Впровадження нейлонового матеріалу для лиття під тиском
У галузі виробництва пластмас на лиття під тиском припадає понад 35% світового виробництва пластмасових виробів, а контроль якості підготовки сировини безпосередньо визначає рівень кваліфікації кінцевого продукту. Згідно з дослідженням Американської асоціації виробників пластмас (SPI), проведеним у 2022 році, 68% дефектів якості в процесі лиття під тиском пов'язані з неправильною підготовкою сировини, і ця частка зросла до 82% при застосуванні нейлонових (PA) матеріалів. У цій статті буде глибоко проаналізовано шість ключових елементів нейлонова сировина підготовки в процесі лиття під тиском, показуючи, як цей "невидимий процес" впливає на ринок пластикових виробів вартістю в сотні мільярдів.
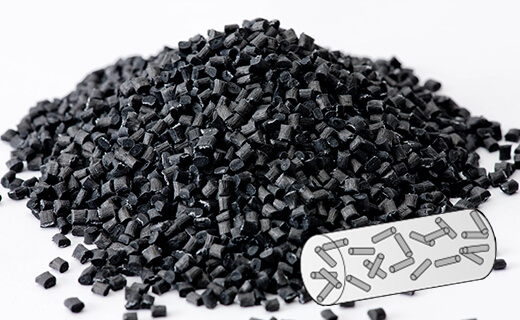
Молекулярний вибір матеріалу: точний підбір нейлонової сировини
Як "золотий стандарт" інженерних пластмас, нейлонові матеріали включають в себе більше 20 видів, таких як PA6, PA66і PA12. У технічному документі німецького хімічного гіганта BASF зазначається, що температура плавлення PA66 (265°C) на 15% вища, ніж у PA6, а міцність на розрив збільшується на 23%, але швидкість поглинання вологи також збільшується на 40%. При литті під тиском деталей капота автомобільного двигуна вибір PA66-GF30 (що містить скловолокно 30%) може зробити термостійкість вище 200°C, що на 60°C вище, ніж у звичайного PA6. При виборі сировини необхідно всебічно враховувати механічні властивості, термостійкість і технологічні характеристики кінцевого продукту, а також встановити матрицю параметрів експлуатаційних характеристик матеріалу.
Контроль якості на мікронному рівні: подвійна лінія захисту для перевірки сировини
Сучасні заводи з лиття під тиском, як правило, використовують механізм подвійного контролю:
① Візуальний огляд для відсіювання гетерохроматичних частинок (різниця кольорів ΔE<1,5);
Лазерний гранулометричний аналіз, щоб переконатися, що розмір частинок знаходиться в діапазоні 2-3 мм.
Експериментальні дані японської компанії Sumitomo Chemical показують, що розмір частинок, який перевищує стандарт на 0,5 мм, збільшує знос гвинта термопластавтомата на 17%, а змішування домішок 0,1% скорочує втомний ресурс нейлонових шестерень на 30%. Використання рентгенофлуоресцентних спектрометрів (наприклад, серії Olympus Vanta) дозволяє швидко виявити вміст важких металів для забезпечення відповідності стандартам RoHS 2.0.
Гра з контролем вологості на нанорівні
Гігроскопічні властивості нейлонових матеріалів роблять їх "чутливими матеріалами" в процесі лиття під тиском. Технічні документи DuPont показують, що коли вологість PA6 перевищує 0,2%, на поверхні виробу з'являються сріблясті прожилки, а ударна в'язкість падає на 40%. Використовується триступеневий метод сушіння:
① Попереднє сушіння при 80℃ протягом 2 годин;
② Основна сушка при 120℃ протягом 4 годин;
вакуумне сушіння до вмісту вологи ≤0,02%.
За допомогою монітора точки роси (наприклад, Motan LD50) можна відстежувати точку роси сухого повітря в режимі реального часу (повинна бути ≤-40 ℃), що є ключовою лінією захисту для забезпечення якості лиття під тиском нейлону.
Золотий перетин рецептурної інженерії
Для лиття під тиском роз'ємів автомобільних джгутів проводки використовується формула Ultramid® A3WG10, рекомендована компанією BASF:
- Базова смола PA66 67%
- Скловолокно 30%
- Антиоксидант 1.5%
- Мастило 1.5%
Використання дозуючого змішувача з втратою ваги (наприклад, серії Maguire WSB) дозволяє досягти точності співвідношення ±0,5%. Досвід Американської асоціації лиття під тиском показує, що оптимізована формула збільшує термін служби роз'єму від 5 000 до 15 000 разів, зменшуючи при цьому швидкість деформації викривлення на 83%.
Інтелектуальна революція у співпраці обладнання
Сучасні системи лиття під тиском забезпечують зв'язок параметрів через промисловий Інтернет речей:
- Контроль завантаження бункера (точність ±1 кг)
- П'ятиступеневе регулювання температури бочки (рекомендація PA66: 240-280℃)
- PID-регулювання швидкості шнека та протитиску Система Smart Power німецької термопластавтомата Arburg показує, що коли температура стовбура коливається більш ніж на ±3℃, в'язкість розплаву змінюється на 15%. У цей час система автоматично компенсує тиск впорскування (діапазон регулювання ±8%), щоб забезпечити стабільність формування.
Молекулярна реконструкція процесу плавлення
На етапі пластифікації при литті під тиском нейлону конструкція гвинта безпосередньо впливає на розташування молекулярних ланцюгів. Використання бар'єрних шнеків (наприклад, серії HPM) може поліпшити рівномірність температури розплаву на 30% і знизити споживання енергії на 15%. Дослідження швейцарської Buhler Group підтвердили, що витримка розплаву в циліндрі протягом 90-120 секунд дозволяє досягти оптимального діапазону кристалічності PA66 в 45-50%, а межа міцності на розрив збільшується на 18%.
Висновок
В епоху Індустрії 4.0 підготовка сировини перетворилася з допоміжного процесу на основну ланку інтелектуального виробництва. Національний центр виробничих наук США прогнозує, що до 2025 року інтелектуальна система підготовки сировини знизить рівень браку при литті під тиском на 75% і скоротить час заміни прес-форми на 60%. Для високоефективних матеріалів, таких як нейлон, лише шляхом створення повної системи знань від молекулярного дизайну до управління процесом можна побудувати технологічний рів в умовах жорсткої ринкової конкуренції. Як сказав Патрік Фаррі, президент Товариства інженерів з виробництва пластмас (SPE): "Майбутнє конкуренції в галузі лиття під тиском починається з міліметрів на станції підготовки сировини".