Introduction of Nylon Material for Injection Molding
In the field of plastics industry, injection molding accounts for more than 35% of the global production of plastic products, and the quality control of raw material preparation directly determines the final product qualification rate. According to a 2022 study by the American Plastics Industry Association (SPI), 68% of quality defects in the injection molding process are related to improper raw material preparation, and this proportion has risen to 82% in the application of nylon (PA) materials. This article will deeply analyze the six key elements of nylon raw material preparation in the injection molding process, revealing how this “invisible process” affects the plastic products market worth hundreds of billions.
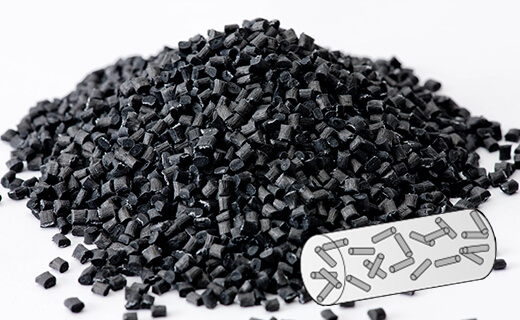
Molecular material selection: precise matching of nylon raw materials
As the “gold standard” of engineering plastics, nylon materials include more than 20 types such as PA6, PA66, and PA12. The technical white paper of German chemical giant BASF pointed out that the melting point of PA66 (265°C) is 15% higher than that of PA6, and the tensile strength is increased by 23%, but the moisture absorption rate is also increased by 40%. In the injection molding of automobile engine hood parts, the selection of PA66-GF30 (containing 30% glass fiber) can make the temperature resistance exceed 200°C, which is 60°C higher than that of ordinary PA6. The selection of raw materials needs to comprehensively consider the mechanical properties, thermal stability and processing characteristics of the end product, and establish a material performance parameter matrix.
Micron-level quality control: double line of defense for raw material inspection
Modern injection molding factories generally adopt a double inspection mechanism:
① Visual inspection to screen out heterochromatic particles (color difference ΔE<1.5);
② Laser particle size analysis to ensure that the particle size is in the range of 2-3mm.
Experimental data from Sumitomo Chemical of Japan show that a particle size exceeding the standard by 0.5mm will increase the wear of the injection molding machine screw by 17%, and the mixing of 0.1% impurities will shorten the fatigue life of nylon gears by 30%. The use of XRF spectrometers (such as the Olympus Vanta series) can quickly detect heavy metal content to ensure compliance with RoHS 2.0 standards.
Nano-level game of humidity control
The hygroscopic properties of nylon materials make them “sensitive materials” in the injection molding process. DuPont’s technical documents show that when the moisture content of PA6 exceeds 0.2%, silver streaks will appear on the surface of the product and the impact strength will drop by 40%. A three-step drying method is used:
① 80℃ pre-drying for 2 hours;
② 120℃ main drying for 4 hours;
③ vacuum drying to a moisture content of ≤0.02%.
Equipped with a dew point monitor (such as Motan LD50), the dew point of dry air can be monitored in real time (needed to be ≤-40℃), which is the key line of defense to ensure the quality of nylon injection molding.
The golden ratio of formulation engineering
In the injection molding of automotive wiring harness connectors, the Ultramid® A3WG10 formula recommended by BASF contains:
- PA66 base resin 67%
- Glass fiber 30%
- Antioxidant 1.5%
- Lubricant 1.5%
Using a loss-in-weight metering mixer (such as the Maguire WSB series) can achieve a ratio accuracy of ±0.5%. The case of the American Injection Molding Association shows that the optimized formula increases the plug-in life of the connector from 5,000 times to 15,000 times, while reducing the warpage deformation rate by 83%.
Intelligent revolution of equipment collaboration
Modern injection molding systems achieve parameter linkage through industrial Internet of Things:
- Hopper loading monitoring (±1kg accuracy)
- Five-stage barrel temperature control (PA66 recommendation: 240-280℃)
- PID adjustment of screw speed and back pressure The Smart Power system of the German Arburg injection molding machine shows that when the barrel temperature fluctuates by more than ±3℃, the melt viscosity changes by 15%. At this time, the system automatically compensates the injection pressure (adjustment range ±8%) to ensure molding stability.
Molecular reconstruction of the melting process
During the plasticization stage of nylon injection molding, the screw design directly affects the arrangement of molecular chains. The use of barrier screws (such as the HPM series) can improve the uniformity of melt temperature by 30% and reduce energy consumption by 15%. Research by the Swiss Buhler Group has confirmed that keeping the melt in the barrel for 90-120 seconds can make the crystallinity of PA66 reach the optimal range of 45-50%, and the tensile strength increase by 18%.
Conclusion
In the era of Industry 4.0, raw material preparation has been upgraded from an auxiliary process to the core link of intelligent manufacturing. The National Center for Manufacturing Sciences in the United States predicts that by 2025, the intelligent raw material preparation system will reduce the injection molding scrap rate by 75% and shorten the mold change time by 60%. For high-performance materials such as nylon, only by establishing a complete knowledge system from molecular design to process control can a technological moat be built in the fierce market competition. As Patrick Farrey, president of the Society of Plastics Engineering (SPE), said: “The future of injection molding competition begins with millimeters at the raw material preparation station.”