Introduction à la PA66 GF33 Composites
PA66, communément appelé nylon 66Le GF33 est un polymère thermoplastique semi-cristallin reconnu pour ses propriétés mécaniques remarquables telles que la résistance, la rigidité et la ténacité. Le GF33 désigne la fibre de verre renforcée par une matrice polymère. En les combinant, le PA66 et le GF33 créent un matériau composite aux caractéristiques mécaniques supérieures. Cette combinaison unique a rendu les composites PA66 et GF33 indispensables dans de nombreuses industries, notamment l'automobile, l'aérospatiale et la construction.
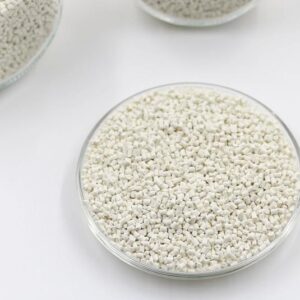
Applications dans l'industrie automobile
Améliorer les performances et l'efficacité des véhicules
Dans le secteur automobile, les composites PA66 GF33 font partie intégrante de la fabrication de composants tels que les pièces de moteur, les systèmes de transmission et les panneaux de carrosserie. Leur rapport résistance/poids élevé permet de produire des pièces légères mais robustes, capables de résister à des charges importantes et à des températures élevées. Cela permet non seulement d'améliorer les performances des véhicules, mais aussi d'augmenter le rendement énergétique et de réduire les émissions. En outre, le remplacement de matériaux traditionnels tels que l'acier et l'aluminium par ces composites permet de réaliser des économies substantielles.
Applications dans l'industrie aérospatiale
Faire progresser la conception des aéronefs et le développement durable
L'industrie aérospatiale utilise largement les composites PA66-GF33 pour produire des composants d'avions tels que les ailes, les panneaux de fuselage et les trains d'atterrissage. Ces composites sont appréciés pour leur grande solidité, leur rigidité et leur excellente résistance à la fatigue. Leur légèreté joue un rôle crucial dans l'amélioration du rendement énergétique et la réduction des émissions, qui sont essentielles pour l'industrie. En outre, les composites PA66-GF33 offrent une résistance thermique et chimique exceptionnelle, ce qui les rend adaptés aux environnements exigeants rencontrés dans les applications aérospatiales.
Applications dans l'industrie de la construction
Construire des structures durables et efficaces
Dans le domaine de la construction, les composites PA66-GF33 sont utilisés pour créer des matériaux de construction tels que des cadres de fenêtres, des tuiles et des panneaux d'isolation. Ces matériaux sont appréciés pour leur grande résistance et leur durabilité, ce qui les rend idéaux pour résister à des conditions météorologiques difficiles telles que des vents violents et des pluies torrentielles. La légèreté de ces composites se traduit également par des coûts de transport et d'installation plus faibles, ainsi que par une maintenance réduite au fil du temps, ce qui en fait une solution rentable pour les besoins de la construction moderne.
Conclusion
Perspectives d'avenir et élargissement des applications des composites PA66-GF33
Les composites PA66-GF33 sont réputés pour leurs propriétés mécaniques exceptionnelles et leur polyvalence. Ils trouvent des applications dans divers secteurs tels que l'automobile, l'aérospatiale et la construction. Ils permettent de produire des composants légers et durables tout en offrant des économies et des performances accrues. À mesure que la technologie progresse, les applications potentielles de ces composites devraient s'accroître, mettant en évidence leur adaptabilité et leur impact significatif dans divers secteurs.
FAQ sur les composites PA66 GF33
Aperçu détaillé des composites PA66 GF33, de leurs caractéristiques, de leurs utilisations, de leurs avantages et de leurs développements futurs.
1. Qu'est-ce que le PA66 GF33 ?
Il s'agit d'un matériau composite composé de polyamide 66 (PA66), communément appelé nylon 66, renforcé par des fibres de verre 33% (GF). Cette combinaison améliore les propriétés mécaniques du PA66, offrant une résistance, une rigidité et une durabilité supérieures à celles du polymère non chargé. Les fibres de verre sont intégrées dans la matrice du PA66, créant ainsi un composite robuste et polyvalent.
2. Quelles sont les principales propriétés du PA66 GF33 ?
Il est connu pour plusieurs propriétés exceptionnelles :
- Résistance et rigidité élevées: Les fibres de verre améliorent considérablement la résistance à la traction et à la flexion du matériau.
- Excellente stabilité thermique: Il peut fonctionner efficacement à des températures plus élevées que beaucoup d'autres plastiques techniques.
- Bonne résistance à la fatigue et à l'usure: Convient aux applications nécessitant des performances mécaniques à long terme.
- Stabilité dimensionnelle: Le composite conserve sa forme et résiste au gauchissement sous l'effet de la charge et de la chaleur.
- Résistance chimique: Il résiste à une large gamme de produits chimiques, d'huiles et de solvants.
- Faible absorption d'humidité: Le PA66 absorbe moins d'humidité que les autres polyamides, ce qui réduit son impact sur les propriétés mécaniques.
3. Quelles sont les applications courantes du PA66 GF33 ?
Il est utilisé dans diverses industries en raison de ses caractéristiques de performance robustes :
Industrie automobile
- Moteur et composants sous le capot: Comme les collecteurs d'admission d'air, les carters d'huile et les boîtiers de thermostat.
- Parties structurelles: Y compris les consoles, les supports et les divers éléments porteurs.
- Composants intérieurs et extérieurs: Comme les poignées de porte, les cadres de sièges et les boîtiers de rétroviseurs.
Industrie aérospatiale
- Composants d'aéronefs: Tels que les panneaux, les supports et les supports structurels, pour lesquels la réduction du poids et une grande résistance sont essentielles.
- Pièces des systèmes électriques et hydrauliques: Composants devant résister à des températures élevées et à des produits chimiques agressifs.
Applications industrielles
- Pièces de machines: Engrenages, roulements et paliers nécessitant une résistance à l'usure et une stabilité élevées.
- Composants d'outils et d'équipements: Pièces utilisées dans les outils électriques et les machines lourdes.
Électricité et électronique
- Boîtiers de connecteurs: Isolation électrique et protection mécanique.
- Interrupteurs et disjoncteurs: Bénéficier de la solidité et de la résistance thermique du matériau.
Biens de consommation
- Produits durables: Articles tels que les équipements sportifs et les composants d'appareils ménagers qui nécessitent une combinaison de résistance et de durabilité.
4. Comment le PA66 GF33 se compare-t-il à d'autres matériaux ?
Il présente plusieurs avantages par rapport à d'autres matériaux :
- Par rapport au PA6 GF33: Le PA66-GF33 offre généralement une meilleure résistance à la chaleur et une meilleure résistance mécanique, bien que le PA6 GF33 puisse offrir une meilleure aptitude à la transformation et un coût inférieur.
- Par rapport aux métaux: Il est beaucoup plus léger et souvent moins coûteux, avec une excellente résistance pour de nombreuses applications.
- Par rapport au PA66 non renforcé: L'ajout de fibres de verre améliore considérablement la rigidité, la résistance et les performances thermiques, ce qui le rend adapté aux applications les plus exigeantes.
5. Quelles sont les méthodes de transformation du PA66 GF33 ?
Il peut être transformé à l'aide des techniques de transformation des thermoplastiques standard :
- Moulage par injection: Idéal pour la production de pièces complexes et de haute précision.
- Extrusion: Utilisé pour fabriquer des profilés continus tels que des tiges, des tubes et des feuilles.
- Moulage par compression: Convient pour les grandes pièces et les composants nécessitant une grande résistance.
- Moulage par soufflage: Utilisé dans la production de pièces creuses, telles que les conduits et les conteneurs.
6. Quels sont les avantages de l'utilisation du PA66 GF33 dans la fabrication ?
PA66 GF33 offre plusieurs avantages clés :
- Réduction du poids: Son rapport résistance/poids élevé permet d'obtenir des composants plus légers, ce qui est essentiel pour les applications où les économies de poids sont cruciales, comme dans l'automobile et l'aérospatiale.
- Rentabilité: Il peut remplacer des matériaux plus lourds et plus coûteux comme les métaux, ce qui permet de réduire les coûts des matériaux et des processus de fabrication.
- Amélioration des performances: Les propriétés mécaniques améliorées du composite lui permettent de bien fonctionner sous des charges et des températures élevées, ce qui prolonge la durée de vie des composants.
- Flexibilité de la conception: Le matériau peut être moulé dans des formes complexes, ce qui offre de vastes possibilités de conception.
- Avantages pour l'environnement: Les composants légers contribuent à améliorer le rendement énergétique et à réduire les émissions des véhicules et des avions.
7. Existe-t-il des limites ou des défis associés au PA66 GF33 ?
Tandis que il offre de nombreux avantages, elle présente également certaines limites :
- Augmentation de la densité: L'ajout de fibres de verre augmente la densité du composite par rapport au PA66 non chargé.
- Finition de la surface: La présence de fibres de verre peut donner une surface plus rugueuse, qui peut ne pas convenir à des applications nécessitant une finition lisse.
- Potentiel d'anisotropie: Les fibres de verre peuvent s'aligner dans certaines directions au cours du traitement, ce qui entraîne des variations des propriétés mécaniques en fonction de l'orientation.
- Températures de traitement plus élevées: Le PA66-GF33 nécessite des températures de moulage plus élevées que d'autres plastiques, ce qui peut influencer le choix de l'équipement de fabrication.
- Sensibilité à l'humidité: Bien que le PA66-GF33 absorbe moins d'humidité que les autres polyamides, celle-ci peut encore affecter les propriétés mécaniques et la stabilité dimensionnelle. Un conditionnement adéquat est nécessaire pour les applications critiques.
8. Quelles sont les tendances et les évolutions futures des composites PA66 GF33 ?
Il devrait continuer à évoluer en fonction des progrès réalisés dans le domaine de la science des matériaux et de la fabrication :
- Formulations améliorées: Des recherches sont en cours pour améliorer les propriétés du composite, comme l'augmentation de sa résistance aux chocs ou l'introduction de caractéristiques ignifuges.
- Matériaux durables: Des efforts sont faits pour incorporer des fibres de verre recyclées et des polyamides biosourcés afin de créer des composites plus respectueux de l'environnement.
- Techniques de transformation innovantes: Des techniques telles que l'impression 3D sont explorées pour étendre les capacités de conception et de fabrication des composites PA66-GF33.
- Des applications plus larges: L'industrie exigeant des matériaux plus légers, plus résistants et plus durables, l'utilisation du PA66-GF33 est susceptible d'augmenter, en particulier dans les domaines émergents tels que les véhicules électriques et les énergies renouvelables.