사출 성형용 나일론 소재 소개
플라스틱 산업 분야에서 사출 성형은 전 세계 플라스틱 제품 생산량의 35% 이상을 차지하며, 원료 준비의 품질 관리가 최종 제품 품질 인증률을 직접적으로 결정합니다. 미국 플라스틱 산업 협회(SPI)의 2022년 연구에 따르면 사출 성형 공정에서 68%의 품질 결함은 부적절한 원료 준비와 관련이 있으며, 나일론(PA) 소재 적용 시 이 비율은 82%로 증가했습니다. 이 기사에서는 다음의 6가지 핵심 요소를 심층적으로 분석합니다. 나일론 원료 사출 성형 공정의 준비 과정을 살펴보고, 이 '보이지 않는 공정'이 수천억 규모의 플라스틱 제품 시장에 어떤 영향을 미치는지 알아보세요.
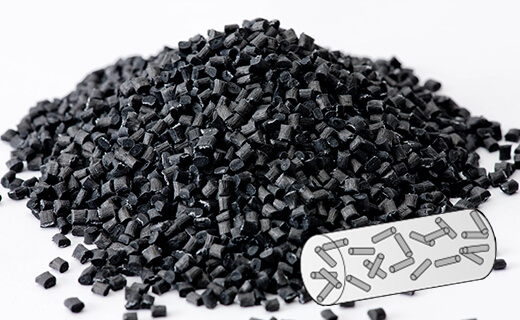
분자 소재 선택: 나일론 원재료의 정밀한 매칭
엔지니어링 플라스틱의 '골드 스탠다드'인 나일론 소재에는 다음과 같은 20가지 이상의 종류가 있습니다. PA6, PA66및 PA12. 독일 화학 대기업 BASF의 기술 백서에 따르면 PA66(265°C)의 융점은 PA6보다 15% 높고 인장 강도는 23% 증가하지만 수분 흡수율도 40% 증가한다고 지적했습니다. 자동차 엔진 후드 부품의 사출 성형에서 PA66-GF30 (30% 유리 섬유 포함)을 선택하면 온도 저항이 일반 PA6보다 60 ° C 높은 200 ° C를 초과 할 수 있습니다. 원자재 선택은 최종 제품의 기계적 특성, 열 안정성 및 가공 특성을 종합적으로 고려하고 재료 성능 매개 변수 매트릭스를 설정해야 합니다.
미크론 수준의 품질 관리: 원자재 검사를 위한 이중 방어선
최신 사출 성형 공장에서는 일반적으로 이중 검사 메커니즘을 채택합니다:
이색 입자(색차 ΔE<1.5)를 가려내기 위한 육안 검사;
레이저 입자 크기 분석으로 입자 크기가 2~3mm 범위인지 확인합니다.
일본 스미토모 화학의 실험 데이터에 따르면 입자 크기가 표준을 0.5mm 초과하면 사출 성형 머신 스크류의 마모가 17% 증가하고 0.1% 불순물이 혼합되면 나일론 기어의 피로 수명이 30% 단축되는 것으로 나타났습니다. XRF 분광기(예: 올림푸스 반타 시리즈)를 사용하면 중금속 함량을 빠르게 감지하여 RoHS 2.0 표준을 준수할 수 있습니다.
나노 수준의 습도 제어 게임
나일론 소재의 흡습성 특성으로 인해 사출 성형 공정에서 '민감한 소재'가 됩니다. 듀폰의 기술 문서에 따르면 PA6의 수분 함량이 0.2%를 초과하면 제품 표면에 은색 줄무늬가 나타나고 충격 강도가 40%까지 떨어집니다. 3단계 건조 방법이 사용됩니다:
80℃에서 2시간 동안 사전 건조합니다;
120℃에서 4시간 동안 메인 건조합니다;
수분 함량 ≤0.02%로 진공 건조.
이슬점 모니터(예: Motan LD50)를 장착하여 건조한 공기의 이슬점을 실시간으로 모니터링할 수 있으며(≤-40℃ 필요), 이는 나일론 사출 성형의 품질을 보장하는 핵심 방어선입니다.
포뮬레이션 엔지니어링의 황금 비율
자동차 와이어링 하니스 커넥터의 사출 성형에는 BASF가 권장하는 Ultramid® A3WG10 포뮬러가 사용됩니다:
- PA66 베이스 수지 67%
- 유리 섬유 30%
- 항산화제 1.5%
- 윤활유 1.5%
중량 손실 계량 믹서(예: Maguire WSB 시리즈)를 사용하면 ±0.5%의 비율 정확도를 달성할 수 있습니다. 미국 사출 성형 협회의 사례에 따르면 최적화된 공식을 통해 커넥터의 플러그인 수명을 5,000배에서 15,000배로 늘리면서 뒤틀림 변형률을 83%까지 줄인 것으로 나타났습니다.
장비 협업의 지능형 혁명
최신 사출 성형 시스템은 산업용 사물 인터넷을 통해 파라미터 연동을 실현합니다:
- 호퍼 적재 모니터링(±1kg 정확도)
- 5단계 배럴 온도 제어(PA66 권장: 240~280℃)
- 스크류 속도와 배압의 PID 조정 독일 아르부르크 사출기의 스마트 파워 시스템은 배럴 온도가 ±3℃ 이상 변동하면 용융 점도가 15%씩 변하는 것으로 나타났습니다. 이때 시스템이 사출 압력을 자동으로 보정(조정 범위 ±8%)하여 성형 안정성을 보장합니다.
용융 과정의 분자 재구성
나일론 사출 성형의 가소화 단계에서 나사 설계는 분자 사슬의 배열에 직접적인 영향을 미칩니다. 배리어 스크류(예: HPM 시리즈)를 사용하면 용융 온도의 균일성을 30%까지 개선하고 에너지 소비를 15%까지 줄일 수 있습니다. 스위스 뷸러 그룹의 연구에 따르면 용융물을 배럴에 90-120초 동안 보관하면 PA66의 결정성이 45-50%의 최적 범위에 도달하고 인장 강도가 18%까지 증가한다는 것이 확인되었습니다.
결론
인더스트리 4.0 시대에 원자재 준비는 보조 공정에서 지능형 제조의 핵심 연결 고리로 업그레이드되었습니다. 미국 국립 제조 과학 센터는 2025년까지 지능형 원자재 준비 시스템이 사출 성형 스크랩률을 75% 줄이고 금형 교체 시간을 60% 단축할 것으로 예측하고 있습니다. 나일론과 같은 고성능 소재의 경우 분자 설계부터 공정 제어까지 완벽한 지식 시스템을 구축해야만 치열한 시장 경쟁에서 기술 해자를 구축할 수 있습니다. 플라스틱 공학회(SPE)의 회장인 패트릭 패리는 다음과 같이 말했습니다: "사출 성형 경쟁의 미래는 원료 준비 스테이션의 밀리미터 단위에서 시작됩니다."