Introducción del material de nailon para moldeo por inyección
En el campo de la industria del plástico, el moldeo por inyección representa más de 35% de la producción mundial de productos de plástico, y el control de calidad de la preparación de la materia prima determina directamente el índice de cualificación del producto final. Según un estudio de 2022 de la Asociación Americana de la Industria del Plástico (SPI), 68% de los defectos de calidad en el proceso de moldeo por inyección están relacionados con una preparación inadecuada de la materia prima, y esta proporción ha aumentado a 82% en la aplicación de materiales de nailon (PA). Este artículo analizará en profundidad los seis elementos clave de materia prima de nailon preparación en el proceso de moldeo por inyección, revelando cómo este "proceso invisible" afecta al mercado de productos plásticos valorados en cientos de miles de millones.
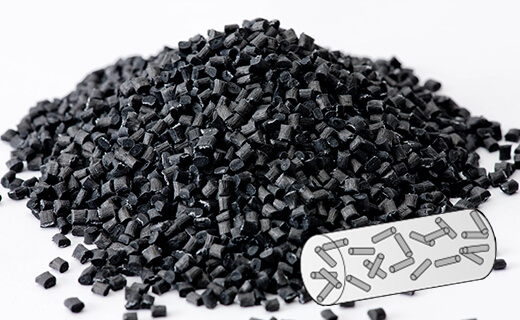
Selección de materiales moleculares: combinación precisa de materias primas de nailon
Como "patrón oro" de los plásticos de ingeniería, los materiales de nailon incluyen más de 20 tipos como PA6, PA66y PA12. El libro blanco técnico del gigante químico alemán BASF señalaba que el punto de fusión de la PA66 (265°C) es 15% superior al de la PA6, y la resistencia a la tracción se incrementa en 23%, pero el índice de absorción de humedad también aumenta en 40%. En el moldeo por inyección de piezas del capó del motor del automóvil, la selección de PA66-GF30 (que contiene fibra de vidrio 30%) puede hacer que la resistencia a la temperatura supere los 200°C, que es 60°C superior a la de la PA6 ordinaria. La selección de materias primas debe tener en cuenta las propiedades mecánicas, la estabilidad térmica y las características de procesamiento del producto final, y establecer una matriz de parámetros de rendimiento del material.
Control de calidad micrométrico: doble línea de defensa para la inspección de materias primas
Las modernas fábricas de moldeo por inyección suelen adoptar un doble mecanismo de inspección:
① Inspección visual para descartar partículas heterocromáticas (diferencia de color ΔE<1,5);
② Análisis granulométrico por láser para garantizar que el tamaño de las partículas se encuentra en el intervalo de 2-3 mm.
Los datos experimentales de Sumitomo Chemical de Japón muestran que un tamaño de partícula que supere la norma en 0,5 mm aumentará el desgaste del tornillo de la máquina de moldeo por inyección en 17%, y la mezcla de impurezas de 0,1% acortará la vida a la fatiga de los engranajes de nailon en 30%. El uso de espectrómetros XRF (como la serie Olympus Vanta) puede detectar rápidamente el contenido de metales pesados para garantizar el cumplimiento de las normas RoHS 2.0.
Juego de control de la humedad a nivel nanométrico
Las propiedades higroscópicas de los materiales de nailon los convierten en "materiales sensibles" en el proceso de moldeo por inyección. Los documentos técnicos de DuPont muestran que cuando el contenido de humedad de la PA6 supera los 0,2%, aparecen vetas plateadas en la superficie del producto y la resistencia al impacto disminuye en 40%. Se utiliza un método de secado en tres etapas:
① 80℃ presecado durante 2 horas;
② 120℃ de secado principal durante 4 horas;
③ secado al vacío hasta un contenido de humedad de ≤0,02%.
Equipado con un monitor de punto de rocío (como Motan LD50), el punto de rocío del aire seco puede ser monitoreado en tiempo real (necesario para ser ≤-40℃), que es la línea clave de defensa para garantizar la calidad del moldeo por inyección de nylon.
La proporción áurea de la ingeniería de formulación
En el moldeo por inyección de conectores de mazos de cables de automoción, la fórmula Ultramid® A3WG10 recomendada por BASF contiene:
- Resina base PA66 67%
- Fibra de vidrio 30%
- Antioxidante 1.5%
- Lubricante 1.5%
Utilizando un mezclador dosificador de pérdida de peso (como la serie WSB de Maguire) se puede conseguir una precisión de relación de ±0,5%. El caso de la Asociación Americana de Moldeo por Inyección muestra que la fórmula optimizada aumenta la vida útil del conector de 5.000 a 15.000 veces, al tiempo que reduce la tasa de deformación por alabeo en 83%.
Revolución inteligente de la colaboración entre equipos
Los sistemas modernos de moldeo por inyección logran la vinculación de parámetros a través del Internet industrial de las cosas:
- Control de la carga de la tolva (precisión de ±1 kg)
- Control de temperatura del barril en cinco etapas (recomendación PA66: 240-280℃)
- Ajuste PID de la velocidad del tornillo y la contrapresión El sistema Smart Power de la máquina de moldeo por inyección alemana Arburg muestra que cuando la temperatura del barril fluctúa en más de ±3℃, la viscosidad de la masa fundida cambia en 15%. En ese momento, el sistema compensa automáticamente la presión de inyección (rango de ajuste ±8%) para garantizar la estabilidad del moldeo.
Reconstrucción molecular del proceso de fusión
Durante la etapa de plastificación del moldeo por inyección de nailon, el diseño del tornillo afecta directamente a la disposición de las cadenas moleculares. El uso de tornillos de barrera (como los de la serie HPM) puede mejorar la uniformidad de la temperatura de la masa fundida en 30% y reducir el consumo de energía en 15%. Las investigaciones del grupo suizo Buhler han confirmado que mantener la masa fundida en el barril durante 90-120 segundos puede hacer que la cristalinidad de la PA66 alcance el rango óptimo de 45-50%, y que la resistencia a la tracción aumente en 18%.
Conclusión
En la era de la Industria 4.0, la preparación de materias primas ha pasado de ser un proceso auxiliar a convertirse en el eslabón central de la fabricación inteligente. El Centro Nacional de Ciencias de la Fabricación de Estados Unidos predice que, para 2025, el sistema inteligente de preparación de materias primas reducirá la tasa de desechos de moldeo por inyección en 75% y acortará el tiempo de cambio de molde en 60%. En el caso de los materiales de alto rendimiento, como el nailon, sólo estableciendo un sistema de conocimiento completo, desde el diseño molecular hasta el control de procesos, se puede construir un foso tecnológico en la feroz competencia del mercado. Como dijo Patrick Farrey, presidente de la Sociedad de Ingeniería de Plásticos (SPE): "El futuro de la competencia en el moldeo por inyección empieza con los milímetros en la estación de preparación de la materia prima".