Introduktion
Nylon er et af de mest alsidige og udbredte syntetiske polymerer i verden i dag. Fra tøj til industrielle anvendelser gør dets bemærkelsesværdige styrke, fleksibilitet og holdbarhed det til et vigtigt materiale på tværs af forskellige industrier. Men bag fremstillingen ligger en kompleks proces kendt som nylonpolymerisation. At forstå, hvordan nylon syntetiseres, dets egenskaber og dets anvendelser, er afgørende for alle, der er interesserede i materialevidenskab eller industriel fremstilling.
Denne artikel udforsker nylonpolymerisationsprocessen i detaljer, undersøger de forskellige typer og anvendelser og besvarer nogle ofte stillede spørgsmål om produktion og genbrug. Uanset om du er studerende, ingeniør eller professionel i industrien, vil denne guide give dig værdifuld indsigt i et af de vigtigste materialer i moderne produktion.
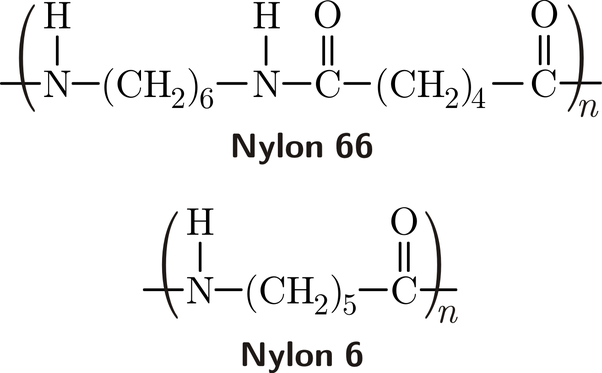
Forståelse af nylonpolymerisation
Definition af polymerisering
Polymerisering er den kemiske proces, hvor små molekyler, kendt som monomerer, bindes kemisk sammen til lange kæder eller polymerer. Den resulterende polymer har egenskaber, der adskiller sig fra de enkelte monomerers. I tilfældet med nylon involverer polymerisering sammenkædning af monomerer for at skabe en lang, fleksibel og holdbar kæde af gentagne enheder.
Nylonpolymerisation sker ved hjælp af to primære metoder: kondensationspolymerisation og additionspolymerisation. Begge metoder bruges i vid udstrækning til at skabe forskellige typer nylon, men kondensationspolymerisation er den mest almindelige proces til fremstilling af nylon.
Monomerernes rolle i dannelsen af nylon
I nylonpolymerisationsprocessen er monomererne typisk diaminer og dicarboxylsyrer. Diamin- og dicarboxylsyremolekylerne indeholder hver især funktionelle grupper, der er reaktive, så de kan binde sig sammen under polymerisationen. Den mest almindeligt anvendte diamin er hexamethylendiamin, mens den anvendte dicarboxylsyre er adipinsyre. Når disse monomerer gennemgår en polymerisation, danner de en gentagende enhed, der kaldes nylon-6,6.
Kombinationen af disse to monomerer skaber en stærk, fleksibel polymerkæde, som er karakteristisk for nylons imponerende mekaniske egenskaber.
Forskellige typer nylon og deres egenskaber
Nylon findes i flere varianter, der hver især egner sig til specifikke anvendelser. De mest almindelige typer er:
Nylon 66: Dette er den mest udbredte form for nylon. Den er kendt for sin styrke, holdbarhed og høje smeltepunkt, hvilket gør den ideel til anvendelser som tekstiler, bildele og industrielt udstyr.
Nylon 6: Nylon-6 fremstilles ved at polymerisere caprolactam og er lidt mere fleksibelt end nylon-6,6 og bruges ofte i tekstiler, reb og fiskenet.
Nylon 12: Med forbedret kemisk modstandsdygtighed og lavere vandabsorption bruges nylon-12 ofte i bildele, brændstofledninger og medicinsk udstyr.
Hver type nylon har specifikke egenskaber, der gør den velegnet til forskellige anvendelser, fra tekstiler til tekniske materialer.
Processen med polymerisering af nylon
Trin-for-trin-forklaring af nylonpolymerisationsprocessen
Nylonpolymerisation udføres typisk gennem en kondensationsreaktion med trinvis vækst, hvor monomerer kombineres for at danne lange kæder. Her er en trinvis gennemgang af processen:
Fremstilling af monomerer: Det første trin består i at fremstille monomererne, såsom hexamethylendiamin og adipinsyre, under kontrollerede forhold.
Polymerisationsreaktion: Monomererne opvarmes i nærvær af en katalysator. Reaktionen frigiver vandmolekyler, når diamin- og dicarboxylsyremolekylerne bindes sammen.
Dannelse af polymerkæder: Efterhånden som reaktionen skrider frem, fortsætter monomererne med at binde sig og danner lange polymerkæder. Polymerisationsreaktionen kan vare i flere timer for at sikre, at kæderne er tilstrækkeligt lange.
Afkøling og størkning: Når polymerkæderne er dannet, afkøles blandingen og størkner. Resultatet er et fast nylonmateriale, der kan videreforarbejdes til fibre, plader eller andre former.
Faktorer, der påvirker polymerisationsreaktionen
Flere faktorer påvirker effektiviteten og kvaliteten af nylonpolymerisationsprocessen:
Temperatur: Den temperatur, som polymerisationen foregår ved, påvirker reaktionshastigheden og molekylvægten af den nylon, der produceres. Høje temperaturer fremmer hurtigere polymerisation, men overdreven varme kan føre til nedbrydning.
Katalysatorer: Brugen af katalysatorer fremskynder reaktionen ved at sænke aktiveringsenergien, hvilket gør det lettere for monomererne at reagere og danne polymerkæder.
Monomer-koncentration: Koncentrationen af diamin og dicarboxylsyre påvirker reaktionshastigheden og slutproduktets egenskaber.
Reaktionstid: Den tid, reaktionen får lov til at forløbe, kan påvirke polymerens molekylvægt. Længere reaktionstider giver typisk nylon med højere molekylvægt og bedre mekaniske egenskaber.
Udfordringer og overvejelser i nylonproduktionen
Selv om nylonpolymerisation er en veletableret proces, er der flere udfordringer i produktionen. Et af de største problemer er frigivelsen af vand under kondensationspolymerisationen. Dette biprodukt kan påvirke nylonens kvalitet, hvis det ikke håndteres omhyggeligt. Derudover kræver det præcis kontrol over reaktionsbetingelserne at opnå den ønskede molekylvægt og polymerkædelængde.
En anden overvejelse er energiforbruget i forbindelse med nylonproduktion. De høje temperaturer, der kræves til polymerisering, kan være energikrævende, hvilket giver anledning til bekymring for nylonproduktionens miljøpåvirkning.
Anvendelser af nylonpolymerisation
Almindelige anvendelser af nylon i forskellige brancher
Nylon er et meget alsidigt materiale, og dets polymeriseringsproces gør det muligt at bruge det til en lang række formål. Nogle af de mest almindelige anvendelser omfatter:
Tekstiler: Nylon bruges i vid udstrækning i modeindustrien til fremstilling af slidstærke, lette stoffer, herunder tøj, strømper og polstring.
Biler: Nylon bruges i produktionen af forskellige bildele, f.eks. gear, motorkomponenter og brændstofledninger, på grund af dets styrke og modstandsdygtighed over for slid.
Industrielt udstyr: Nylons modstandsdygtighed over for slid og stød gør det til et ideelt valg til lejer, bøsninger og transportbånd.
Medicinsk udstyr: Nylon bruges til medicinske formål som kirurgiske suturer, medicinske slanger og proteser på grund af dets biokompatibilitet og holdbarhed.
Fordele ved nylon frem for andre materialer
Nylon har flere fordele i forhold til andre materialer som metaller og naturfibre:
Styrke og holdbarhed: Nylon er kendt for sin overlegne trækstyrke, hvilket gør det ideelt til applikationer med høj belastning.
Letvægt: På trods af sin styrke er nylon let, hvilket gør det perfekt til anvendelser, hvor vægt er et problem, f.eks. i luftfarts- og bilindustrien.
Kemisk modstandsdygtighed: Nylon er modstandsdygtigt over for en lang række kemikalier, olier og opløsningsmidler, hvilket gør det anvendeligt i barske miljøer.
Fremtidsudsigter for nylonpolymerisationsteknologi
I takt med at efterspørgslen efter bæredygtige materialer vokser, undersøger forskere, hvordan man kan forbedre nylonpolymerisationsprocessen. Innovationer som biobaseret nylon, der er fremstillet af vedvarende ressourcer som ricinusbønner, vinder frem. Disse alternativer har til formål at reducere miljøpåvirkningen fra nylonproduktion, samtidig med at de ønskede egenskaber bevares.
Desuden forbedrer fremskridt inden for genbrugsteknologier genanvendeligheden af nylonprodukter, hvilket bidrager til en mere cirkulær økonomi.
Ofte stillede spørgsmål
1. Hvad er forskellen mellem kondensations- og additionspolymerisation?
Kondensationspolymerisation involverer eliminering af et lille molekyle, typisk vand, når monomererne bindes sammen. I modsætning hertil involverer additionspolymerisation ikke frigivelse af nogen biprodukter. Begge processer bruges til at skabe forskellige typer nylon, hvor kondensationspolymerisation er den mest almindelige til fremstilling af nylon-6,6.
2. Hvordan adskiller nylonpolymerisation sig fra andre polymerisationsprocesser?
Nylonpolymerisation er en specifik type kondensationspolymerisation, der kræver en kombination af diaminer og dicarboxylsyrer. I modsætning til andre polymerisationsprocesser, som f.eks. dem, der bruges til polyethylen, resulterer nylonpolymerisation i et materiale med fremragende mekaniske egenskaber, kemisk resistens og varmebestandighed.
3. Kan nylon genbruges efter polymerisering?
Ja, nylon kan genbruges gennem forskellige processer, herunder mekanisk genbrug, hvor gamle nylonprodukter nedbrydes og omdannes til nye materialer. Effektiviteten af genanvendelse af nylon afhænger dog af den specifikke nylontype og kvaliteten af genanvendelsesprocessen.
Konklusion
Nylonpolymerisation er en afgørende proces, der resulterer i et af de mest udbredte og alsidige materialer i moderne industrier. Fra de første monomerer til det endelige produkt er processen med at skabe nylon kompleks og kræver omhyggelig kontrol af forskellige faktorer. De forskellige anvendelser af nylon - fra tekstiler til bildele - viser dets betydning på tværs af forskellige sektorer. Efterhånden som teknologien udvikler sig, kan vi forvente yderligere innovationer inden for produktion og genbrug af nylon, hvilket sikrer, at dette materiale forbliver en nøglespiller i produktionsverdenen i de kommende år.