdehnungskoeffizienten des Materials ist von entscheidender Bedeutung, um eine Verschlechterung zu verhindern.
6. wie verhält sich PA12GF30 in chemischen Umgebungen?
PA12-GF30 weist eine ausgezeichnete chemische Beständigkeit auf und eignet sich daher ideal für Bauteile, die aggressiven Chemikalien ausgesetzt sind. Konstrukteure sollten jedoch sicherstellen:
- Umfassende Analyse der spezifischen Chemikalien, denen das Material ausgesetzt sein wird.
- Einführung von Schutzmaßnahmen zur Verhinderung des chemischen Abbaus im Laufe der Zeit.
7. Was ist bei den Festigkeitseigenschaften von PA12GF30 zu beachten?
Das hohe Festigkeits-Gewichts-Verhältnis von PA12-GF30 ist zwar vorteilhaft, birgt aber das Risiko von Ermüdungsbrüchen. Um dieses Problem zu lösen:
- Konstruieren Sie die Komponenten so, dass sich wiederholende Belastungskonzentrationen minimiert werden.
- Verteilen Sie mechanische Belastungen gleichmäßig, um die Ermüdungsfestigkeit zu erhöhen.
8. Wie widersteht PA12GF30 dem Verschleiß und der Abnutzung?
PA12-GF30 ist sehr abrieb- und verschleißfest und eignet sich daher für Teile, die Reibung und Stößen ausgesetzt sind. Um Langlebigkeit zu gewährleisten:
- Konzentrieren Sie sich auf die Optimierung der Oberflächenbeschaffenheit.
- Berücksichtigung potenzieller Abnutzungsstellen in der Konstruktion und im Fertigungsprozess.
9. Was sind die allgemeinen Vorteile und Herausforderungen beim Einsatz von PA12GF30 in der Luft- und Raumfahrttechnik?
PA12-GF30 bietet eine einzigartige Mischung aus mechanischen, thermischen und chemischen Eigenschaften, die es für verschiedene Anwendungen in der Luft- und Raumfahrt besonders geeignet machen. Zu seinen Vorteilen gehören leichte Festigkeit, thermische Stabilität, chemische Beständigkeit und Langlebigkeit. Zu den Herausforderungen gehören jedoch das Risiko von Rissbildung, Temperaturschocks, chemischer Empfindlichkeit, Ermüdungsversagen und Oberflächenverschlechterung. Durch die sorgfältige Berücksichtigung dieser Faktoren bei der Konstruktion und Fertigung können Ingenieure die Vorteile von PA12-GF30 maximieren und gleichzeitig mögliche Nachteile minimieren, um eine hohe Leistung und Zuverlässigkeit in Luft- und Raumfahrtanwendungen zu gewährleisten.