PA612 vs PA12: Decoding the golden rules of nylon material selection to help reduce engineering costs and increase efficiency
Minor differences in molecular structure determine their success or failure in scenarios such as high-temperature fuel pipes, precision gears and medical catheters.
In the world of polymer materials, the polyamide (nylon) family has become the mainstay of engineering applications due to its excellent mechanical properties and chemical stability. Among them, PA612 and PA12, as representatives of long-chain nylon, are often placed at the crossroads of technical choices.
Although both belong to the nailon 12 series, there are profound differences in molecular design, performance boundaries and application scenarios. With the upgrade of the National VI emission standards for automobiles and the surge in demand for precision and sustainable manufacturing of medical devices, accurately mastering the differences between the two materials has become the key to avoiding design failures and optimizing costs.
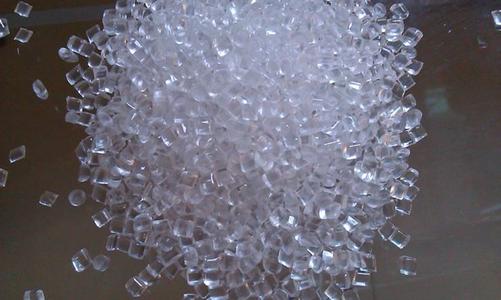
Differences in molecular structure and basic performance
PA612 is formed by polycondensation of hexamethylenediamine (6 carbon atoms) and dodecanedioic acid (12 carbon atoms), with a molecular formula of -(NH-(CH₂)₆-NH-CO-(CH₂)₁₀-CO)-. PA12 is generated by ring-opening polymerization of a single monomer, laurolactam, with a structure of -(NH-(CH₂)₁₁-CO)- .
The difference in carbon chain length directly leads to performance differences: PA612 has a more regular molecular chain arrangement, with a crystallinity of 55%-60%, while PA12 is only 40%-45%. Higher crystallinity gives PA612 better heat resistance (heat deformation temperature is about 20°C higher than PA12) and dimensional stability, while PA12 has more outstanding flexibility and low-temperature impact strength.
Mechanical properties: the game between strength and toughness
PA612’s molecular chain rigidity gives it higher mechanical strength. Typical data show that its tensile strength (60-75 MPa) is significantly higher than PA12 (45-55 MPa), and its flexural modulus (about 2500 MPa) is 1.7 times that of PA12 (about 1500 MPa).
This makes PA612 irreplaceable in gears, bearing cages and other structural parts that need to withstand high loads**. In contrast, PA12 has a higher elongation at break (>30%) and excellent impact strength, especially in a low temperature environment of -40℃, and still maintains toughness, making it the first choice for dynamic bending scenes such as oil pipes and ski boot fasteners.
Water absorption and dimensional stability: The difference in humidity
Although the equilibrium water absorption rate of PA12 (0.5%) is lower than that of PA612 (1.1%-2.5%), the dimensional stability of PA612 is better in a high temperature and humid environment**.
Under 80℃ water immersion environment, the water absorption rate of PA12 can soar to 8%, while that of PA612 is only 6%. After absorbing water, the volume expansion rate of PA12 is 30% higher than that of PA612, resulting in an increased risk of dimensional deviation of precision parts. In the multi-layer design of automotive fuel pipes, PA612 is often used as the inner layer material because its dimensional change rate is lower in the fuel penetration environment, ensuring the reliability of sealing.
Chemical resistance and heat resistance: a severe test of medium and temperature
PA612 wins in the field of oil resistance. Experiments show that after immersion in 120℃ gear oil for 1000 hours, PA612 tensile strength retention rate is greater than 85%, while PA12 drops to 70%. Therefore, PA612 has become the first choice for turbocharged engine fuel pipes, with a temperature tolerance of up to 140℃ (peak 150℃), far exceeding the 120℃ upper limit of PA12.
PA12’s tolerance to strong acid (such as 30% sulfuric acid) is twice that of PA612, and it has more advantages in biocompatibility, which is suitable for medical scenarios such as infusion tubes and surgical instrument handles.
Processing performance and cost-effectiveness: the balance of manufacturing economy
PA12 has a wider processing window: the melting temperature is only 215-235℃, and the mold temperature is 40-60℃ for molding; while PA612 requires a high temperature of 245-265℃ and a mold temperature of 80-100℃. PA12 has better melt fluidity, and the flow length of thin-walled parts is 15% longer than that of PA612, which is suitable for fast mold filling of complex structural parts.
In terms of cost: PA12 resin price is about 20% lower than PA612, but its processing energy consumption is saved by 15%. Comprehensive calculations show that: When the wall thickness is greater than 3mm, the total cost of PA612 is lower (due to the small amount of material used per piece); it is more economical to choose PA12 for thin-walled parts. In addition, bio-based versions of PA12 (such as Emmans GreenLine) can reduce carbon emissions and meet the needs of sustainable development.
Application scenario selection strategy: precise mapping from demand to material
PA612’s rigidity and heat resistance make it dominate the high-performance field:
- Automobile: throttle body, gearbox sensor bracket (high temperature dimensional stability)
- Industry: gears, bearings (high load requirements)
- Packaging: EVOH barrier layer composite tube (low permeability)
PA12’s flexibility and biocompatibility occupy flexible scenarios:
- Medical: catheters, respiratory masks (biosafety)
- Automobile: brake hoses, pneumatic pipelines (dynamic bending)
- Sports: ski boots, diving equipment (resistant to low temperature impact)
Multi-layer composite design can have the advantages of both. For example, Huitong Co., Ltd.’s five-layer fuel pipe solution: PA1012 outer layer (wear-resistant) + EVOH barrier layer + PA612 conductive inner layer (antistatic, oil-resistant), achieving the unity of high barrier and low precipitation.
The essence of the competition between PA612 and PA12 is the dialectical choice between rigidity and flexibility, heat and cold, static and dynamic. In the fuel pipe battlefield, PA612 crushes the 120℃ limit of PA12 with its 140℃ temperature resistance; on the operating table, the biocompatibility of PA12 is irreplaceable by PA612.
The wisdom of today’s engineers lies in finding the invisible dividing line from the molecular chain length (Emans modification scheme) to the water absorption curve (Enxinger physical property table), from the oil resistance test data (Huitong fuel pipe research) to the whole life cycle cost – it divides not only the material, but also the fate of the product’s success or failure.
KKK
Q1: Which has lower water absorption: PA612 or PA12?
A: PA12 absorbs less at room temp (1.8-2.2% vs 2.5-3% for PA612), but PA612 outperforms in humid heat (6% vs 8% at 80°C).
Q2: Is PA612 stronger than PA12?
A: Yes. PA612 tensile strength = 60-75 MPa vs PA12’s 45-55 MPa. Ideal for gears/bearings.
Q3: Which is better for fuel lines: PA612 or PA12?
A: PA612. Retains >85% strength after 1000h in 120°C oil vs PA12’s 70%. Withstands 140°C peaks.
Q4: Does PA12 have any cost advantages?
A: Yes. Resin costs 20% less + 15% lower processing energy. Best for thin-wall parts (<3mm).
Q5: Why choose PA12 for medical devices?
A: Superior biocompatibility (ISO 10993 certified) and acid resistance. Used in catheters/surgical tools.
Q6: Can both materials be modified?
A: PA12 blends better with elastomers (flexible parts). PA612 bonds with 30% glass fiber (strength ↑160MPa).