Introduction du nylon pour le moulage par injection
Dans le domaine de l'industrie plastique, le moulage par injection représente plus de 35% de la production mondiale de produits en plastique, et le contrôle de la qualité de la préparation des matières premières détermine directement le taux de qualification du produit final. Selon une étude réalisée en 2022 par l'Association américaine de l'industrie des plastiques (SPI), 68% des défauts de qualité dans le processus de moulage par injection sont liés à une mauvaise préparation des matières premières, et cette proportion est passée à 82% dans l'application des matériaux en nylon (PA). Cet article analyse en profondeur les six éléments clés du processus de moulage par injection. Matière première du nylon dans le processus de moulage par injection, révélant comment ce "processus invisible" affecte le marché des produits en plastique, qui représente des centaines de milliards.
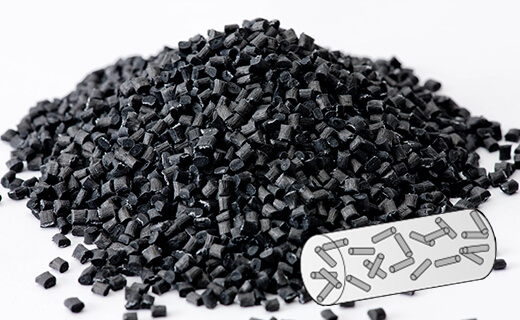
Sélection des matériaux moléculaires : adéquation précise des matières premières du nylon
En tant qu'"étalon-or" des plastiques techniques, les matériaux en nylon comprennent plus de 20 types de matériaux tels que PA6, PA66et PA12. Le livre blanc technique du géant allemand de la chimie BASF souligne que le point de fusion du PA66 (265°C) est supérieur de 15% à celui du PA6, et que la résistance à la traction est augmentée de 23%, mais que le taux d'absorption de l'humidité est également augmenté de 40%. Dans le moulage par injection de pièces de capot de moteur automobile, le choix du PA66-GF30 (contenant des fibres de verre 30%) peut rendre la résistance à la température supérieure à 200°C, soit 60°C de plus que le PA6 ordinaire. La sélection des matières premières doit tenir compte des propriétés mécaniques, de la stabilité thermique et des caractéristiques de traitement du produit final, et établir une matrice des paramètres de performance des matériaux.
Contrôle de qualité au micron : double ligne de défense pour l'inspection des matières premières
Les usines modernes de moulage par injection adoptent généralement un double mécanisme d'inspection :
① Inspection visuelle pour éliminer les particules hétérochromatiques (différence de couleur ΔE<1,5) ;
② Analyse granulométrique au laser pour s'assurer que la taille des particules est comprise entre 2 et 3 mm.
Les données expérimentales de Sumitomo Chemical (Japon) montrent qu'une taille de particule dépassant la norme de 0,5 mm augmente l'usure de la vis de la machine de moulage par injection de 17%, et que le mélange d'impuretés de 0,1% raccourcit la durée de vie des engrenages en nylon de 30%. L'utilisation de spectromètres XRF (tels que la série Olympus Vanta) permet de détecter rapidement la teneur en métaux lourds afin de garantir la conformité aux normes RoHS 2.0.
Jeu de contrôle de l'humidité au niveau nanométrique
Les propriétés hygroscopiques des matériaux en nylon en font des "matériaux sensibles" dans le processus de moulage par injection. Les documents techniques de DuPont montrent que lorsque la teneur en humidité du PA6 dépasse 0,2%, des stries argentées apparaissent à la surface du produit et la résistance aux chocs diminue de 40%. Une méthode de séchage en trois étapes est utilisée :
① 80℃ préséchage pendant 2 heures ;
② 120℃ séchage principal pendant 4 heures ;
③ séchage sous vide jusqu'à une teneur en humidité de ≤0,02%.
Équipé d'un moniteur de point de rosée (tel que Motan LD50), le point de rosée de l'air sec peut être surveillé en temps réel (nécessaire pour être ≤-40℃), ce qui est la ligne de défense clé pour assurer la qualité du moulage par injection de nylon.
Le nombre d'or de l'ingénierie de la formulation
Dans le moulage par injection de connecteurs de faisceaux de câbles automobiles, la formule Ultramid® A3WG10 recommandée par BASF contient.. :
- Résine de base PA66 67%
- Fibre de verre 30%
- Antioxydant 1.5%
- Lubrifiant 1.5%
L'utilisation d'un mélangeur doseur à perte de poids (tel que la série WSB de Maguire) permet d'obtenir une précision de rapport de ±0,5%. Le cas de l'American Injection Molding Association montre que la formule optimisée augmente la durée de vie du connecteur de 5 000 à 15 000 fois, tout en réduisant le taux de déformation par gauchissement de 83%.
Révolution intelligente de la collaboration en matière d'équipements
Les systèmes modernes de moulage par injection permettent de relier les paramètres grâce à l'Internet industriel des objets :
- Contrôle du chargement de la trémie (précision de ±1kg)
- Contrôle de la température de la barrique en cinq étapes (recommandation PA66 : 240-280℃).
- Réglage PID de la vitesse de la vis et de la contre-pression Le système Smart Power de la machine de moulage par injection allemande Arburg montre que lorsque la température du tonneau fluctue de plus de ±3℃, la viscosité de la matière fondue change de 15%. À ce moment-là, le système compense automatiquement la pression d'injection (plage de réglage ±8%) pour assurer la stabilité du moulage.
Reconstruction moléculaire du processus de fusion
Au cours de la phase de plastification du moulage par injection du nylon, la conception de la vis affecte directement l'arrangement des chaînes moléculaires. L'utilisation de vis barrières (telles que celles de la série HPM) peut améliorer l'uniformité de la température de la matière fondue de 30% et réduire la consommation d'énergie de 15%. Des recherches menées par le groupe suisse Buhler ont confirmé que le maintien de la matière fondue dans le tonneau pendant 90 à 120 secondes peut permettre à la cristallinité du PA66 d'atteindre la plage optimale de 45 à 50%, et à la résistance à la traction d'augmenter de 18%.
Conclusion
À l'ère de l'industrie 4.0, la préparation des matières premières est passée d'un processus auxiliaire au lien central de la fabrication intelligente. Le National Center for Manufacturing Sciences des États-Unis prévoit que d'ici 2025, le système intelligent de préparation des matières premières réduira le taux de rebut du moulage par injection de 75% et raccourcira le temps de changement de moule de 60%. Pour les matériaux à hautes performances tels que le nylon, ce n'est qu'en établissant un système de connaissances complet, de la conception moléculaire au contrôle des processus, qu'un fossé technologique pourra être creusé dans la concurrence féroce du marché. Comme l'a déclaré Patrick Farrey, président de la Society of Plastics Engineering (SPE) : "L'avenir de la concurrence dans le domaine du moulage par injection commence par des millimètres au niveau de la station de préparation des matières premières.