Introduction
Sous l'impulsion de la double force des automobiles légères et de l'industrie 4.0, PA6 (polyamide 6) est en train de devenir le plastique technique qui connaît la croissance la plus rapide au monde, avec un taux de croissance annuel moyen de 5,3%. Ce matériau thermoplastique semi-cristallin est devenu le premier choix dans des domaines clés tels que les engrenages, les roulements et les pièces automobiles en raison de sa grande solidité, de sa résistance à l'usure et de sa résistance à la corrosion chimique. Cet article analyse en profondeur les cinq technologies de base et révèle comment libérer les performances ultimes du PA6 grâce à un contrôle précis du processus.
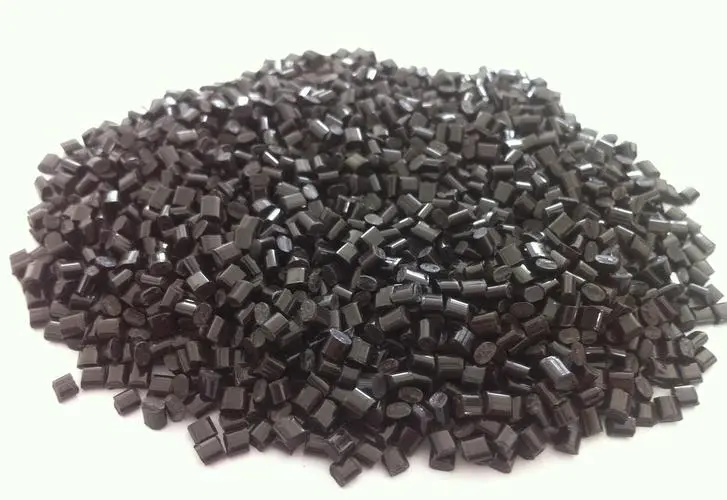
1. Prétraitement des matériaux : le contrôle de l'humidité détermine le succès ou l'échec
L'hygroscopicité du PA6 est une "arme à double tranchant" dans son traitement - les matériaux non séchés provoquent des défauts tels que des bulles et des stries argentées dans le produit fini. Les expériences montrent que lorsque la teneur en humidité dépasse 0,2%, la résistance à la traction diminue de 18%. Paramètres clés du processus:
- Température de séchage : 80-100℃ système en boucle fermée (30% meilleur que le séchage traditionnel à l'air chaud).
- Temps de séchage : 16-24 heures (ajusté dynamiquement en fonction de l'humidité ambiante)
- Contrôle du point de rosée : <-40℃ (pour éviter l'absorption secondaire d'humidité) Les leaders de l'industrie tels qu'Arburg ont développé des systèmes de séchage intelligents qui surveillent la teneur en humidité en temps réel grâce à l'Internet des objets, réduisant ainsi le taux de rebut à moins de 0,5%.
2. Moulage par injection de précision : l'art du champ de température
Le moulage par injection représente 67% du marché de la transformation du PA6, et sa technologie de base réside dans le contrôle du gradient de température :
- Température de fusion: 230-280℃ contrôle en couches (section frontale 230℃/section médiane 250℃/buse 280℃).
- Température du mouleSystème de température constante 80-90℃ (différence de température de ±2℃ pour assurer la cohérence de la cristallinité).
- Courbe de pressionLa machine de moulage par injection servoélectrique de KraussMaffei en Allemagne utilise un réglage en temps réel par le biais du capteur de pression dans le moule pour que la précision du profil de la dent des engrenages en PA6 soit conforme à la norme DIN 5.
3. Renforcement et modification : la clé de l'amélioration des performances
Le PA6-GF30 renforcé par des fibres de verre 30% a un module de flexion allant jusqu'à 9500MPa, soit 400% de plus que le PA6 pur (source de données : Rapport technique de DuPont). Les dernières tendances technologiques sont les suivantes :
- Renforcement par nano-argile: L'ajout de la nano-montmorillonite 3% augmente la température de déformation thermique de 25°C.
- Hybride en fibre de carbone: 15% fibre de carbone hachée + 15% fibre de verre pour atteindre l'isotropie
- Modification autolubrifiante: En ajoutant du MoS₂ ou du graphène, le coefficient de frottement est réduit à 0,08 Les matériaux composites PA6+fibres de carbone développés par Victrex ont été utilisés avec succès dans les composants hydrauliques de l'aérospatiale, augmentant leur durée de vie de 3 fois.
4. Innovation dans le domaine des moules : la bataille de la précision au micron près
L'optimisation de la conception des moules permet de réduire le cycle de moulage de 20% tout en améliorant la stabilité dimensionnelle :
- Système de canaux chaudsLes produits de la catégorie "Autres" : réduisent la rétention de la matière fondue et évitent la dégradation thermique.
- Canal d'eau de refroidissement conforme: Le moule d'impression 3D atteint une uniformité de température de ±0,5℃.
- Structure d'échappement: Conception de la rainure d'échappement à gradins de 0,03 mm Boîtier : Japon [Fanuc] (https://www.fanuc.com) utilise la technologie de chauffage par induction dans le moule pour que la rugosité de la surface des connecteurs automobiles en PA6 atteigne Ra0,8μm.
5. Processus de post-traitement : le deuxième saut de performance
- Traitement de recuit: Recuit de 120℃×4h, éliminant les contraintes internes et améliorant la stabilité dimensionnelle par 30%.
- Conditionnement de l'humidité: 48h d'équilibre dans un environnement 65%RH, et 50% d'augmentation de la résistance à l'impact
- Modification de la surface: Le traitement au plasma permet au revêtement d'atteindre un niveau d'adhérence de 5B. ProtolabsLa ligne de post-traitement automatisé de l'entreprise permet de gérer sans personnel l'ensemble du processus de fabrication des pièces en PA6, depuis le moulage jusqu'à l'emballage.
Conclusion
Du prétraitement par séchage au post-traitement intelligent, la technologie de traitement du PA6 évolue vers la numérisation et la haute précision. En maîtrisant ces cinq technologies de base, les entreprises peuvent maximiser le potentiel du PA6 - tout en maintenant la compétitivité des coûts, la résistance à la traction dépasse 85MPa et la température de déformation thermique atteint 180℃. Une référence dans l'industrie, Fuchen New MaterialLe mélange PA6/PA66 d'IATF a obtenu la certification IATF 16949. Sa formule innovante à faible déformation redéfinit les limites de performance des pièces automobiles.
Contact L'équipe technique de Fuchen pour obtenir des solutions personnalisées de traitement du PA6 et entrer dans une nouvelle ère de fabrication à haute performance !