Introdução do material de nylon para moldagem por injeção
No campo da indústria de plásticos, a moldagem por injeção é responsável por mais de 35% da produção global de produtos plásticos, e o controle de qualidade da preparação da matéria-prima determina diretamente a taxa de qualificação do produto final. De acordo com um estudo de 2022 da Associação Americana da Indústria de Plásticos (SPI), 68% de defeitos de qualidade no processo de moldagem por injeção estão relacionados com a preparação inadequada da matéria-prima, e esta proporção aumentou para 82% na aplicação de materiais de nylon (PA). Este artigo analisará em profundidade os seis elementos-chave da matéria-prima de nylon no processo de moldagem por injeção, revelando como este "processo invisível" afecta o mercado de produtos plásticos no valor de centenas de milhares de milhões.
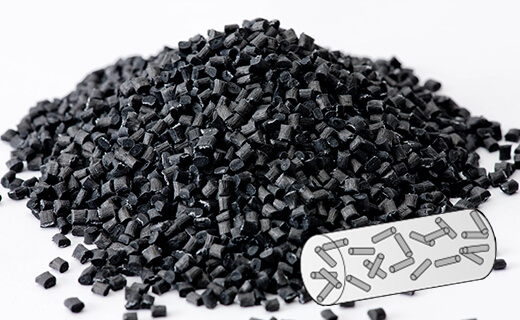
Seleção de material molecular: correspondência precisa de matérias-primas de nylon
Sendo o "padrão de ouro" dos plásticos de engenharia, os materiais de nylon incluem mais de 20 tipos, tais como PA6, PA66e PA12. O livro branco técnico do gigante químico alemão BASF salientou que o ponto de fusão do PA66 (265°C) é 15% superior ao do PA6, e a resistência à tração é aumentada em 23%, mas a taxa de absorção de humidade também é aumentada em 40%. Na moldagem por injeção de peças de capô de motor de automóvel, a seleção de PA66-GF30 (contendo fibra de vidro 30%) pode fazer com que a resistência à temperatura ultrapasse os 200°C, o que é 60°C superior à do PA6 comum. A seleção de matérias-primas tem de considerar de forma abrangente as propriedades mecânicas, a estabilidade térmica e as caraterísticas de processamento do produto final, e estabelecer uma matriz de parâmetros de desempenho do material.
Controlo de qualidade ao nível do mícron: dupla linha de defesa para a inspeção de matérias-primas
As modernas fábricas de moldagem por injeção adoptam geralmente um duplo mecanismo de inspeção:
① Inspeção visual para excluir partículas heterocromáticas (diferença de cor ΔE<1,5);
② Análise de tamanho de partícula a laser para garantir que o tamanho da partícula esteja na faixa de 2-3mm.
Os dados experimentais da Sumitomo Chemical do Japão mostram que um tamanho de partícula que exceda a norma em 0,5 mm aumentará o desgaste do parafuso da máquina de moldagem por injeção em 17%, e a mistura de impurezas de 0,1% encurtará a vida à fadiga das engrenagens de nylon em 30%. A utilização de espectrómetros XRF (como a série Olympus Vanta) pode detetar rapidamente o teor de metais pesados para garantir a conformidade com as normas RoHS 2.0.
Jogo de controlo da humidade a nível nanométrico
As propriedades higroscópicas dos materiais de nylon tornam-nos "materiais sensíveis" no processo de moldagem por injeção. Os documentos técnicos da DuPont mostram que, quando o teor de humidade do PA6 excede 0,2%, aparecem estrias prateadas na superfície do produto e a resistência ao impacto diminui 40%. É utilizado um método de secagem em três fases:
① 80℃ pré-secagem durante 2 horas;
② 120℃ secagem principal durante 4 horas;
③ secagem sob vácuo até um teor de humidade ≤0,02%.
Equipado com um monitor de ponto de orvalho (como o Motan LD50), o ponto de orvalho do ar seco pode ser monitorado em tempo real (necessário para ser ≤-40 ℃), que é a principal linha de defesa para garantir a qualidade da moldagem por injeção de nylon.
O rácio dourado da engenharia de formulações
Na moldagem por injeção de conectores de cablagem para automóveis, a fórmula Ultramid® A3WG10 recomendada pela BASF contém:
- Resina de base PA66 67%
- Fibra de vidro 30%
- Antioxidante 1.5%
- Lubrificante 1.5%
A utilização de um misturador de medição de perda de peso (como a série Maguire WSB) pode atingir uma precisão de rácio de ±0,5%. O caso da Associação Americana de Moldagem por Injeção mostra que a fórmula optimizada aumenta a vida útil do conetor de 5.000 vezes para 15.000 vezes, enquanto reduz a taxa de deformação por empenamento em 83%.
Revolução inteligente da colaboração entre equipamentos
Os modernos sistemas de moldagem por injeção conseguem a ligação de parâmetros através da Internet das Coisas industrial:
- Monitorização do carregamento da tremonha (precisão de ±1kg)
- Controlo da temperatura do barril em cinco fases (recomendação PA66: 240-280℃)
- Ajuste PID da velocidade do parafuso e da contrapressão O sistema Smart Power da máquina de moldagem por injeção alemã Arburg mostra que quando a temperatura do barril flutua em mais de ± 3 ℃, a viscosidade do fundido muda em 15%. Neste momento, o sistema compensa automaticamente a pressão de injeção (faixa de ajuste ± 8%) para garantir a estabilidade da moldagem.
Reconstrução molecular do processo de fusão
Durante a fase de plastificação da moldagem por injeção de nylon, o desenho do parafuso afecta diretamente a disposição das cadeias moleculares. A utilização de parafusos de barreira (como os da série HPM) pode melhorar a uniformidade da temperatura de fusão em 30% e reduzir o consumo de energia em 15%. A investigação do Swiss Buhler Group confirmou que manter a massa fundida no cilindro durante 90-120 segundos pode fazer com que a cristalinidade do PA66 atinja o intervalo ótimo de 45-50% e a resistência à tração aumente 18%.
Conclusão
Na era da Indústria 4.0, a preparação de matérias-primas foi actualizada de um processo auxiliar para o elo central do fabrico inteligente. O Centro Nacional de Ciências da Fabricação dos Estados Unidos prevê que, até 2025, o sistema inteligente de preparação de matérias-primas reduzirá a taxa de refugo de moldagem por injeção em 75% e encurtará o tempo de troca de molde em 60%. Para materiais de alto desempenho como o nylon, só estabelecendo um sistema de conhecimento completo, desde a conceção molecular até ao controlo do processo, é possível construir um fosso tecnológico na feroz concorrência do mercado. Como afirmou Patrick Farrey, presidente da Society of Plastics Engineering (SPE): "O futuro da concorrência na moldagem por injeção começa com milímetros na estação de preparação da matéria-prima."