Внедрение нейлонового материала для литья под давлением
В сфере производства пластмасс на литье под давлением приходится более 35% мирового производства пластмассовых изделий, и контроль качества подготовки сырья напрямую определяет уровень квалификации конечного продукта. Согласно исследованию Американской ассоциации индустрии пластмасс (SPI), проведенному в 2022 году, 68% дефектов качества в процессе литья под давлением связаны с неправильной подготовкой сырья, и эта доля возросла до 82% при использовании нейлоновых (PA) материалов. В этой статье будет проведен глубокий анализ шести ключевых элементов нейлоновое сырьё подготовка в процессе литья под давлением, показывая, как этот "невидимый процесс" влияет на рынок пластмассовых изделий стоимостью в сотни миллиардов.
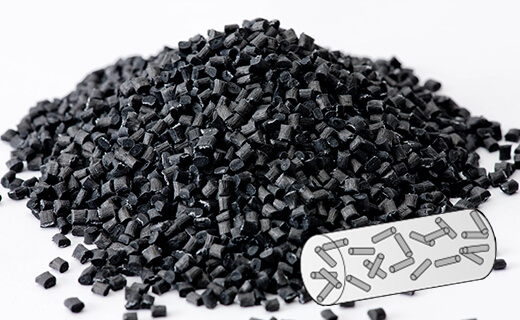
Выбор молекулярного материала: точный подбор нейлонового сырья
Являясь "золотым стандартом" инженерных пластмасс, нейлоновые материалы включают в себя более 20 видов, таких как PA6, PA66, и PA12. В техническом документе немецкого химического гиганта BASF отмечается, что температура плавления PA66 (265°C) на 15% выше, чем у PA6, а прочность на разрыв увеличивается на 23%, но при этом показатель поглощения влаги также увеличивается на 40%. При литье под давлением деталей капота автомобильного двигателя выбор PA66-GF30 (содержащего стекловолокно 30%) может обеспечить термостойкость свыше 200°C, что на 60°C выше, чем у обычного PA6. При выборе сырья необходимо всесторонне учитывать механические свойства, термостойкость и технологические характеристики конечного продукта, а также составлять матрицу параметров характеристик материала.
Контроль качества на микронном уровне: двойная линия защиты при проверке сырья
Современные заводы по литью под давлением обычно используют двойной механизм контроля:
① Визуальный осмотр для отсеивания гетерохроматических частиц (разница в цвете ΔE<1,5);
② Лазерный анализ размера частиц, чтобы убедиться, что размер частиц находится в диапазоне 2-3 мм.
Экспериментальные данные японской компании Sumitomo Chemical показывают, что размер частиц, превышающий стандарт на 0,5 мм, увеличивает износ шнека термопластавтомата на 17%, а смешение примесей в количестве 0,1% сокращает усталостный ресурс нейлоновых шестеренок на 30%. Использование спектрометров XRF (например, Olympus серии Vanta) позволяет быстро определить содержание тяжелых металлов для обеспечения соответствия стандартам RoHS 2.0.
Игра на наноуровне для контроля влажности
Гигроскопичность нейлоновых материалов делает их "чувствительными материалами" в процессе литья под давлением. В технической документации DuPont указано, что при содержании влаги в PA6 более 0,2% на поверхности изделия появляются серебристые разводы, а ударная прочность падает на 40%. Используется трехступенчатый метод сушки:
① Предварительная сушка при температуре 80℃ в течение 2 часов;
② Основная сушка при температуре 120℃ в течение 4 часов;
③ вакуумная сушка до содержания влаги ≤0,02%.
Оснащенный монитором точки росы (например, Motan LD50), можно отслеживать точку росы сухого воздуха в режиме реального времени (необходимо ≤-40℃), что является ключевой линией обороны для обеспечения качества литья нейлона под давлением.
Золотое сечение в разработке рецептур
Для литья под давлением автомобильных разъемов жгутов проводов рекомендованная компанией BASF формула Ultramid® A3WG10 содержит:
- Смола на основе PA66 67%
- Стекловолокно 30%
- Антиоксидант 1.5%
- Смазка 1.5%
Использование дозирующего смесителя с потерями в весе (например, Maguire серии WSB) позволяет достичь точности соотношения ±0,5%. Пример Американской ассоциации инжекционного формования показывает, что оптимизированная формула увеличивает срок службы разъема с 5 000 раз до 15 000 раз, при этом снижая уровень деформации деформации на 83%.
Интеллектуальная революция в области совместной работы с оборудованием
Современные системы литья под давлением обеспечивают связь параметров с помощью промышленного Интернета вещей:
- Контроль загрузки бункера (точность ±1 кг)
- Пятиступенчатый контроль температуры в бочке (рекомендация для PA66: 240-280℃)
- ПИД-регулировка скорости вращения шнека и противодавления Система Smart Power немецкого термопластавтомата Arburg показывает, что при колебании температуры бочки более чем на ±3℃ вязкость расплава изменяется на 15%. В это время система автоматически компенсирует давление впрыска (диапазон регулировки ±8%) для обеспечения стабильности литья.
Молекулярная реконструкция процесса плавления
На стадии пластификации при литье нейлона под давлением конструкция шнека напрямую влияет на расположение молекулярных цепей. Использование барьерных шнеков (например, серии HPM) позволяет повысить равномерность температуры расплава на 30% и снизить энергопотребление на 15%. Исследования швейцарской компании Buhler Group подтвердили, что выдержка расплава в бочке в течение 90-120 секунд позволяет достичь оптимального уровня кристалличности PA66 в диапазоне 45-50%, а также увеличить прочность на разрыв на 18%.
Заключение
В эпоху Индустрии 4.0 подготовка сырья превратилась из вспомогательного процесса в основное звено интеллектуального производства. По прогнозам Национального центра производственных наук США, к 2025 году интеллектуальная система подготовки сырья позволит снизить количество брака при литье под давлением на 75% и сократить время смены пресс-формы на 60%. Для таких высокоэффективных материалов, как нейлон, только создание полной системы знаний от молекулярного проектирования до управления процессом может обеспечить технологический ров в условиях жесткой рыночной конкуренции. Как сказал Патрик Фарри, президент Общества инженеров-пластмассовиков (SPE): "Будущее конкуренции в области литья под давлением начинается с миллиметров на станции подготовки сырья".