PA6 та PA12, також відомі під більш поширеними назвами нейлон 6 та нейлон 12, належать до сімейства поліамідних пластиків. Хоча вони мають певну схожість, між цими двома матеріалами є ключові відмінності, які впливають на їхню придатність для різних застосувань. Давайте заглибимося в ці відмінності, щоб зрозуміти, який з них краще підходить для ваших конкретних потреб.
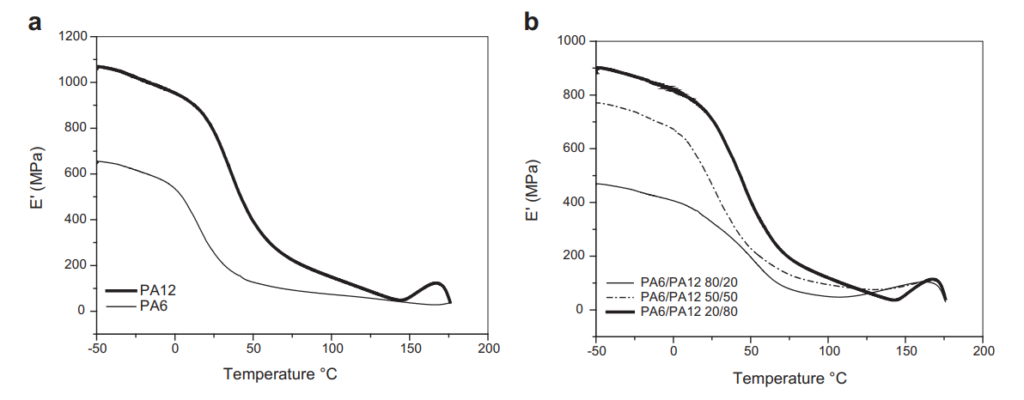
1. Казка про два джерела PA6 VS PA12
PA6 і PA12 побудовані з різних будівельних блоків, що впливає на їхні загальні властивості. В основі PA6 лежить комбінація адипінової кислоти та гексаметилендіаміну, які отримують за допомогою синтетичних хімічних процесів. На відміну від нього, PA12 використовує додецилдіоєву кислоту і додецилдіамін як основу, також отримані синтетичним шляхом.
2.Фізична доблесть: Акт балансування
PA6 вирізняється вражаючою міцністю, зносостійкістю та здатністю витримувати удари. Така універсальність робить його популярним вибором для широкого спектру загальнотехнічних застосувань. PA12, з іншого боку, вирізняється стійкістю до хімічних речовин і високих температур. Він також пропонує чудову жорсткість, але може демонструвати невелику тенденцію до крихкості порівняно з PA6.
3.Н2О Блюз: Битва проти водопоглинання
Одна з найважливіших відмінностей полягає у їх взаємодії з водою. PA6 має вищий показник водопоглинання, що може призвести до зміни його розмірів і зниження загальної продуктивності. PA12, однак, перевершує його в цій області завдяки своїм низьким властивостям водопоглинання. Це робить його більш стабільним варіантом для середовищ з високим рівнем вологості.
4.Міркування щодо витрат: Зважуємо вплив на гаманець
Як правило, PA6 є більш бюджетним варіантом через доступність сировини, з якої він виготовляється. З іншого боку, PA12 може бути дорожчим, оскільки сировина, що використовується для його виробництва, може бути дорожчою.
5.Там, де вони сяють: Відкриваємо ідеальні застосування
PA6 знаходить застосування в широкому спектрі галузей, включаючи загальні механічні деталі, компоненти в автомобільній промисловості, електричні пристрої та різні промислові матеріали. PA12, завдяки своїй чудовій хімічній і термостійкості, добре підходить для застосування в автомобільних паливних системах, пневматичних фітингах і кабельних оболонках.
6.Вплив на довкілля: Заклик до сталого розвитку
Оскільки PA6 синтезується переважно з нафтохімічної сировини, процес його виробництва може мати негативний вплив на навколишнє середовище. PA12, порівняно з PA6, може мати дещо менший вплив на навколишнє середовище під час виробництва.
7.Температура плавлення та обробка
PA6 зазвичай має нижчу температуру плавлення порівняно з PA12. Це дає переваги під час обробки такими методами, як лиття під тиском або 3D-друк. PA6 можна переробляти за дещо нижчих температур, що потенційно призводить до зменшення споживання енергії та потенційно меншої кількості деформацій або дефектів, пов'язаних з нагріванням, у кінцевому продукті.
8.Діелектричні властивості
PA6 має кращі діелектричні властивості порівняно з PA12. Це означає кращі електроізоляційні властивості, що робить PA6 більш підходящим вибором для застосувань, пов'язаних з електричними компонентами або такими, що вимагають хорошої стійкості до витоку електричного струму.
9.Вогнестійкість
Певні склади PA6 можуть бути вогнестійкими за своєю природою або легко модифікуватися для досягнення вогнестійкості. Це робить PA6 цінним матеріалом для застосувань, де пожежна безпека є критично важливою, наприклад, в електронних компонентах або будівельних матеріалах.
Остаточний вердикт: Обираємо чемпіона
Вибір між PA6 і PA12 залежить від конкретних вимог вашого застосування. Якщо вартість є основним фактором, що викликає занепокоєння, і задіяний широкий спектр інженерних застосувань, PA6 може бути ідеальним вибором. Однак, якщо хімічна стійкість, термостійкість і продуктивність у вологому середовищі мають першорядне значення, то кращим буде PA12. Зрештою, врахування як експлуатаційних характеристик, так і екологічних факторів допоможе вам вибрати найбільш підходящий матеріал для вашого проекту.