Sisällysluettelo
ToggleJohdanto
Teknisten muovien osalta kaksi yleisimmin käytettyä materiaalia ovat Nylon (polyamidi) ja POM (polyoksimetyleeni), jotka molemmat tarjoavat ainutlaatuisia ominaisuuksia, jotka tekevät niistä välttämättömiä monissa eri sovelluksissa. Vaikka Nylon ja POM ovat samankaltaisia lujuutensa, kestävyytensä ja monipuolisuutensa suhteen, niiden kemiallisen koostumuksen, mekaanisen suorituskyvyn ja ympäristövaikutusten erot tekevät kummastakin materiaalista paremmin soveltuvan tiettyihin tarkoituksiin. Tässä artikkelissa tarkastelemme Nailonin ja POM:n keskeisiä eroja ja tarjoamme tietoa niiden koostumuksesta, ominaisuuksista, sovelluksista ja kustannustehokkuudesta. Näiden erojen ymmärtäminen on ratkaisevan tärkeää, jotta voit tehdä tietoon perustuvia päätöksiä materiaalin valinnassa, suunnittelitpa sitten osia auto-, ilmailu-, avaruus-, lääke- tai kulutustavarateollisuuteen.
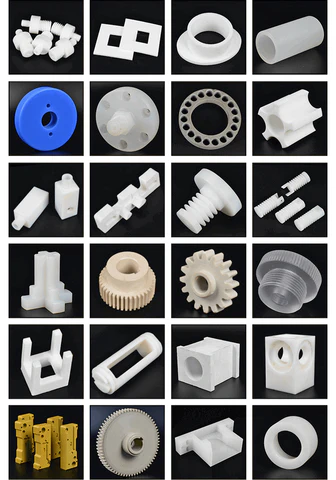
1. Johdanto Nyloniin ja POM:iin
Yleiskatsaus nailoniin: Nylon: koostumus ja ominaisuudet
Nylonon monipuolinen synteettinen polymeeri, joka otettiin ensimmäisen kerran käyttöön 1930-luvulla, ja siitä on sittemmin tullut yksi yleisimmin käytetyistä teknisistä muoveista. Se koostuu pääasiassa amidiryhmien toistuvista yksiköistä, ja se tunnetaan lujuudestaan, joustavuudestaan ja kulutuskestävyydestään. Nailonin ainutlaatuiset ominaisuudet tekevät siitä ihanteellisen materiaalin moniin eri sovelluksiin, kuten tekstiileihin, autonosiin ja mekaanisiin osiin.
Johdanto POM:iin: ominaisuudet ja käyttö
Polyoksimetyleeni, joka tunnetaan yleisesti nimellä POM tai asetaali, on toinen suorituskykyinen tekninen muovi. Tälle materiaalille on ominaista suuri jäykkyys, alhainen kitka ja erinomainen mittatarkkuus. POM-muovia käytetään yleisesti tarkkuutta vaativissa sovelluksissa, kuten hammaspyörissä, laakereissa ja muissa mekaanisissa komponenteissa. Sen alhainen kosteuden imeytymisaste tekee siitä erityisen käyttökelpoisen ympäristöissä, joissa mittatarkkuus on ratkaisevan tärkeää.
Erojen ymmärtämisen tärkeys
Vaikka molemmat materiaalit ovat erittäin toimivia, niiden kemiallinen koostumus, mekaaniset ominaisuudet ja ympäristövaikutukset eroavat toisistaan, joten ne soveltuvat paremmin tiettyihin käyttötarkoituksiin. Näiden erojen ymmärtämisen ansiosta valmistajat ja insinöörit voivat valita oikean materiaalin tehtäväänsä ja optimoida suorituskyvyn, kustannukset ja kestävyyden.
2. Kemiallinen koostumus ja rakenne
Nylon: Molekyylirakenne: Lähempi tarkastelu
Nailon on polyamidi, mikä tarkoittaa, että sen runko koostuu monomeerejä yhdistävistä amidiryhmistä (-CONH-). Nailonin yleisimmät muodot ovat Nylon 6 ja Nylon 66, jotka eroavat toisistaan monomeerien hiiliatomien lukumäärän perusteella. Nailonin molekyylirakenne antaa sille joustavuuden, hyvän kulutuskestävyyden ja kemikaalien kestävyyden, mutta se on myös erittäin herkkä kosteudelle, joka voi vaikuttaa sen ominaisuuksiin.
POM: sen kemiallisen koostumuksen ainutlaatuiset ominaisuudet
POM puolestaan on puolikiteinen kestomuovi, joka koostuu toistuvista formaldehydiyksiköistä. POM:n erittäin kiteinen rakenne vaikuttaa osaltaan sen ylivoimaiseen mekaaniseen lujuuteen ja jäykkyyteen sekä alhaisiin kitkaominaisuuksiin. Toisin kuin nailon, POM imee vähemmän kosteutta, mikä tekee siitä vakaamman erilaisissa ympäristöolosuhteissa.
Nailonin ja POM:n kemiallisten ominaisuuksien vertailu
Molemmilla materiaaleilla on erinomaiset mekaaniset ominaisuudet, mutta niiden kemialliset koostumukset aiheuttavat erilaista käyttäytymistä tietyissä sovelluksissa. Nailonin taipumus veteen voi aiheuttaa sen turpoamisen tai lujuuden heikkenemisen, kun se altistuu kosteudelle, kun taas POM pysyy vakaana ja säilyttää mekaanisen eheytensä. Erittäin kosteissa ympäristöissä tai sovelluksissa, joissa kosteudelle altistuminen on väistämätöntä, POM on usein parempi valinta.
3. Nailonin ja POM:n mekaaniset ominaisuudet
Lujuus ja kestävyys: Nylon vs. POM
Sekä Nylon että POM ovat tunnettuja vaikuttavasta lujuus-painosuhteestaan, mutta ne toimivat eri tavoin tietyissä olosuhteissa. Nylonilla on yleensä suurempi vetolujuus ja parempi iskunkestävyys kuin POM:lla, joten se soveltuu joustavuutta ja sitkeyttä vaativiin sovelluksiin. POM on kuitenkin erityisen jäykkä ja jäykkä, mikä on ratkaisevan tärkeää tarkkuusosissa.
Iskunkestävyys: Mikä materiaali on parempi?
Nailonilla on taipumus vaimentaa enemmän energiaa iskujen aikana, joten se on parempi valinta sovelluksiin, jotka vaativat joustavuutta. Vaikka POM ei ole yhtä iskunkestävä kuin nailon, se kestää paremmin kulutusta ja säilyttää muotonsa myös pitkäaikaisen rasituksen jälkeen.
Vetolujuuden ja leikkauslujuuden vertailu
Vetolujuus ja leikkauslujuus ovat kriittisiä tekijöitä, kun valitaan materiaaleja suurikuormitussovelluksiin. Nailonin vetolujuus ylittää tyypillisesti POM:n vetolujuuden, joten se on ihanteellinen jännitetyille komponenteille. Vaikka POM on vahvaa, se on yleensä leikkauslujuudessa Nylonia parempi, erityisesti sovelluksissa, joissa vaaditaan tarkkaa liikettä tai vähän kitkaa aiheuttavia pintoja.
4. Lämpöominaisuudet
Lämmönkestävyys: Miten Nylon ja POM käsittelevät kohonneita lämpötiloja?
Nailon kestää kohtalaista kuumuutta, ja sen sulamispiste vaihtelee tyypistä riippuen 220 °C:n ja 265 °C:n välillä. Se alkaa kuitenkin hajota yli 150 °C:n lämpötiloissa, erityisesti kosteuden vaikutuksesta. POM:n sulamispiste on korkeampi, noin 175 °C, mutta se kestää paremmin lämpöhajoamista jatkuvassa lämpöaltistuksessa.
Lämpölaajeneminen: Nailonin ja POM:n väliset erot
Molemmat materiaalit lämpölaajenevat lämmitettäessä, mutta POM-materiaalissa tapahtuu vähemmän mittamuutoksia kuin nailonissa. Tämä ominaisuus on erityisen hyödyllinen sovelluksissa, joissa tarkat toleranssit on säilytettävä vaihtelevissa lämpötiloissa.
Sovellukset, jotka hyötyvät lämmönkestävyydestä
Teollisuudenalat, kuten autoteollisuus, elektroniikka ja ilmailu- ja avaruusteollisuus, vaativat materiaaleja, joilla on erinomaiset lämpöominaisuudet. POM:n parempi lämmönkestävyys tekee siitä sopivan korkeille käyttölämpötiloille altistuviin osiin, kuten hammaspyöriin, laakereihin ja tarkkuuskoneistettuihin komponentteihin, kun taas nailonin joustavuus ja parempi iskunkestävyys soveltuvat paremmin sovelluksiin, joissa tarvitaan lämpötilan vaihtelua.
5. Kemiallinen kestävyys
Nailonin suorituskyky syövyttävissä ympäristöissä
Nailon kestää yleisesti ottaen monia kemikaaleja, mutta se voi hajota, kun se altistuu vahvoille hapoille ja emäksille. Sen kestävyys heikkenee entisestään, kun se altistuu liuottimille, kuten bensiinille tai tietyille öljyille, jotka voivat vaikuttaa sen mekaanisiin ominaisuuksiin.
POM: Kemiallisen kestävyyden mestari
POM erottuu edukseen kestävyydessään monenlaisia kemikaaleja, kuten happoja, emäksiä ja liuottimia, vastaan. Sen vähäinen kosteuden imeytyminen ja korkea kemiallinen stabiilisuus tekevät siitä materiaalin, joka on ensisijainen valinta komponentteihin, jotka altistuvat koville kemikaaleille, öljyille ja polttoaineille autoteollisuudessa, teollisuudessa ja kemian prosessisovelluksissa.
Liuotinten, öljyjen ja muiden kemikaalien kestävyyden vertailu
Ympäristöissä, joissa polttoaineille, öljyille tai vahvoille liuottimille altistuminen on ongelma, POM on Nylonia parempi. POM:n vakaus näissä olosuhteissa auttaa säilyttämään mittatarkkuuden ja mekaanisen suorituskyvyn ajan myötä.
6. Nailonin ja POM:n sovellukset
Nailonin yleiset käyttötarkoitukset eri teollisuudenaloilla
Nailonin ainutlaatuinen yhdistelmä lujuutta, joustavuutta ja kulutuskestävyyttä tekee siitä ihanteellisen monenlaisiin sovelluksiin. Sitä käytetään yleisesti tekstiileissä, autonosissa, sähkökomponenteissa ja kulutustavaroissa. Nailonia käytetään myös mielellään hammaspyörien, laakereiden ja holkkien valmistuksessa, jossa iskunkestävyys on ratkaisevan tärkeää.
POM Sovellukset: POM: Tarkkuusosien yleismateriaali
POM-muovin erinomaisen mittatarkkuuden, alhaisen kitkan ja kemiallisen kestävyyden ansiosta se sopii erinomaisesti erittäin tarkkoihin mekaanisiin osiin, kuten hammaspyöriin, laakereihin, lukkoihin ja venttiileihin. Sitä käytetään yleisesti myös auto- ja elektroniikkateollisuudessa komponentteihin, jotka vaativat suurta kulutuskestävyyttä.
Tapaustutkimukset, joissa korostetaan kunkin materiaalin parhaiten soveltuvia sovelluksia
Nylonia käytetään usein esimerkiksi autojen polttoaineletkuissa ja ilmanottosarjassa, joissa sen joustavuus ja kulutuskestävyys ovat olennaisia. POM:ää taas käytetään tyypillisesti tarkkuuskoneissa, kuten liukumekanismeissa, joissa alhainen kitka ja suuri jäykkyys ovat kriittisiä.
7. Ympäristövaikutukset ja kestävä kehitys
Nailonin kierrätys ja biohajoavuus
Nailon ei ole helposti biohajoavaa, ja sen kierrätysprosessi voi olla energiaintensiivinen. Nailonin kierrätystä koskevat innovaatiot ovat kuitenkin edistämässä kestävämpiä käytäntöjä erityisesti tekstiiliteollisuudessa, jossa kierrätettyä nailonia käytetään ympäristöystävällisten tuotteiden valmistukseen.
POM: Kestävyysnäkökohdat ja hallinta
POM-muovia on haastavampi kierrättää sen kiderakenteen vuoksi, mutta se kestää paremmin ympäristön hajoamista. Koska valmistajat ovat yhä enemmän suuntautumassa kohti kestäviä käytäntöjä, POM-muovia käytetään entistä energiatehokkaampiin tuotteisiin, ja kierrätystekniikoita kehitetään parhaillaan.
Ympäristöystävällisten materiaalien suuntaukset ja tutkimuksen edistysaskeleet
Kummallakin materiaalilla on vielä matkaa täydelliseen kestävyyteen. Kasvava kiinnostus biohajoavia polymeerejä ja kierrätystekniikoita kohtaan auttaa kuitenkin tekemään nailonista ja POM-materiaalista ympäristöystävällisempiä erilaisissa teollisissa sovelluksissa.
8. Nailonin ja POM:n kustannusvertailu
Nailonin ja POM:n hintatekijät
Nailon on yleensä edullisempi kuin POM, koska sen käyttöalueet ja tuotantomahdollisuudet ovat laajemmat. POM:n korkeat suorituskykyominaisuudet oikeuttavat kuitenkin usein korkeamman hinnan sovelluksissa, joissa vaaditaan tarkkuutta ja kemikaalien kestävyyttä.
Kustannusanalyysi ostajille ja valmistajille
Materiaalia valittaessa on tärkeää punnita sekä alkuperäisiä kustannuksia että pitkän aikavälin suorituskykyä. Nailon tarjoaa kustannustehokkaamman ratkaisun sovelluksissa, joissa joustavuus ja iskunkestävyys ovat avainasemassa, kun taas POM:n korkeammat alkukustannukset kompensoituvat usein sen ylivoimaisella suorituskyvyllä vaativissa sovelluksissa.
Pitkän aikavälin kustannustehokkuus: Mikä materiaali on investoinnin arvoinen?
Korkean rasituksen ja tarkkuuden sovelluksissa POM:n ylivoimaiset mekaaniset ominaisuudet sekä kulumisen ja kemiallisen hajoamisen kestävyys voivat oikeuttaa investoinnin. Yleiskäyttöön Nylon voi kuitenkin tarjota parhaan vastineen kustannustietoisille valmistajille.
9. Nailonin ja POM:n usein kysytyt kysymykset
Mitkä ovat nailonin ja POM:n tärkeimmät erot?
Nylon on joustavampi ja iskunkestävämpi, kun taas POM on jäykempi, kulutusta kestävämpi ja kestää paremmin kemikaaleja.
Kumpi materiaali on vahvempi: nylon vai POM?
Nylon on yleensä vahvempi vetolujuuden suhteen, kun taas POM on parempi leikkauslujuuden ja jäykkyyden suhteen.
Miten lämpö vaikuttaa nailoniin ja POM-muoviin?
Nailon voi hajota korkeissa lämpötiloissa, kun taas POM säilyy vakaana korkeissa lämpötiloissa.
Voidaanko nailonia tai POM-muovia kierrättää?
Molemmat materiaalit voidaan kierrättää, mutta prosessit eroavat toisistaan. Nailonia kierrätetään yleisemmin tekstiiliteollisuudessa, kun taas POM:n kierrätys on haastavampaa.
Millä teollisuudenaloilla käytetään pääasiassa nylonia ja POM-muovia?
Nailonia käytetään laajalti tekstiileissä, autoteollisuudessa ja kulutustavaroissa, kun taas POM-muovia käytetään pääasiassa tarkkuusosissa ja mekaanisissa komponenteissa esimerkiksi autoteollisuudessa, elektroniikassa ja ilmailu- ja avaruusalalla.
Päätelmä
Yhteenvetona voidaan todeta, että Nylon ja POM ovat kaksi korkean suorituskyvyn teknistä muovia, jotka tarjoavat ainutlaatuisia etuja sovelluksesta riippuen. Niiden kemiallisten ominaisuuksien, mekaanisten lujuusominaisuuksien ja erityisiin ympäristöihin soveltuvuuden ymmärtäminen auttaa valmistajia tekemään tietoon perustuvia päätöksiä. Nailon voi olla ihanteellinen joustavuutta ja kulutuskestävyyttä vaativiin sovelluksiin, kun taas POM on materiaalivalinta tarkkuusosiin, jotka vaativat mittatarkkuutta ja kemikaalien kestävyyttä. Kun otat huomioon kustannusten, kestävyyden ja suorituskykyvaatimusten kaltaiset tekijät, voit valita oikean materiaalin seuraavaan projektiisi ja varmistaa pitkän aikavälin tehokkuuden ja luotettavuuden.