Pengenalan Bahan Nilon untuk Cetakan Injeksi
Di bidang industri plastik, cetakan injeksi menyumbang lebih dari 35% dari produksi global produk plastik, dan kontrol kualitas persiapan bahan baku secara langsung menentukan tingkat kualifikasi produk akhir. Menurut sebuah studi tahun 2022 oleh Asosiasi Industri Plastik Amerika (SPI), 68% cacat kualitas dalam proses pencetakan injeksi terkait dengan persiapan bahan baku yang tidak tepat, dan proporsi ini telah meningkat menjadi 82% dalam penerapan bahan nilon (PA). Artikel ini akan menganalisis secara mendalam enam elemen kunci dari bahan baku nilon persiapan dalam proses pencetakan injeksi, mengungkapkan bagaimana "proses yang tidak terlihat" ini memengaruhi pasar produk plastik yang bernilai ratusan miliar.
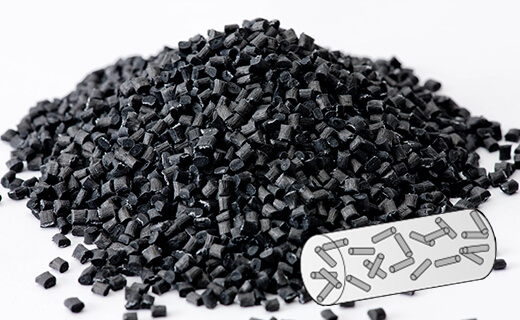
Pemilihan bahan molekuler: pencocokan bahan baku nilon yang tepat
Sebagai "standar emas" plastik rekayasa, bahan nilon mencakup lebih dari 20 jenis seperti PA6, PA66dan PA12. Buku putih teknis raksasa kimia Jerman BASF menunjukkan bahwa titik leleh PA66 (265 ° C) adalah 15% lebih tinggi dari PA6, dan kekuatan tarik meningkat sebesar 23%, tetapi tingkat penyerapan kelembaban juga meningkat sebesar 40%. Dalam cetakan injeksi bagian kap mesin mobil, pemilihan PA66-GF30 (mengandung serat kaca 30%) dapat membuat ketahanan suhu melebihi 200 ° C, yang 60 ° C lebih tinggi dari PA6 biasa. Pemilihan bahan baku perlu mempertimbangkan secara komprehensif sifat mekanik, stabilitas termal, dan karakteristik pemrosesan produk akhir, serta menetapkan matriks parameter kinerja bahan.
Kontrol kualitas tingkat mikron: garis pertahanan ganda untuk pemeriksaan bahan baku
Pabrik-pabrik cetakan injeksi modern umumnya mengadopsi mekanisme pemeriksaan ganda:
① Inspeksi visual untuk menyaring partikel heterokromatik (perbedaan warna ΔE <1,5);
② Analisis ukuran partikel laser untuk memastikan bahwa ukuran partikel berada dalam kisaran 2-3mm.
Data eksperimental dari Sumitomo Chemical Jepang menunjukkan bahwa ukuran partikel yang melebihi standar sebesar 0,5 mm akan meningkatkan keausan sekrup mesin cetak injeksi sebesar 17%, dan pencampuran kotoran 0,1% akan memperpendek usia pakai roda gigi nilon sebesar 30%. Penggunaan spektrometer XRF (seperti seri Olympus Vanta) dapat dengan cepat mendeteksi kandungan logam berat untuk memastikan kepatuhan terhadap standar RoHS 2.0.
Permainan kontrol kelembaban tingkat nano
Sifat higroskopis bahan nilon membuatnya menjadi "bahan sensitif" dalam proses pencetakan injeksi. Dokumen teknis DuPont menunjukkan bahwa apabila kadar air PA6 melebihi 0,2%, garis-garis perak akan muncul pada permukaan produk dan kekuatan benturan akan turun sebesar 40%. Metode pengeringan tiga langkah digunakan:
(1) 80℃ pra-pengeringan selama 2 jam;
Pengeringan utama 120℃ selama 4 jam;
Pengeringan vakum hingga kadar air ≤0,02%.
Dilengkapi dengan monitor titik embun (seperti Motan LD50), titik embun udara kering dapat dipantau secara real time (harus ≤-40 ℃), yang merupakan garis pertahanan utama untuk memastikan kualitas cetakan injeksi nilon.
Rasio emas dari rekayasa formulasi
Dalam cetakan injeksi konektor harness kabel otomotif, formula Ultramid® A3WG10 yang direkomendasikan oleh BASF mengandung:
- Resin dasar PA66 67%
- Serat kaca 30%
- Antioksidan 1.5%
- Pelumas 1.5%
Menggunakan mixer pengukur kehilangan berat (seperti seri Maguire WSB) dapat mencapai akurasi rasio ±0,5%. Kasus American Injection Moulding Association menunjukkan bahwa formula yang dioptimalkan meningkatkan masa pakai konektor dari 5.000 kali menjadi 15.000 kali, sekaligus mengurangi tingkat deformasi lengkungan sebesar 83%.
Revolusi kolaborasi peralatan yang cerdas
Sistem cetakan injeksi modern mencapai hubungan parameter melalui Internet of Things industri:
- Pemantauan pemuatan hopper (akurasi ±1kg)
- Kontrol suhu barel lima tahap (rekomendasi PA66: 240-280 ℃)
- Penyesuaian PID untuk kecepatan sekrup dan tekanan balik Sistem Smart Power pada mesin cetak injeksi Arburg Jerman menunjukkan bahwa ketika suhu barel berfluktuasi lebih dari ±3℃, viskositas lelehan berubah sebesar 15%. Pada saat ini, sistem secara otomatis mengkompensasi tekanan injeksi (kisaran penyesuaian ±8%) untuk memastikan stabilitas pencetakan.
Rekonstruksi molekuler dari proses peleburan
Selama tahap plastisisasi cetakan injeksi nilon, desain sekrup secara langsung memengaruhi susunan rantai molekul. Penggunaan sekrup penghalang (seperti seri HPM) dapat meningkatkan keseragaman suhu leleh sebesar 30% dan mengurangi konsumsi energi sebesar 15%. Penelitian oleh Swiss Buhler Group telah mengkonfirmasi bahwa menjaga lelehan di dalam laras selama 90-120 detik dapat membuat kristalinitas PA66 mencapai kisaran optimal 45-50%, dan kekuatan tarik meningkat sebesar 18%.
Kesimpulan
Di era Industri 4.0, persiapan bahan baku telah ditingkatkan dari proses tambahan menjadi penghubung inti manufaktur cerdas. Pusat Nasional Ilmu Manufaktur di Amerika Serikat memperkirakan bahwa pada tahun 2025, sistem persiapan bahan baku yang cerdas akan mengurangi tingkat sisa cetakan injeksi sebesar 75% dan mempersingkat waktu penggantian cetakan sebesar 60%. Untuk bahan berkinerja tinggi seperti nilon, hanya dengan membangun sistem pengetahuan yang lengkap dari desain molekuler hingga kontrol proses, parit teknologi dapat dibangun dalam persaingan pasar yang ketat. Seperti yang dikatakan Patrick Farrey, presiden Society of Plastics Engineering (SPE): "Masa depan persaingan cetakan injeksi dimulai dengan milimeter di stasiun persiapan bahan baku."